Essential Components of a High-Performance PLA Sheet Extrusion Line
2025-06
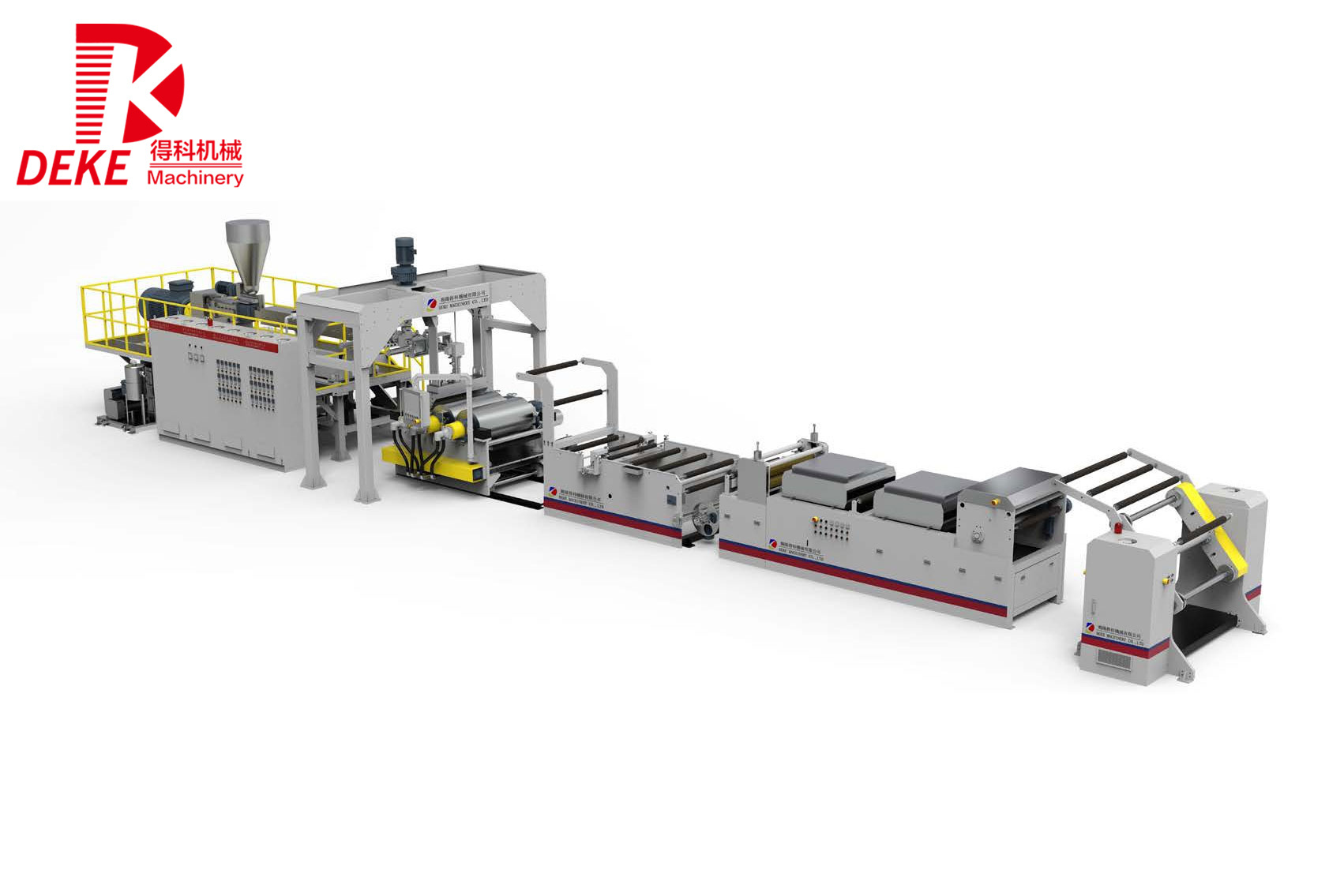
Essential Components of a High-Performance PLA Sheet Extrusion Line
When it comes to the production of biodegradable plastics, particularly Polylactic Acid (PLA), the efficiency and performance of the extrusion line play a critical role in achieving high-quality output. Understanding the essential components of a high-performance PLA sheet extrusion line enables manufacturers to optimize their processes, enhance product quality, and reduce waste. This guide will delve deep into the pivotal elements that contribute to an efficient PLA sheet extrusion system.
