Unlocking Efficiency: The Role of Twin Screw Compounders in Modern Plastics Processing
2025-07
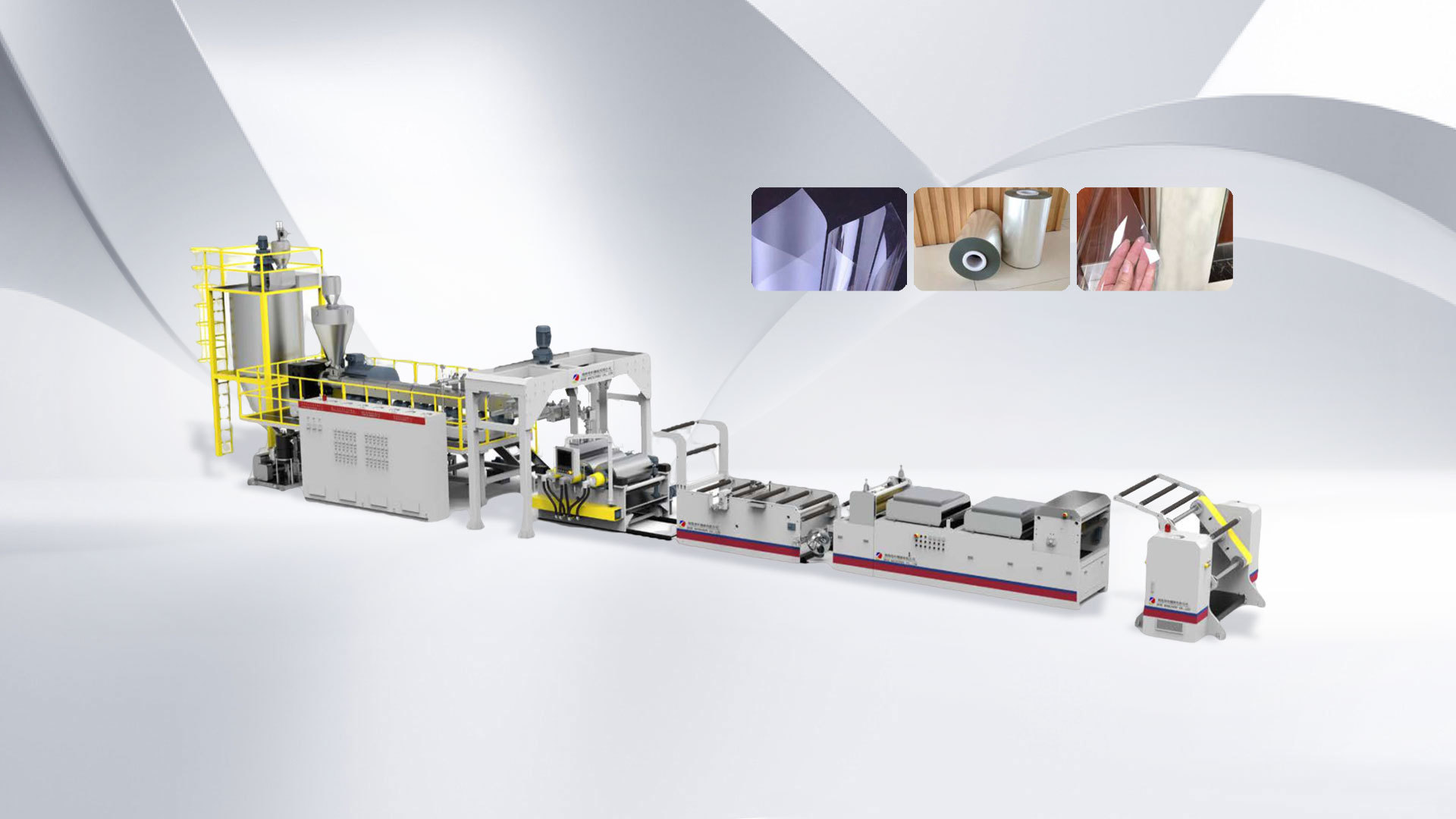
Unlocking Efficiency: The Role of Twin Screw Compounders in Modern Plastics Processing
Table of Contents
- Introduction to Twin Screw Compounders
- Understanding Plastics Processing
- What Are Twin Screw Compounders?
