Exploring the Efficiency of PET Single Screw Extruders in Manufacturing
2025-07
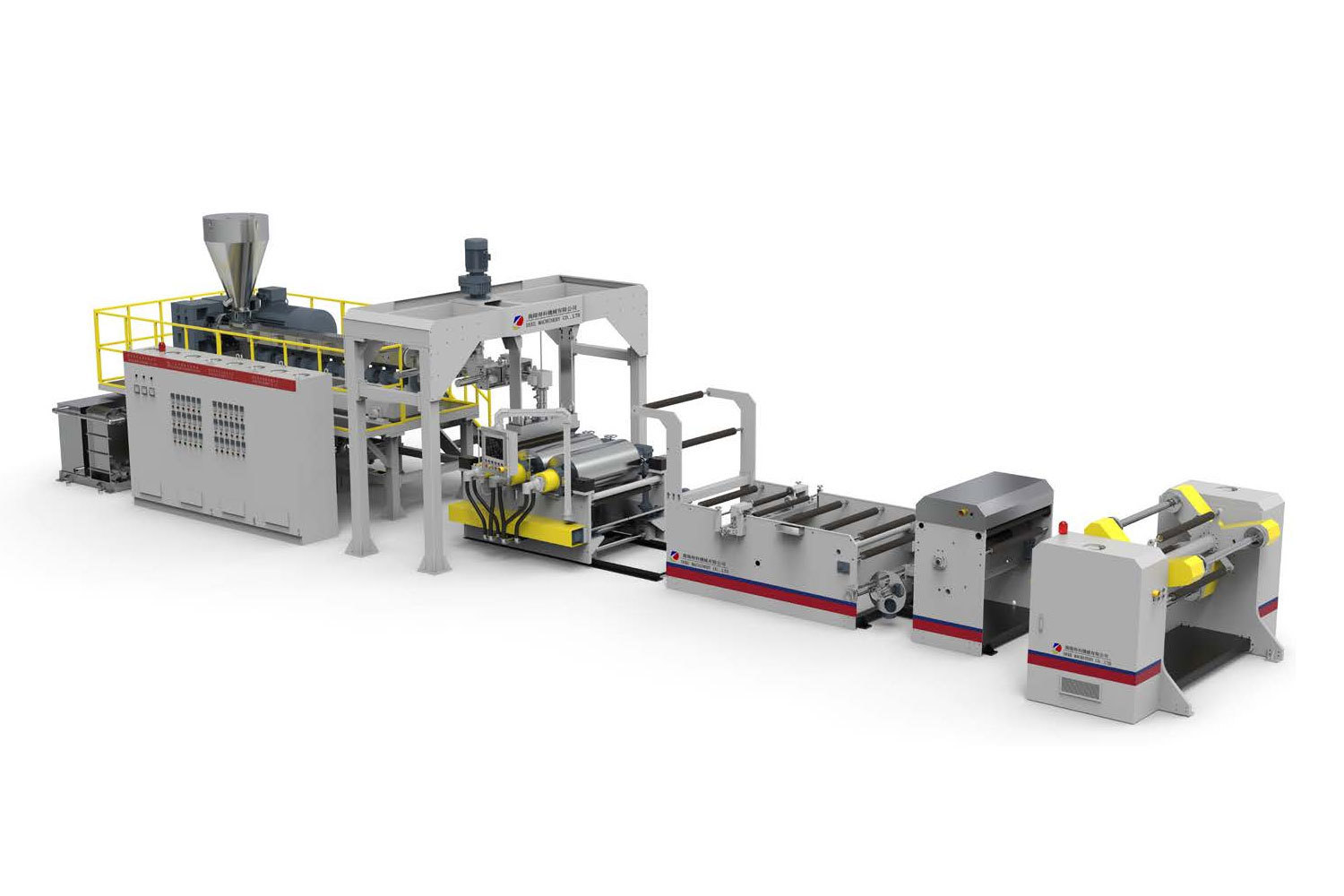
Exploring the Efficiency of PET Single Screw Extruders in Manufacturing
Table of Contents
- 1. Introduction to PET Single Screw Extruders
- 2. The Importance of PET in the Manufacturing Process
- 3. Design and Mechanism of Single Screw Extruders
- 4. Efficiency Factors of PET Single Screw Extruders
- 5. Applications of PET Single Screw Extruders in Manufacturing
- 6. Maintenance and Optimization of Extruders
- 7. The Future of PET Single Screw Extruders
- 8. Frequently Asked Questions (FAQs)
1. Introduction to PET Single Screw Extruders
The evolution of manufacturing processes has significantly benefited from advancements in machinery. Among these advancements, **PET single screw extruders** stand out as a vital technology in the production of plastic materials. These machines play a crucial role in converting raw materials into finished products with superior properties, especially in industries like packaging, automotive, and textiles.
2. The Importance of PET in the Manufacturing Process
Polyethylene Terephthalate (PET) is a widely used thermoplastic polymer known for its excellent strength-to-weight ratio, chemical resistance, and transparency. Its applications range from bottles to films and fibers. The importance of PET in manufacturing can be attributed to its recyclability, making it a preferred choice for environmentally conscious manufacturers. Furthermore, the capability of **single screw extruders** to process PET efficiently has made them essential in modern production lines.
2.1 Benefits of Using PET
- Durability: PET's robustness ensures long-lasting products.
- Lightweight: This property helps in reducing transportation costs.
- Recyclability: PET can be recycled multiple times without losing integrity.
3. Design and Mechanism of Single Screw Extruders
A **single screw extruder** comprises a rotating screw embedded within a heated barrel. This design allows for efficient melting, mixing, and shaping of the PET resin. Understanding the components and their functions is crucial for manufacturers aiming to optimize the extrusion process.
