Exploring the Benefits of HIPS Sheet Co-Extrusion for Your Production Line
2025-07
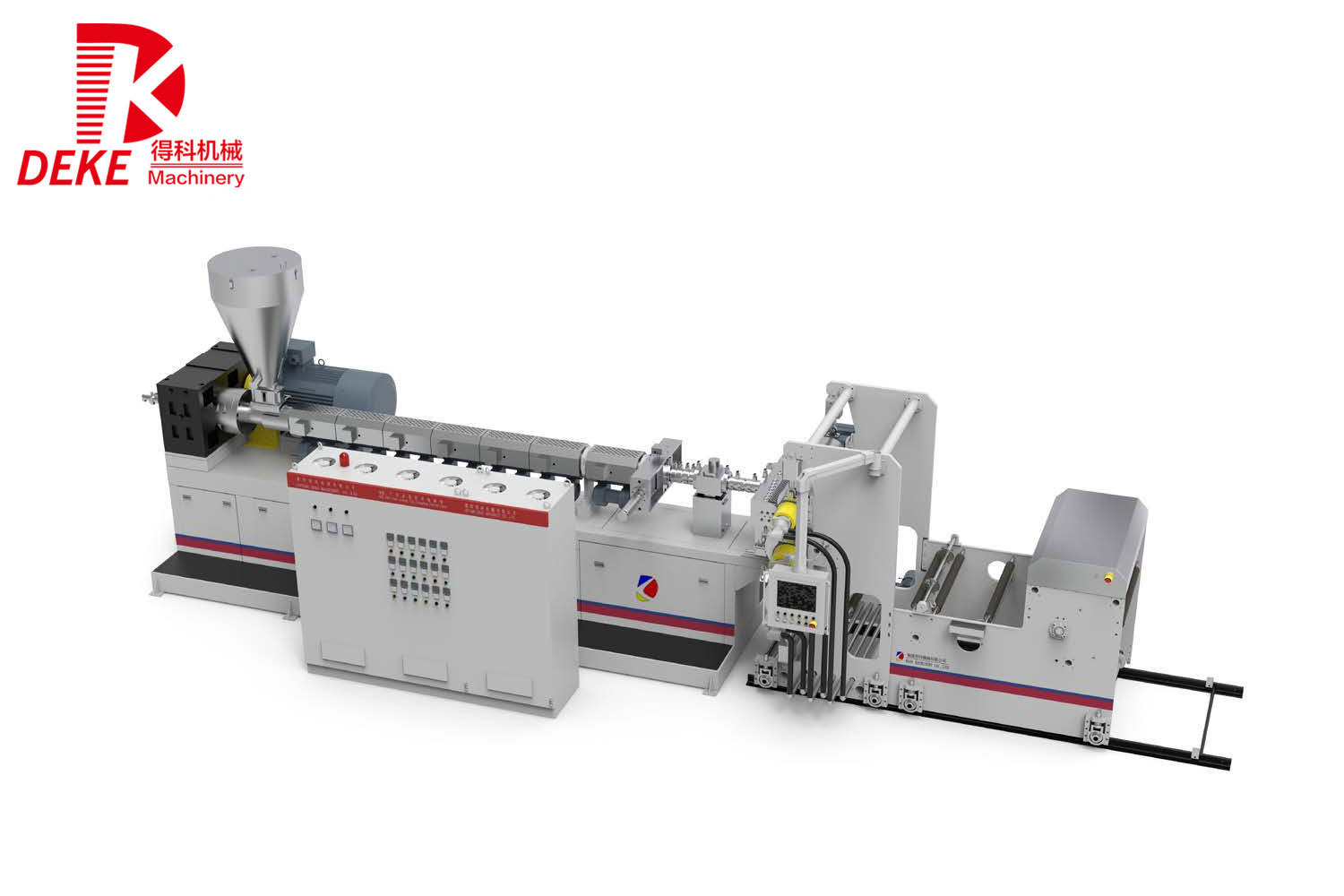
Exploring the Benefits of HIPS Sheet Co-Extrusion for Your Production Line
Table of Contents
- 1. Introduction to HIPS Sheet Co-Extrusion
- 2. What is HIPS (High Impact Polystyrene)?
