A Comprehensive Guide to HIPS Sheet Co-Extruder Technology: Unlocking Efficiency and Quality in Plastic Manufacturing
2025-07
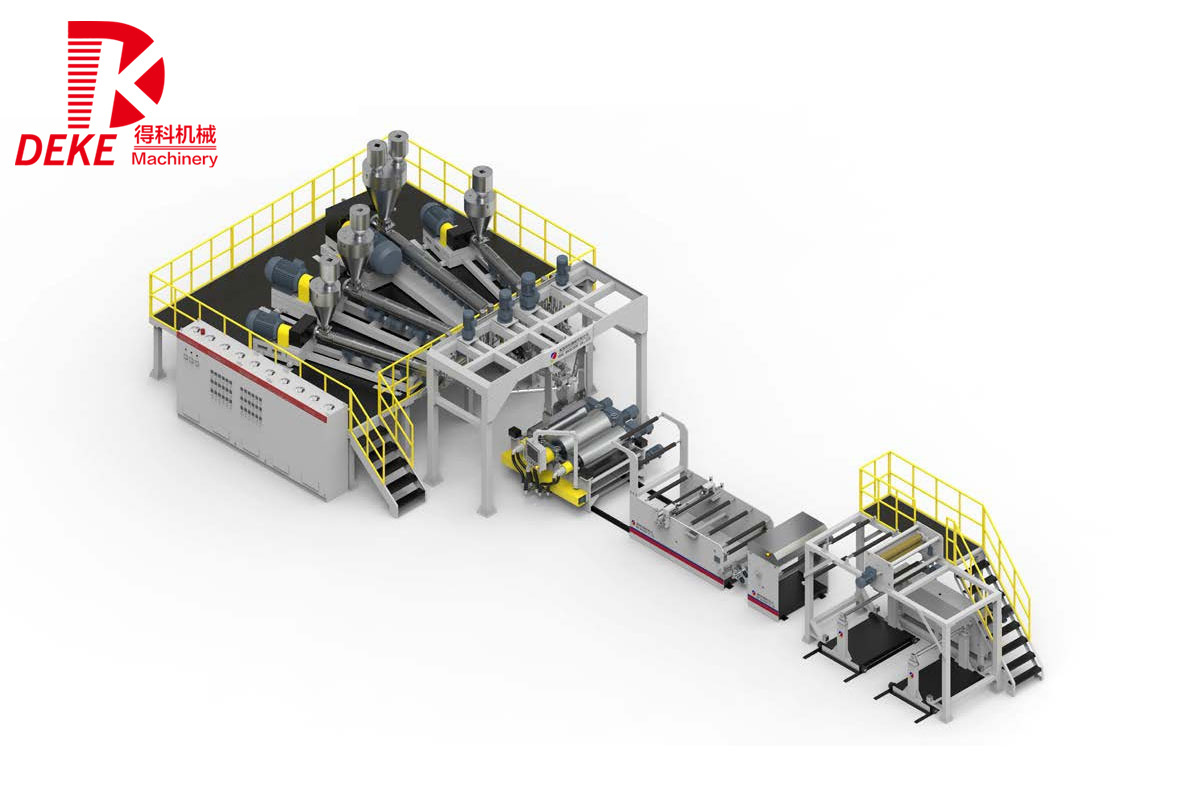
A Comprehensive Guide to HIPS Sheet Co-Extruder Technology
In the dynamic landscape of plastic manufacturing, understanding **HIPS sheet co-extruder technology** is crucial for optimizing production processes and enhancing product quality. This guide will explore the intricacies of co-extrusion, its advantages, applications, and the technical aspects that every manufacturer should know.
Table of Contents
- 1. Introduction to HIPS Sheet Co-Extrusion
- 2. What is HIPS?
- 3. The Co-Extrusion Process Explained
- 4. Advantages of HIPS Sheet Co-Extrusion
- 5. Applications of HIPS Sheet Co-Extruders
- 6. Key Components of HIPS Co-Extruder Systems
- 7. Tips for Optimizing HIPS Co-Extrusion
- 8. FAQs About HIPS Sheet Co-Extruder Technology
- 9. Conclusion
1. Introduction to HIPS Sheet Co-Extrusion
Co-extrusion is a sophisticated manufacturing process that allows for the simultaneous extrusion of two or more different materials. This technique is particularly significant in the production of HIPS (High Impact Polystyrene) sheets, which are widely used in various applications due to their excellent impact resistance, rigidity, and ease of processing. This guide aims to provide a comprehensive understanding of HIPS sheet co-extruder technology, highlighting its importance in the plastic manufacturing industry.
2. What is HIPS?
High Impact Polystyrene (HIPS) is a versatile thermoplastic known for its outstanding toughness and ease of fabrication. It is a copolymer made from styrene and polybutadiene, giving it enhanced impact resistance compared to standard polystyrene. HIPS is often used in applications such as:
- **Packaging materials**
- **Consumer electronics**
- **Automotive parts**
- **Household goods**
The adaptability of HIPS makes it a favored choice for manufacturers looking to produce durable and lightweight products.
3. The Co-Extrusion Process Explained
The co-extrusion process involves multiple extruders working in tandem to produce a multilayer film or sheet. In the context of HIPS sheet production, the process typically consists of the following steps:
3.1 Material Preparation
The first step involves selecting and preparing the raw materials. For HIPS co-extrusion, manufacturers often combine HIPS with other polymers to enhance specific properties such as barrier performance, aesthetics, or cost-effectiveness.
3.2 Feeding and Melting
Once the materials are prepared, they are fed into the extruders, where they are heated to their melting point. Each extruder operates at a specific temperature to ensure optimal melting of the respective polymers.