3.1 Key Components
- Screw: The screw's design influences the melting and mixing efficiency.
- Barrel: The heated barrel maintains the necessary temperature for PET processing.
- Die: The die shapes the extruded material into the desired profile.
3.2 Operational Principles
The operation of single screw extruders involves several phases: feeding, melting, mixing, and extrusion. During feeding, PET pellets are introduced into the hopper and conveyed through the screw. As the screw rotates, friction and heat melt the pellets, leading to a homogenous melt. This melt is then forced through the die, where it takes shape according to the desired product specifications.
4. Efficiency Factors of PET Single Screw Extruders
Efficiency in manufacturing is paramount, and several factors influence the performance of PET single screw extruders. Understanding these factors can lead to improved productivity and reduced operational costs.
4.1 Temperature Control
Maintaining optimal temperature throughout the extrusion process is critical. Too low a temperature can result in poor melting, while excessive heat can degrade the material. Implementing accurate temperature control systems enhances the melt quality and reduces waste.
4.2 Screw Design
The geometry of the screw, including its diameter, pitch, and depth, significantly affects the efficiency of the extrusion process. Customized screw designs can lead to better mixing and melting, ultimately improving throughput.
4.3 Material Properties
The intrinsic properties of PET, such as viscosity and flow rate, play a significant role in the extrusion process. Adjusting the formulation of PET can enhance the performance of the extruder and lead to higher-quality outputs.
5. Applications of PET Single Screw Extruders in Manufacturing
Single screw extruders are versatile and find applications across various industries. The ability to produce a wide range of products makes them integral to modern manufacturing.
5.1 Packaging
One of the most prominent uses of PET is in packaging. Single screw extruders efficiently produce PET sheets and films, which are then used for food and beverage containers, enhancing shelf life and ensuring product safety.
5.2 Automotive Components
PET's durability and lightweight nature make it suitable for automotive applications. Extruded PET components contribute to the overall efficiency of vehicles, reducing fuel consumption.
5.3 Textiles and Fibers
PET is also used in the textile industry, where it is extruded into fibers for clothing and upholstery. The flexibility and strength of PET fibers make them ideal for various fabric applications.
6. Maintenance and Optimization of Extruders
Regular maintenance of PET single screw extruders is essential for sustaining efficiency and prolonging the lifespan of the machinery. Here are key strategies for optimizing performance:
6.1 Routine Inspections
Conducting routine inspections of the screw, barrel, and die can identify wear and tear early, preventing costly downtimes and ensuring consistent production quality.
6.2 Lubrication
Proper lubrication reduces friction between moving parts, ensuring smooth operation and minimizing energy consumption. Establishing a lubrication schedule is crucial for long-term performance.
6.3 Process Monitoring
Implementing process monitoring systems allows for real-time tracking of operational parameters, leading to quicker adjustments and enhanced efficiency. This technology can also predict maintenance needs before they lead to equipment failure.
7. The Future of PET Single Screw Extruders
As industries continue to evolve, the future of PET single screw extruders looks promising. Innovations in technology are expected to enhance their efficiency further, making them more environmentally friendly and cost-effective.
7.1 Advancements in Materials
The development of new PET formulations that further improve processing capabilities will likely emerge, optimizing the extrusion process.
7.2 Smart Manufacturing
The integration of smart technologies, such as IoT and AI, into the operation of PET single screw extruders can lead to significant improvements in efficiency and productivity. These advancements will enable manufacturers to respond swiftly to market changes and consumer demands.
8. Frequently Asked Questions (FAQs)
8.1 What is the main advantage of using a single screw extruder for PET processing?
The primary advantage lies in its simplicity and effectiveness in processing PET, leading to consistent quality and high throughput.
8.2 How does the design of the screw impact efficiency?
The screw design affects melting, mixing, and overall flow characteristics, thus significantly influencing the efficiency of the extrusion process.
8.3 Can PET single screw extruders be used for other materials?
Yes, while they are optimized for PET, these extruders can process various thermoplastic materials with appropriate adjustments.
8.4 How often should maintenance be performed on PET extruders?
Regular inspections should be conducted weekly, with comprehensive maintenance performed quarterly or bi-annually, depending on usage.
8.5 What is the expected lifespan of a PET single screw extruder?
With proper maintenance, a PET single screw extruder can last several years, often exceeding a decade in optimal operating conditions.
Conclusion
The efficiency of **PET single screw extruders** in manufacturing cannot be overstated. By understanding their design, operational principles, and maintenance needs, manufacturers can significantly optimize their production processes. As technology advances, the future holds great promise for further enhancements in these essential pieces of machinery, paving the way for more sustainable and efficient manufacturing practices.
RELATED INFORMATION
Understanding PET Sheet Extruder Machines: A Comprehensive Guide
PET sheet extruder machines are specialized equipment used in the plastic processing industry to produce sheets made from polyethylene terephthalate (PET). These machines play a crucial role in various applications, including packaging, automotive parts, and consumer goods. Understanding how these machines work, their components, and their applications can help manufacturers improve efficiency and
Exploring the Efficiency of PET Single Screw Extruders in Manufacturing
Exploring the Efficiency of PET Single Screw Extruders in Manufacturing Table of Contents 1. Introduction to PET Single Screw Extruders 2. The Importance of PET in the Manufacturing Process 3. Design and Mechanism of Single Screw Extruders 4. Efficiency Factors of PET Single Screw Extruders 5. Applications of PET Single Screw Extruders in Manufacturing 6. Maintenance and O