- 3. The Co-Extrusion Process Explained
- 4. Advantages of HIPS Sheet Co-Extrusion
- 4.1 Enhanced Product Quality
- 4.2 Cost Efficiency
- 4.3 Increased Production Speed
- 4.4 Versatility in Applications
- 5. Applications of HIPS Sheet Co-Extrusion
- 6. Sustainability Aspects of HIPS Co-Extrusion
- 7. Case Studies: Success Stories in HIPS Co-Extrusion
- 8. Frequently Asked Questions (FAQs)
- 9. Conclusion
1. Introduction to HIPS Sheet Co-Extrusion
In today's fast-paced manufacturing environment, efficiency and innovation are key to staying competitive. HIPS sheet co-extrusion is a cutting-edge technology that allows manufacturers to produce high-quality plastic sheets with enhanced properties. By combining multiple layers of materials, this process not only improves the performance of the final product but also streamlines production processes, leading to significant cost savings.
2. What is HIPS (High Impact Polystyrene)?
High Impact Polystyrene (HIPS) is a versatile thermoplastic that is widely used in various applications due to its excellent impact resistance and ease of fabrication. HIPS combines the rigidity of polystyrene with the toughness of rubber, resulting in a material that is ideal for applications requiring durability and flexibility. Commonly used in packaging, automotive parts, and consumer goods, HIPS is a go-to choice for manufacturers looking for a reliable plastic solution.
3. The Co-Extrusion Process Explained
Co-extrusion is a method that involves the simultaneous extrusion of two or more different materials through a single die to create a multi-layered product. In the case of HIPS sheet co-extrusion, layers of HIPS can be combined with other materials to enhance specific properties. The process typically involves the following steps:
1. **Material Preparation**: Raw materials are prepared and fed into separate extruders.
2. **Melt Processing**: Each material is heated and melted before being forced through a common die.
3. **Layer Formation**: As the materials exit the die, they form distinct layers that adhere to one another, resulting in a composite sheet.
4. **Cooling and Solidifying**: The extruded sheet is cooled to solidify and then cut to the desired dimensions.
This process allows for precise control over the thickness and composition of each layer, enabling manufacturers to tailor products to meet specific needs.
4. Advantages of HIPS Sheet Co-Extrusion
HIPS sheet co-extrusion offers numerous advantages that can significantly enhance your production line.
4.1 Enhanced Product Quality
Co-extrusion provides manufacturers with the ability to create sheets that exhibit superior properties. By layering different materials, it is possible to achieve enhanced impact resistance, improved chemical resistance, and better surface finishes. This results in products that meet stringent quality standards and perform more reliably in end-use applications.
4.2 Cost Efficiency
One of the standout benefits of HIPS sheet co-extrusion is the potential for cost savings. By combining materials, manufacturers can reduce the amount of more expensive materials used while still achieving desired performance characteristics. Additionally, the efficiency of the co-extrusion process often leads to lower production costs, as less energy and labor are required compared to traditional single-material extrusion methods.
4.3 Increased Production Speed
The co-extrusion process allows for faster production rates compared to conventional extrusion methods. Multiple layers can be produced in a single pass, significantly increasing throughput. This efficiency translates to shorter lead times and the ability to meet growing market demands without compromising quality.
4.4 Versatility in Applications
HIPS sheet co-extrusion is suitable for a wide range of applications across various industries. From packaging solutions and automotive components to consumer electronics and construction materials, the versatility of co-extruded sheets makes them an attractive option for manufacturers looking to innovate and diversify their product offerings.
5. Applications of HIPS Sheet Co-Extrusion
The applications of HIPS sheet co-extrusion are vast and varied. Some notable examples include:
- **Packaging**: HIPS sheets are used in food packaging due to their excellent barrier properties and durability.