Table of Contents
- Introduction to PLA Sheet Extrusion
- Key Components of a PLA Sheet Extrusion Line
- Process Steps in PLA Sheet Extrusion
- Optimizing Performance in PLA Extrusion
- Quality Control Measures
- Future Trends in PLA Sheet Extrusion Technology
- Conclusion
- Frequently Asked Questions
Introduction to PLA Sheet Extrusion
In recent years, the demand for sustainable materials has led to the growing popularity of PLA, a biodegradable thermoplastic derived from renewable resources like corn starch or sugarcane. The extrusion process for PLA involves melting the polymer and forming it into sheets, which can then be utilized in numerous applications, including packaging, consumer goods, and medical devices. Understanding the essential components of a high-performance PLA sheet extrusion line is crucial for manufacturers aiming to produce high-quality sheets efficiently.
Key Components of a PLA Sheet Extrusion Line
A high-performance PLA sheet extrusion line comprises several critical components that work in unison to ensure optimal performance and quality. Each component plays a vital role in the extrusion process, and an understanding of these elements is key to maximizing efficiency and output.
The Extruder
The **extruder** serves as the heart of the PLA sheet extrusion line. It is responsible for melting the PLA resin and converting it into a flowable mass. The extruder typically consists of a hopper, barrel, screws, and a heating mechanism. Here’s a closer look at its main features:
- **Hopper**: The initial entry point for PLA pellets, where they are fed into the extruder.
- **Screws**: These convey the pellets through the barrel, ensuring even melting and mixing. The design and configuration of the screws are tailored to optimize shear and temperature, facilitating a homogeneous melt.
- **Heating Zones**: The barrel contains several heating zones that progressively melt the PLA. Precise temperature control is essential to prevent degradation of the polymer.
Proper selection of the extruder based on the desired output, material characteristics, and processing parameters is critical. Manufacturers often opt for twin-screw extruders for improved mixing and processing of PLA.
The Die
The **die** is a crucial component that shapes the melted PLA into sheets. The design of the die directly influences the thickness and width of the sheets produced. Key considerations include:
- **Die Design**: A flat die is commonly used for sheet production, allowing for uniform thickness. The die should be engineered to maintain consistent flow and pressure to ensure high-quality output.
- **Temperature Control**: Maintaining optimal die temperatures is vital to minimize shear stress and prevent degradation of the PLA, ensuring a smooth flow of the molten polymer.
Investing in high-quality dies can significantly impact the efficiency and quality of the extrusion process.
Calibration Unit
The **calibration unit** is essential for achieving precise sheet dimensions. After exiting the die, the molten PLA sheet must be cooled and set to the desired thickness. The calibration unit controls the sheet's width and thickness through various mechanisms such as:
- **Calibration Plates**: These plates help shape and hold the molten sheet in place while it cools.
- **Vacuum Calibration**: This method employs a vacuum to stabilize the sheet as it cools, ensuring uniform thickness and preventing warping.
Effective calibration contributes to the overall quality of the final product, making it a vital component of the extrusion line.
Cooling Systems
Cooling systems play a crucial role in the PLA sheet extrusion process. Once the sheet exits the calibration unit, it needs to be cooled rapidly to solidify the polymer. Various cooling methods can be employed:
- **Water Baths**: Immersing the sheets in a water bath provides efficient cooling and helps maintain consistent thickness.
- **Air Cooling**: For some applications, air cooling systems using fans can provide sufficient cooling without the need for water.
The choice of cooling method affects both production speed and sheet quality.
Winding Equipment
After cooling, the PLA sheets are wound onto rolls for storage and transportation. The **winding equipment** must ensure that the sheets are wound tightly and uniformly to prevent defects. Important features include:
- **Tension Control**: Proper tension during winding is necessary to avoid wrinkles or damage to the sheets.
- **Roll Diameter Adjustment**: The equipment should allow for easy adjustment of roll sizes to accommodate varying production outputs.
Advanced winding solutions can automate this process, further enhancing efficiency.
Process Steps in PLA Sheet Extrusion
Understanding the process flow of PLA sheet extrusion can help manufacturers identify areas for improvement. The typical steps involved include:
1. **Material Preparation**: Raw PLA pellets are dried and prepared for extrusion. Moisture content must be minimized to avoid defects in the final product.
2. **Feeding**: The dried pellets are fed into the extruder through the hopper.
3. **Melting and Mixing**: As the screw rotates, heat and shear forces melt the PLA, ensuring homogeneity.
4. **Extrusion**: The molten PLA is forced through the die, forming a continuous sheet.
