How HDPE Sheet Extruders Contribute to Waste Reduction and Sustainable Manufacturing
2025-07
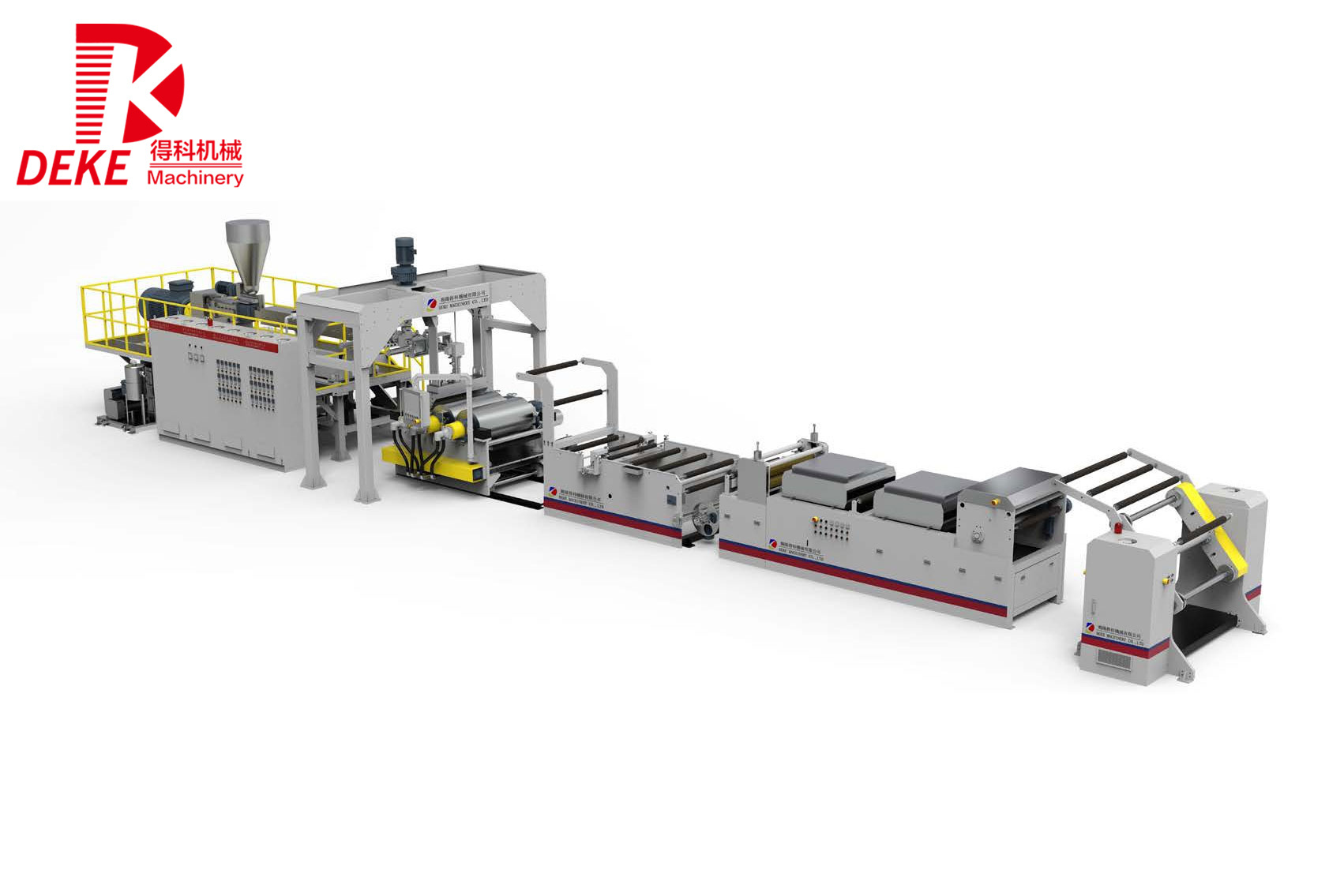
Introduction to HDPE Sheet Extruders and Their Environmental Impact
The quest for environmental sustainability is more pressing than ever, especially in the realm of manufacturing. As industries increasingly adopt eco-friendly practices, **HDPE sheet extruders** emerge as pivotal players in reducing plastic waste and promoting recycling. High-Density Polyethylene (HDPE) is a robust plastic with diverse applications; however, its production and disposal have historically raised environmental concerns. This article will comprehensively explore how HDPE sheet extruders contribute to waste reduction, offering insights into sustainable manufacturing practices.
Understanding HDPE and Its Applications
**High-Density Polyethylene**, commonly referred to as HDPE, is a versatile plastic known for its strength, durability, and resistance to various chemicals. Its applications range from packaging materials to construction and automotive components.
The Versatility of HDPE
HDPE is utilized in various industries due to its impressive characteristics:
- **Packaging**: HDPE is commonly used for bottles, containers, and bags.
- **Construction**: Its strength makes it ideal for piping, geomembranes, and other construction materials.
- **Consumer Goods**: It is found in toys, household items, and more.
Environmental Concerns Related to HDPE Production
Despite its advantageous properties, the production of HDPE raises significant environmental concerns. Traditional manufacturing processes often lead to substantial waste, contributing to the global plastic pollution crisis. The challenge lies in innovating production methods that prioritize sustainability without sacrificing efficiency or performance.
The Role of Extrusion in HDPE Processing
Extrusion is a crucial process in the production of HDPE sheets. During extrusion, plastic pellets are melted and formed into continuous sheets, allowing for precise control over thickness and consistency.
