Understanding PLA Sheet Extrusion Lines: A Comprehensive Guide to Plastic Processing Technology
2025-06
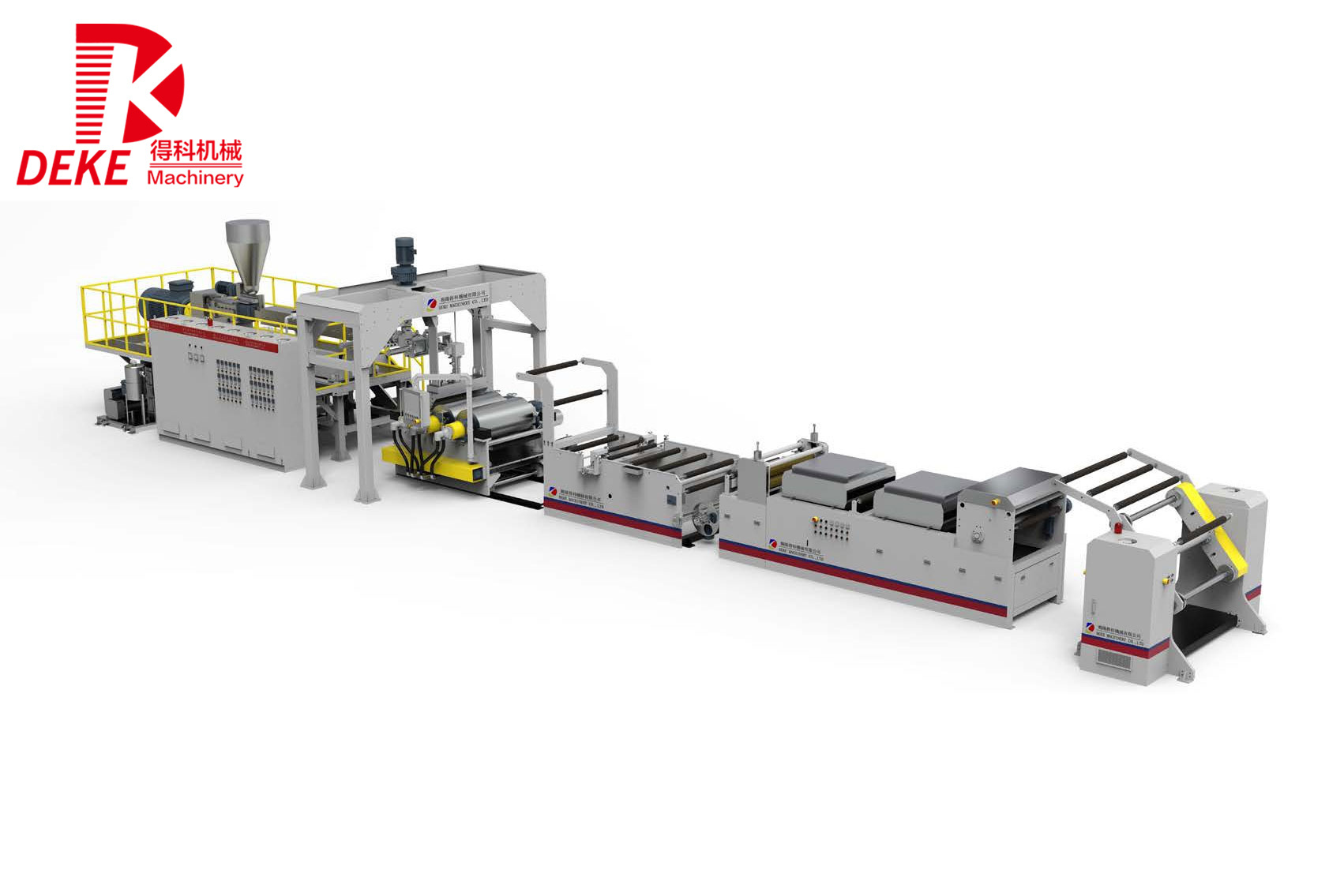
The core function of a PLA sheet extrusion line is to take PLA pellets and convert them into continuous sheets through an extrusion process. This involves several key stages: feeding, melting, extruding, and cooling. Initially, PLA pellets are fed into the extruder, where they are heated and melted. The molten PLA is then forced through a die, shaping it into a flat sheet. Subsequently, the sheet is cooled and solidified, ready for further processing or cutting.
One of the most significant advantages of using PLA for sheet production is its compostability and lower environmental impact compared to traditional petroleum-based plastics. PLA is derived from renewable resources such as corn starch or sugarcane, making it a popular choice for eco-conscious manufacturers. The resulting sheets can be used in various applications, including packaging, disposable tableware, and even in the construction of medical devices.
When considering a PLA sheet extrusion line, there are several factors to keep in mind. First, it's essential to evaluate the extruder's capacity and efficiency, as these will directly impact production volume and energy consumption. High-quality extruders designed for PLA processing can ensure consistent melt flow and sheet thickness, which are critical for product performance.
Another key consideration is the temperature control system within the extrusion line. PLA has specific thermal properties that require precise temperature management to prevent degradation. An advanced temperature control system will help maintain optimal conditions throughout the extrusion process, ensuring high-quality output.
Additionally, the choice of downstream equipment, such as cooling rolls and trimming devices, plays a crucial role in the final product's quality. It is vital to select equipment that complements the PLA sheet extrusion line to achieve smooth and uniform sheets.
In summary, PLA sheet extrusion lines are an essential component of the plastic processing industry, particularly for manufacturers focused on sustainability. By understanding the extrusion process, evaluating equipment options, and considering the unique properties of PLA, industry professionals can enhance their production capabilities while contributing to a greener future. Embracing the advancements in PLA technology not only fulfills market demands but also aligns with the growing emphasis on environmental responsibility.
RELATED INFORMATION
Understanding PET Sheet Extruder Machines: A Comprehensive Guide
PET sheet extruder machines are specialized equipment used in the plastic processing industry to produce sheets made from polyethylene terephthalate (PET). These machines play a crucial role in various applications, including packaging, automotive parts, and consumer goods. Understanding how these machines work, their components, and their applications can help manufacturers improve efficiency and
Exploring the Efficiency of PET Single Screw Extruders in Manufacturing
Exploring the Efficiency of PET Single Screw Extruders in Manufacturing Table of Contents 1. Introduction to PET Single Screw Extruders 2. The Importance of PET in the Manufacturing Process 3. Design and Mechanism of Single Screw Extruders 4. Efficiency Factors of PET Single Screw Extruders 5. Applications of PET Single Screw Extruders in Manufacturing 6. Maintenance and O