Understanding HDPE Sheet Extruders: Key Insights for Professionals
2025-07
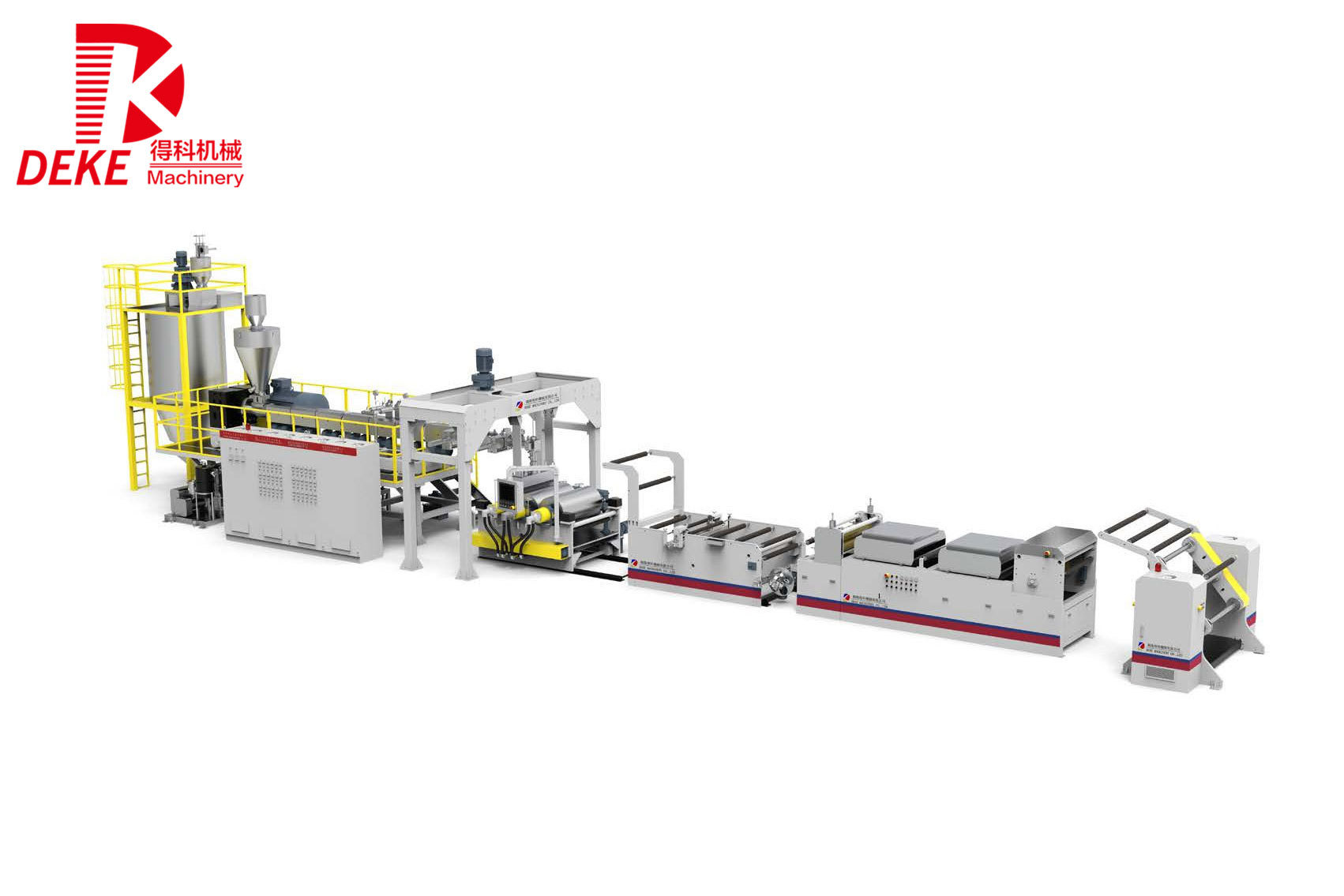
One of the primary benefits of using HDPE sheet extruders is the material itself. HDPE is known for its strength, durability, and resistance to impact, chemicals, and moisture. These qualities make HDPE sheets ideal for a range of applications, from industrial containers to construction materials and even consumer goods. The ability to produce custom thicknesses and sizes with HDPE sheet extruders allows manufacturers to meet specific customer needs effectively.
The operation of HDPE sheet extruders involves several key components, including the hopper, extruder barrel, screw, die, and cooling system. The process begins with the loading of plastic pellets into the hopper, which then feed into the extruder barrel. Here, the screw mechanism plays a crucial role in melting the pellets through friction and heat, preparing the material for shaping. Once the melted HDPE reaches the die, it is formed into sheets of desired thickness before moving into a cooling system, solidifying the extruded product.
To enhance productivity, manufacturers often consider several factors when operating HDPE sheet extruders. Maintaining optimal temperatures within the extruder barrel is crucial, as overheating can degrade the material and affect the quality of the final product. Additionally, the choice of screw design can influence the flow characteristics and melting efficiency of the HDPE. Advanced HDPE sheet extruders may also feature automated controls for monitoring temperature and pressure, leading to more consistent output and reduced waste.
Investing in high-quality HDPE sheet extruders can yield considerable advantages in production efficiency and product quality. As the demand for HDPE products continues to rise, understanding the operational nuances of these machines becomes increasingly vital. By focusing on optimizing processes and ensuring that equipment is maintained properly, manufacturers can stay competitive in a dynamic industry.
In conclusion, HDPE sheet extruders play a pivotal role in the plastic processing sector, offering versatile solutions for producing high-quality sheets. Industry professionals must stay informed about the latest technologies and best practices to harness the full potential of these machines, ensuring sustainable and profitable production outcomes.
RELATED INFORMATION
Understanding PET Sheet Extruder Machines: A Comprehensive Guide
PET sheet extruder machines are specialized equipment used in the plastic processing industry to produce sheets made from polyethylene terephthalate (PET). These machines play a crucial role in various applications, including packaging, automotive parts, and consumer goods. Understanding how these machines work, their components, and their applications can help manufacturers improve efficiency and
Exploring the Efficiency of PET Single Screw Extruders in Manufacturing
Exploring the Efficiency of PET Single Screw Extruders in Manufacturing Table of Contents 1. Introduction to PET Single Screw Extruders 2. The Importance of PET in the Manufacturing Process 3. Design and Mechanism of Single Screw Extruders 4. Efficiency Factors of PET Single Screw Extruders 5. Applications of PET Single Screw Extruders in Manufacturing 6. Maintenance and O