What Is HDPE Sheet Extrusion?
HDPE sheet extrusion involves several stages:
1. **Feeding**: Raw HDPE pellets are fed into an extruder.
2. **Melting**: The pellets are heated and melted into a viscous form.
3. **Shaping**: The molten plastic is then shaped into sheets through a die.
4. **Cooling**: The sheets are cooled and cut to the desired dimensions.
Benefits of HDPE Sheet Extrusion in Waste Reduction
HDPE sheet extruders help minimize waste through several mechanisms:
- **Efficient Material Use**: Extruders can produce sheets with minimal scrap material, optimizing the use of raw materials.
- **Recycling Capabilities**: Many HDPE sheet extruders are designed to incorporate recycled materials, reducing the need for virgin plastic.
- **Reduced Energy Consumption**: Advanced extrusion technologies can lower energy consumption, contributing to a smaller carbon footprint.
How HDPE Extruders Minimize Waste Generation
The innovative designs and technologies embedded in modern HDPE sheet extruders play a colossal role in waste reduction.
Closed-Loop Systems
Many manufacturers are integrating closed-loop systems within their extrusion machines. These systems recycle waste generated during the extrusion process, transforming it back into reusable feedstock. This not only reduces waste but also lowers production costs.
Continuous Improvement and Innovation
The pursuit of efficiency is a continuous journey. Manufacturers invest in research and development to improve extrusion techniques, yielding higher quality products while reducing environmental impact.
Innovative Technologies in HDPE Sheet Extrusion
Emerging technologies in HDPE sheet extrusion are redefining industry standards for waste reduction.
Advanced Control Systems
Modern extruders often come equipped with state-of-the-art control systems that monitor parameters such as temperature, pressure, and flow rate in real time. This precision ensures optimal performance, minimizing defects and waste during production.
Integration of Biodegradable Materials
Some manufacturers are exploring blends of HDPE with biodegradable materials, providing a pathway for more sustainable plastic solutions. These innovations can significantly mitigate the environmental impact of plastic waste.
Real-World Applications of HDPE Sheet Extrusion in Waste Management
Examining real-world applications sheds light on how industries leverage HDPE sheet extruders to reduce waste.
Case Study: Packaging Industry
In the packaging sector, HDPE sheet extruders play a vital role in creating lightweight and durable packaging solutions. Companies utilize recycled HDPE to produce new packaging materials, significantly reducing landfill contributions.
Case Study: Construction Materials
Construction firms are increasingly turning to HDPE sheets for applications such as underlayments and vapor barriers. By utilizing recycled HDPE sheets, they not only achieve durability but also support waste reduction initiatives.
The Future of HDPE Sheet Extruders and Waste Reduction
As we look toward the future, HDPE sheet extruders will undoubtedly continue to evolve, further contributing to sustainable manufacturing practices.
Increasing Regulations and Market Demand
With rising environmental regulations and consumer demand for sustainable products, the market for eco-friendly HDPE solutions is expanding. Companies that invest in advanced extrusion technologies will likely gain a competitive edge.
Emphasis on Circular Economy
The circular economy model will further influence the direction of HDPE sheet extrusion. Emphasizing reuse, recycling, and resource efficiency will become central to production strategies.
Frequently Asked Questions (FAQs)
1. What is the role of HDPE sheet extruders in sustainability?
HDPE sheet extruders play a critical role in sustainability by minimizing waste generation, incorporating recycled materials, and reducing energy consumption during production.
2. How does the extrusion process work for HDPE sheets?
The extrusion process involves melting HDPE pellets, shaping them into sheets through a die, and cooling them before cutting to the desired dimensions.
3. Can HDPE sheets be recycled?
Yes, HDPE sheets can be recycled and are often made from recycled materials, contributing to waste reduction efforts.
4. What industries benefit from HDPE sheet extrusion?
Industries such as packaging, construction, and consumer goods benefit significantly from HDPE sheet extrusion due to its versatility and durability.
5. How can manufacturers improve their HDPE extrusion processes?
Manufacturers can improve their processes by incorporating advanced control systems, utilizing closed-loop recycling systems, and integrating biodegradable materials.
Conclusion
HDPE sheet extruders are revolutionizing the plastic manufacturing landscape by addressing critical environmental challenges. Through efficient production techniques, recycling capabilities, and innovative technologies, these machines significantly reduce waste and promote sustainability. As industries continue to seek eco-friendly solutions, the role of HDPE sheet extruders will undoubtedly expand, paving the way for a more sustainable future in manufacturing. Emphasizing the balance between production efficiency and environmental responsibility, we can harness the full potential of HDPE to create a greener world.
RELATED INFORMATION
Understanding PET Sheet Extruder Machines: A Comprehensive Guide
PET sheet extruder machines are specialized equipment used in the plastic processing industry to produce sheets made from polyethylene terephthalate (PET). These machines play a crucial role in various applications, including packaging, automotive parts, and consumer goods. Understanding how these machines work, their components, and their applications can help manufacturers improve efficiency and
Exploring the Efficiency of PET Single Screw Extruders in Manufacturing
Exploring the Efficiency of PET Single Screw Extruders in Manufacturing Table of Contents 1. Introduction to PET Single Screw Extruders 2. The Importance of PET in the Manufacturing Process 3. Design and Mechanism of Single Screw Extruders 4. Efficiency Factors of PET Single Screw Extruders 5. Applications of PET Single Screw Extruders in Manufacturing 6. Maintenance and O