- Advantages of Twin Screw Compounders in Plastics Processing
- Applications of Twin Screw Compounders
- Operating Principles of Twin Screw Compounders
- Maintenance and Support for Twin Screw Compounders
- Future Trends in Twin Screw Compounding Technology
- Conclusion
- Frequently Asked Questions
Introduction to Twin Screw Compounders
In the rapidly evolving landscape of plastics manufacturing, the demand for innovative solutions has never been greater. **Twin screw compounders**, a cornerstone of modern plastics processing, offer unparalleled efficiency and versatility. By harnessing the power of advanced technology, these machines are transforming the way plastics are compounded, modified, and processed. This article explores the critical role of twin screw compounders within this industry, emphasizing their importance in boosting productivity, enhancing product quality, and driving innovation.
Understanding Plastics Processing
Plastics processing encompasses a variety of methods used to shape, mold, and enhance plastic materials. These techniques include extrusion, injection molding, blow molding, and thermoforming, each serving unique purposes in the manufacturing of plastic products.
**Extrusion**, in particular, plays a significant role in creating plastic films, sheets, and various shapes. Twin screw compounders excel in this area by facilitating the mixing, melting, and compounding processes necessary for producing high-quality plastic materials.
What Are Twin Screw Compounders?
Twin screw compounders are sophisticated machines that consist of two intermeshing screws rotating within a barrel. These screws work in tandem to process and mix various polymer materials with additives, fillers, and colorants.
The unique design allows for efficient material transportation, dispersion, and reaction, making twin screw compounders an essential tool in the plastics processing industry. Unlike single screw extruders, twin screw compounders offer better control over the material processing environment, which is crucial for achieving desired product characteristics.
Key Features of Twin Screw Compounders
- **Intermeshing Screws**: The design of the screws allows for enhanced mixing and pumping efficiency.
- **Modular Design**: Many twin screw compounders are modular, enabling customization for specific applications.
- **Temperature Control**: Advanced temperature controls help maintain optimal processing conditions.
- **Versatility**: They can process a wide range of materials, from thermoplastics to thermosets.
Advantages of Twin Screw Compounders in Plastics Processing
The integration of twin screw compounders into plastics processing offers numerous advantages that contribute to increased efficiency and improved product quality.
1. Enhanced Mixing and Compounding
The intermeshing design of twin screw compounders ensures optimal mixing of polymers and additives. This results in uniform dispersion, which is vital for achieving consistent product quality.
2. Improved Process Control
Advanced control systems allow operators to monitor and adjust processing parameters in real time. This leads to better product characteristics and reduces material waste.
3. Greater Flexibility
Twin screw compounders can handle a wide variety of materials, enabling manufacturers to adapt quickly to changing market demands. Whether producing biodegradable plastics or engineering thermoplastics, these machines can accommodate diverse formulations.
4. Higher Throughput
The design and functionality of twin screw compounders enable higher production rates compared to traditional methods. This efficiency is crucial for meeting market demands and improving profitability.
5. Efficient Heat Transfer
Twin screw compounders are designed to provide excellent heat transfer, which is crucial for the melting and processing of polymers. This efficiency helps reduce energy consumption and processing times.
Applications of Twin Screw Compounders
Twin screw compounders are utilized across various sectors within the plastics industry, showcasing their versatility and effectiveness.
1. Polymer Modification
These machines are often employed to modify existing polymers by blending them with additives to enhance properties such as strength, flexibility, and thermal stability.
2. Masterbatch Production
In the production of masterbatches—concentrated mixtures of pigments or additives with polymers—twin screw compounders ensure thorough dispersion and uniformity.
3. Production of Nanocomposites
Nanocomposites, which incorporate nanoparticles into polymers, benefit from the superior mixing capabilities of twin screw compounders, resulting in enhanced mechanical and thermal properties.
4. Recycling Processes
In the realm of plastics recycling, twin screw compounders play a crucial role in reprocessing post-consumer materials, helping to create new products from recycled content.
5. Bioplastics Development
As the industry shifts towards sustainable materials, twin screw compounders are instrumental in developing bioplastics, allowing for the effective blending of natural polymers with conventional plastics.