- **Signage**: The vibrant colors and ease of fabrication make co-extruded HIPS sheets ideal for outdoor signage and displays.
- **Automotive Parts**: Lightweight and impact-resistant, HIPS sheets can be utilized in automotive interiors and exterior parts.
- **Consumer Goods**: Products such as toys, kitchenware, and electronic housings often leverage the benefits of co-extruded HIPS sheets.
6. Sustainability Aspects of HIPS Co-Extrusion
As the world focuses more on sustainability, HIPS sheet co-extrusion provides eco-friendly advantages. By optimizing material usage and reducing waste, manufacturers can adopt more sustainable practices. Additionally, the ability to incorporate recycled materials into the co-extrusion process allows companies to lower their carbon footprint and contribute to a circular economy.
7. Case Studies: Success Stories in HIPS Co-Extrusion
Several companies have successfully integrated HIPS sheet co-extrusion into their manufacturing processes. For instance:
- **Company A**: By switching to HIPS sheet co-extrusion, this packaging manufacturer reduced material costs by 20% while increasing production efficiency by 30%.
- **Company B**: An automotive parts supplier utilized co-extruded HIPS sheets to develop a new line of lightweight components, resulting in a significant reduction in vehicle weight and improved fuel efficiency.
These case studies illustrate the practical benefits of adopting HIPS sheet co-extrusion technology.
8. Frequently Asked Questions (FAQs)
1. What materials can be co-extruded with HIPS?
HIPS can be co-extruded with various materials, including other plastics like polyethylene (PE) or polypropylene (PP), to enhance specific properties such as barrier performance or surface texture.
2. How does co-extrusion improve product durability?
By combining different materials with varying properties, co-extrusion produces sheets that are tougher and more resistant to impacts, chemicals, and environmental factors, leading to longer-lasting products.
3. Is co-extrusion suitable for small production runs?
While co-extrusion is often more efficient for larger production runs, advancements in technology have made it feasible for smaller batches as well. Customization options and rapid prototyping capabilities enhance its appeal.
4. Can HIPS sheet co-extrusion help with sustainability goals?
Yes, co-extrusion can aid in sustainability by minimizing waste, optimizing material use, and allowing for the incorporation of recycled materials into the production process.
5. What industries benefit the most from HIPS sheet co-extrusion?
Industries such as packaging, automotive, consumer goods, and construction benefit significantly from HIPS sheet co-extrusion due to its versatile applications and performance characteristics.
9. Conclusion
HIPS sheet co-extrusion represents a transformative advancement in the realm of plastic manufacturing. By offering enhanced product quality, cost efficiency, increased production speed, and versatility, this technology stands out as a valuable asset for any production line. As manufacturers strive to meet the demands of an evolving market, incorporating HIPS sheet co-extrusion can lead to significant competitive advantages. Embracing this innovative process not only improves product offerings but also contributes to sustainable manufacturing practices, ensuring a prosperous future for businesses in the plastic processing industry.
Previous Page:
RELATED INFORMATION
Understanding PET Sheet Extruder Machines: A Comprehensive Guide
PET sheet extruder machines are specialized equipment used in the plastic processing industry to produce sheets made from polyethylene terephthalate (PET). These machines play a crucial role in various applications, including packaging, automotive parts, and consumer goods. Understanding how these machines work, their components, and their applications can help manufacturers improve efficiency and
Exploring the Efficiency of PET Single Screw Extruders in Manufacturing
Exploring the Efficiency of PET Single Screw Extruders in Manufacturing Table of Contents 1. Introduction to PET Single Screw Extruders 2. The Importance of PET in the Manufacturing Process 3. Design and Mechanism of Single Screw Extruders 4. Efficiency Factors of PET Single Screw Extruders 5. Applications of PET Single Screw Extruders in Manufacturing 6. Maintenance and O