The Benefits of Using Advanced Control Systems in Small Twin Screw Extruders
2025-06
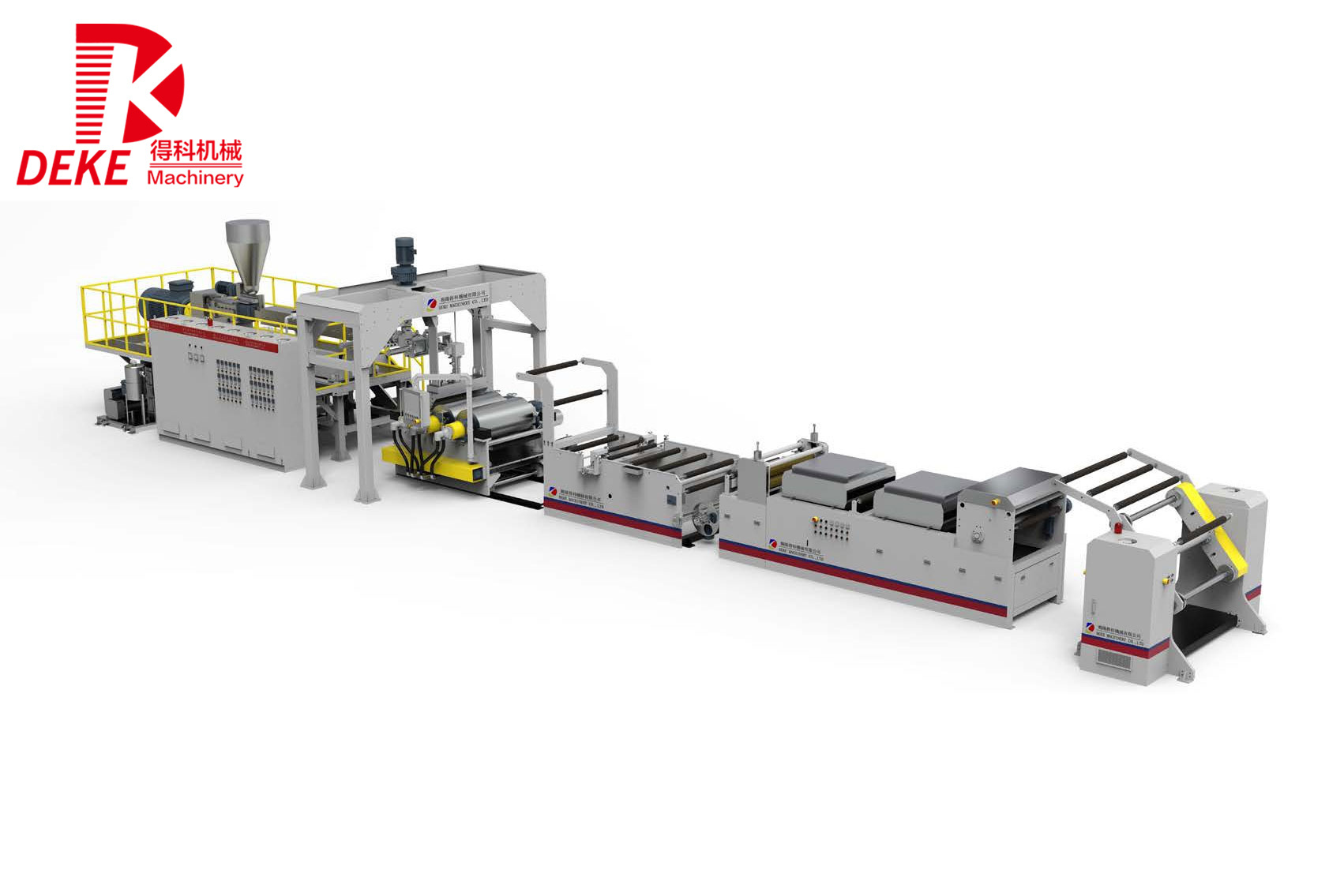
The Benefits of Using Advanced Control Systems in Small Twin Screw Extruders
Introduction to Small Twin Screw Extruders
Small twin screw extruders play a pivotal role in the plastic manufacturing industry. They are essential for various applications such as compounding, mixing, and polymer processing. The effectiveness of these machines influences the quality of the final product and overall production efficiency. As technological advancements continue to evolve, integrating **advanced control systems** into small twin screw extruders has become imperative for achieving superior performance.
Understanding Advanced Control Systems
Advanced control systems in extruders refer to sophisticated technologies that monitor, manage, and optimize the various parameters of the extrusion process. These systems can include features such as real-time data analytics, automated feedback loops, and adaptive control strategies.
What Defines an Advanced Control System?
An advanced control system is characterized by its ability to:
- **Provide real-time monitoring** of critical parameters such as temperature, pressure, and feed rate.
- **Utilize data analytics** to predict and respond to variations in the extrusion process.
- **Enable automated adjustments** to maintain optimal processing conditions, reducing the need for manual intervention.
Key Components of Control Systems
1. **Sensors and Actuators**: Vital for collecting data and executing control commands.