Operating Principles of Twin Screw Compounders
Understanding the operational mechanics behind twin screw compounders is essential for maximizing their efficiency.
1. Feed Mechanism
Materials are introduced into the machine through a feed hopper, where they are drawn into the barrel by the rotating screws.
2. Melting and Mixing
As materials travel through the barrel, they are subjected to heat from the barrel and friction from the screws, leading to melting and mixing.
3. Dosage of Additives
Additives, such as colorants or stabilizers, can be introduced at various points in the process for optimal mixing.
4. Venting and Degassing
Excess moisture or volatile compounds can be removed during processing through venting ports, which helps improve product quality.
5. Discharge and Pelletizing
Once the desired material characteristics are achieved, the finished product exits the machine, often requiring further processing such as pelletizing.
Maintenance and Support for Twin Screw Compounders
To ensure optimal performance and longevity, regular maintenance is essential for twin screw compounders.
1. Routine Inspections
Regular inspections of the screw elements and barrel are crucial for identifying wear and tear that could impact performance.
2. Cleaning Protocols
Implementing effective cleaning protocols is vital to prevent contamination between different batch runs.
3. Spare Parts Management
Maintaining an inventory of critical spare parts helps minimize downtime during maintenance or repairs.
4. Training and Support
Investing in operator training and support ensures that personnel can effectively operate and maintain the machinery.
Future Trends in Twin Screw Compounding Technology
As technology continues to evolve, several trends are emerging that will shape the future of twin screw compounding in plastics processing.
1. Automation and Smart Technology
The integration of automation and smart technology will enhance process control, leading to improved efficiency and reduced labor costs.
2. Sustainable Practices
With a growing focus on sustainability, twin screw compounders will increasingly be used to develop eco-friendly materials and facilitate recycling processes.
3. Advanced Materials Development
As the demand for high-performance materials grows, twin screw compounders will play a pivotal role in the development of advanced composites and engineered plastics.
4. Increased Customization
Manufacturers are expected to invest in customizable twin screw compounders that can be tailored to specific applications, allowing for greater flexibility in production.
Conclusion
Twin screw compounders have emerged as a critical component in modern plastics processing, unlocking new levels of efficiency and innovation. By combining advanced technology with versatile applications, these machines are setting the standard for quality and productivity in the industry. As the demand for sustainable and high-performance materials continues to grow, twin screw compounders will undoubtedly play an integral role in shaping the future of plastics processing.
Frequently Asked Questions
1. What is the primary function of a twin screw compounder?
The primary function of a twin screw compounder is to mix, melt, and process various polymers and additives to create new materials with tailored properties.
2. How does a twin screw compounder differ from a single screw extruder?
Twin screw compounders feature two intermeshing screws that provide superior mixing and control compared to single screw extruders, which typically use a single screw for processing.
3. What industries benefit from twin screw compounding technology?
Twin screw compounding technology benefits various industries, including automotive, packaging, electronics, and medical devices, among others.
4. How can I ensure optimal performance from my twin screw compounder?
Regular maintenance, proper training for operators, and adherence to cleaning protocols can help ensure optimal performance from your twin screw compounder.
5. Are twin screw compounders suitable for recycling processes?
Yes, twin screw compounders are highly effective in recycling processes, allowing for the reprocessing of post-consumer materials into new products.
RELATED INFORMATION
Understanding PET Sheet Extruder Machines: A Comprehensive Guide
PET sheet extruder machines are specialized equipment used in the plastic processing industry to produce sheets made from polyethylene terephthalate (PET). These machines play a crucial role in various applications, including packaging, automotive parts, and consumer goods. Understanding how these machines work, their components, and their applications can help manufacturers improve efficiency and
Exploring the Efficiency of PET Single Screw Extruders in Manufacturing
Exploring the Efficiency of PET Single Screw Extruders in Manufacturing Table of Contents 1. Introduction to PET Single Screw Extruders 2. The Importance of PET in the Manufacturing Process 3. Design and Mechanism of Single Screw Extruders 4. Efficiency Factors of PET Single Screw Extruders 5. Applications of PET Single Screw Extruders in Manufacturing 6. Maintenance and O