3.3 Layering
As the molten materials exit the extruders, they are layered together to form a single sheet. The layers can vary in thickness, and the combination of different materials allows for the creation of products with unique properties.
3.4 Cooling and Solidifying
The co-extruded sheet is then passed through a cooling system, where it solidifies. This step is crucial for maintaining the integrity of the layers and ensuring a high-quality finished product.
4. Advantages of HIPS Sheet Co-Extrusion
Implementing HIPS sheet co-extrusion technology presents numerous advantages for manufacturers:
4.1 Enhanced Material Properties
Co-extrusion allows the combination of different materials, resulting in products with improved characteristics. For example, adding a barrier layer can enhance moisture and gas resistance.
4.2 Cost Efficiency
By using co-extrusion, manufacturers can optimize their material usage, reducing waste and costs associated with secondary processing. This efficiency translates to more competitive pricing for end products.
4.3 Improved Aesthetics
Co-extruded sheets can be produced in various colors and finishes, allowing manufacturers to cater to diverse market demands. This flexibility is vital for branding and consumer appeal.
4.4 Reduced Processing Time
The ability to produce multilayer products in a single pass means that co-extrusion significantly reduces production times compared to traditional methods that may require multiple processing stages.
5. Applications of HIPS Sheet Co-Extruders
HIPS sheet co-extrusion technology finds applications across various industries, including:
5.1 Packaging Solutions
HIPS sheets are frequently used in food packaging due to their durability and barrier properties. Co-extruded sheets can be tailored to meet specific regulatory and performance requirements.
5.2 Electronics
The electronics industry benefits from HIPS co-extruded materials for producing lightweight housings that provide excellent protection for sensitive components.
5.3 Automotive Components
In the automotive sector, HIPS is used for interior trim, dashboards, and other components where durability and aesthetics are paramount. Co-extruded layers can enhance impact resistance and reduce weight.
5.4 Consumer Goods
From toys to kitchenware, HIPS sheets are widely utilized in consumer products. The co-extrusion process allows for innovative designs that appeal to consumer trends.
6. Key Components of HIPS Co-Extruder Systems
Understanding the essential components of HIPS co-extruder systems is crucial for optimizing performance:
6.1 Extruders
Each extruder must be selected based on the specific materials being processed. They should have precise temperature control and consistent feed rates to ensure uniformity in the final product.
6.2 Die Systems
The die system is responsible for shaping the co-extruded output. A well-designed die is critical for achieving the desired thickness and layer distribution.
6.3 Cooling Systems
Effective cooling systems ensure rapid solidification of the co-extruded sheet, preserving the integrity of the layers. This is essential for preventing defects and maintaining product quality.
6.4 Control Systems
Advanced control systems enable real-time monitoring of the extrusion process, allowing for quick adjustments to maintain consistent quality and performance.
7. Tips for Optimizing HIPS Co-Extrusion
To maximize the benefits of HIPS sheet co-extrusion, consider the following optimization strategies:
7.1 Material Selection
Choose compatible materials that complement each other and enhance the desired properties of the final product. Conduct thorough testing to ensure optimal performance.
7.2 Process Parameters
Regularly monitor and adjust process parameters such as temperature, pressure, and feed rates to maintain consistent quality and reduce defects.
7.3 Maintenance
Implement a proactive maintenance schedule for your extruder systems. Regular checks can prevent downtime and ensure long-term performance.
7.4 Staff Training
Invest in training for your staff to ensure they are familiar with operating and troubleshooting co-extruder systems. A knowledgeable team can significantly enhance efficiency and product quality.
8. FAQs About HIPS Sheet Co-Extruder Technology
8.1 What is the difference between co-extrusion and single extrusion?
Co-extrusion involves multiple materials being extruded simultaneously to create multilayer products, while single extrusion uses one type of material.
8.2 Can HIPS be co-extruded with other materials?
Yes, HIPS can be co-extruded with various materials to enhance specific properties, such as barrier performance or aesthetic appeal.
8.3 What are the common challenges in HIPS co-extrusion?
Challenges may include material compatibility, layer adhesion issues, and maintaining consistent temperature and pressure throughout the process.
8.4 How does co-extrusion affect the recycling of HIPS products?
Co-extruded products can be more challenging to recycle due to the combination of materials. However, advancements in recycling technologies are addressing these challenges.
8.5 What industries benefit most from HIPS sheet co-extrusion?
Industries such as packaging, electronics, automotive, and consumer goods are among the primary beneficiaries of HIPS sheet co-extrusion technology.
9. Conclusion
HIPS sheet co-extruder technology represents a significant advancement in plastic manufacturing, offering manufacturers the ability to produce high-quality, durable products efficiently. By understanding the co-extrusion process, its advantages, and best practices for optimization, businesses can enhance their production capabilities and meet the evolving demands of the market. With a focus on innovation and quality, HIPS co-extrusion will continue to play a vital role in shaping the future of plastic manufacturing.
Previous Page:
RELATED INFORMATION
Understanding PET Sheet Extruder Machines: A Comprehensive Guide
PET sheet extruder machines are specialized equipment used in the plastic processing industry to produce sheets made from polyethylene terephthalate (PET). These machines play a crucial role in various applications, including packaging, automotive parts, and consumer goods. Understanding how these machines work, their components, and their applications can help manufacturers improve efficiency and
Exploring the Efficiency of PET Single Screw Extruders in Manufacturing
Exploring the Efficiency of PET Single Screw Extruders in Manufacturing Table of Contents 1. Introduction to PET Single Screw Extruders 2. The Importance of PET in the Manufacturing Process 3. Design and Mechanism of Single Screw Extruders 4. Efficiency Factors of PET Single Screw Extruders 5. Applications of PET Single Screw Extruders in Manufacturing 6. Maintenance and O