5. **Calibration and Cooling**: The sheet undergoes calibration to achieve the desired thickness and is then cooled rapidly.
6. **Winding**: The finished sheets are wound onto rolls for further processing or shipping.
Each step requires careful monitoring and control to achieve optimal performance and product quality.
Optimizing Performance in PLA Extrusion
To maximize the performance of a PLA sheet extrusion line, several strategies can be implemented:
- **Regular Maintenance**: Routine maintenance of machinery ensures that all components operate efficiently, reducing downtime.
- **Temperature Control**: Precise temperature management throughout the extrusion process minimizes degradation and enhances the quality of the sheets produced.
- **Material Quality**: Sourcing high-quality PLA pellets is essential. Impurities or low-grade materials can lead to production issues and compromised end products.
By focusing on these areas, manufacturers can enhance the overall efficiency and effectiveness of their PLA sheet extrusion lines.
Quality Control Measures
Quality control is a fundamental aspect of PLA sheet extrusion. Implementing robust quality assurance protocols ensures that the final products meet industry standards and customer expectations. Key measures include:
- **Testing for Thickness and Width**: Regular sampling and measurement of the output sheets help in maintaining consistent dimensions.
- **Visual Inspection**: Observing the sheets for defects such as bubbles, wrinkles, or discoloration is essential for quality assurance.
- **Mechanical Testing**: Conducting mechanical tests on the sheets, such as tensile strength and flexibility, assesses their performance characteristics.
Establishing a comprehensive quality control framework not only guarantees product quality but also enhances customer satisfaction.
Future Trends in PLA Sheet Extrusion Technology
As the demand for sustainable materials continues to rise, innovations in PLA sheet extrusion technology are emerging. Some of the trends to watch for include:
- **Enhanced Recycling Technologies**: Advances in recycling technologies for PLA could significantly reduce waste and promote a circular economy.
- **Biocompatible Additives**: The incorporation of biocompatible additives could improve the performance of PLA sheets for specialized applications, particularly in the medical field.
- **Automated Systems**: The integration of automation in the extrusion process may enhance efficiency and reduce labor costs, allowing for higher output with minimal human intervention.
Staying ahead of these trends can help manufacturers remain competitive in the evolving landscape of biodegradable plastics.
Conclusion
An efficient and high-performance PLA sheet extrusion line is built upon several critical components, each playing an integral role in the production process. From the extruder to the winding equipment, understanding and optimizing each element can lead to enhanced output quality and efficiency. As the industry evolves, staying informed about technological advancements and best practices will be key for manufacturers looking to excel in the production of sustainable materials.
Frequently Asked Questions
1. What is PLA, and why is it important in extrusion?
PLA, or Polylactic Acid, is a biodegradable thermoplastic derived from renewable resources. It is important in extrusion due to its eco-friendly properties and versatility in various applications.
2. How does the extruder affect the quality of PLA sheets?
The extruder's design and configuration impact the melting and mixing of PLA, which directly influences the homogeneity and quality of the final sheets.
3. What should be considered when selecting a die for PLA sheet extrusion?
Considerations include die design, material compatibility, temperature control, and the desired sheet dimensions to ensure optimal output quality.
4. How can manufacturers ensure proper cooling of PLA sheets?
Choosing the right cooling method, whether water baths or air cooling, and maintaining consistent cooling rates can significantly affect the quality of the final product.
5. What are some common defects in PLA sheets, and how can they be prevented?
Common defects include bubbles, wrinkles, and uneven thickness. To prevent these issues, manufacturers should focus on temperature control, material quality, and regular quality inspections.
Previous Page:
RELATED INFORMATION
Understanding PET Sheet Extruder Machines: A Comprehensive Guide
PET sheet extruder machines are specialized equipment used in the plastic processing industry to produce sheets made from polyethylene terephthalate (PET). These machines play a crucial role in various applications, including packaging, automotive parts, and consumer goods. Understanding how these machines work, their components, and their applications can help manufacturers improve efficiency and
Exploring the Efficiency of PET Single Screw Extruders in Manufacturing
Exploring the Efficiency of PET Single Screw Extruders in Manufacturing Table of Contents 1. Introduction to PET Single Screw Extruders 2. The Importance of PET in the Manufacturing Process 3. Design and Mechanism of Single Screw Extruders 4. Efficiency Factors of PET Single Screw Extruders 5. Applications of PET Single Screw Extruders in Manufacturing 6. Maintenance and O