2. **Control Algorithms**: These mathematical formulas optimize extrusion conditions based on real-time data.
3. **User Interface**: A dashboard that presents data in an accessible manner for operators.
The Benefits of Implementing Advanced Control Systems
Integrating advanced control systems into small twin screw extruders offers multiple advantages that can significantly improve manufacturing outcomes.
1. Enhanced Process Control
With advanced control systems, manufacturers can achieve superior process control. By continuously monitoring critical parameters, these systems ensure that conditions remain within optimal ranges, which is crucial for consistent product quality. Enhanced control also mitigates the risk of defects caused by fluctuations in processing conditions.
2. Increased Productivity and Efficiency
Advanced control systems streamline the manufacturing process, reducing downtime and maximizing throughput. By automating adjustments based on real-time data, these systems allow for faster changeovers and less manual oversight, resulting in increased overall efficiency.
3. Improved Product Quality
By maintaining precise control over the extrusion process, advanced control systems help ensure that materials are processed uniformly. As a result, manufacturers can produce higher-quality products with fewer inconsistencies, enhancing customer satisfaction and loyalty.
4. Cost Savings
While the initial investment in advanced control systems may be significant, the long-term savings are substantial. Improved efficiency leads to reduced energy consumption, minimized waste, and lower labor costs. Additionally, by enhancing product quality and consistency, manufacturers can reduce the costs associated with rework and returns.
5. Enhanced Flexibility in Production
Modern control systems allow for greater flexibility in production runs. Manufacturers can easily adjust parameters to accommodate different materials or product specifications without significant downtime. This adaptability is vital in a market that increasingly demands customized solutions.
The Role of Data Analytics in Control Systems
Data analytics is a cornerstone of advanced control systems in small twin screw extruders. By harnessing the power of data, manufacturers can gain actionable insights into their processes.
1. Predictive Maintenance
Through data analysis, manufacturers can identify potential equipment failures before they occur. This predictive maintenance capability minimizes downtime and prolongs the life of the extruder.
2. Process Optimization
Data analytics enables manufacturers to analyze trends and patterns in their production processes. By understanding these dynamics, they can implement strategies to optimize flow rates, temperature settings, and other critical parameters, further enhancing efficiency.
Case Studies: Real-World Applications
Examining case studies of companies that have successfully integrated advanced control systems into their small twin screw extruders can provide compelling insights.
1. Case Study: Plastics Manufacturer A
Company A implemented an advanced control system that improved process monitoring and product quality. Within six months, they reported a 30% reduction in scrap rates and a 20% increase in production efficiency.
2. Case Study: Compounding Specialist B
Company B utilized predictive analytics to enhance their maintenance protocols. As a result, they achieved a 50% decrease in unexpected machine downtime, translating to significant cost savings and improved output.
Challenges and Considerations
Despite the numerous benefits, integrating advanced control systems comes with challenges that must be addressed.
1. Initial Investment Costs
The upfront cost of implementing advanced control systems can be substantial. Companies must weigh these costs against the long-term benefits to make informed decisions.
2. Training and Skill Development
To fully leverage the capabilities of advanced control systems, operators and technicians require appropriate training. Investing in personnel development is crucial for maximizing the return on investment.
3. Technology Integration
Integrating new control systems with existing machinery and software can pose technical challenges. Companies must engage with experienced vendors to ensure seamless integration.
Future Trends in Control Systems for Twin Screw Extruders
As the industry evolves, so too will the technology behind advanced control systems.
1. AI and Machine Learning Integration
The incorporation of AI and machine learning into control systems will facilitate even greater automation, predictive capabilities, and optimization techniques.
2. Enhanced User Interfaces
Future control systems are likely to feature more sophisticated user interfaces, making data analysis and process management even more intuitive.
3. IoT Connectivity
The Internet of Things (IoT) will play a significant role in the evolution of advanced control systems. Enhanced connectivity will allow for more comprehensive data collection and remote monitoring capabilities.
Frequently Asked Questions (FAQs)
1. What are small twin screw extruders used for?
Small twin screw extruders are primarily used for compounding, mixing, and processing polymers in various applications, including plastics manufacturing.
2. How do advanced control systems improve product quality?
By maintaining optimal processing conditions and reducing variations, advanced control systems ensure uniform material processing, resulting in higher-quality products.
3. What are the main components of an advanced control system?
Key components include sensors, actuators, control algorithms, and user interfaces that work together to monitor and manage the extrusion process.
4. Are advanced control systems cost-effective?
While there is an initial investment, the long-term savings from increased efficiency, reduced waste, and improved product quality often outweigh the costs.
5. How can companies ensure successful integration of control systems?
Engaging experienced vendors, investing in training, and conducting thorough assessments of existing machinery can facilitate smooth integration of advanced control systems.
Conclusion
Integrating advanced control systems in small twin screw extruders offers undeniable benefits that can enhance productivity, improve product quality, and streamline operations. As the industry progresses, leveraging these advanced technologies will be crucial for manufacturers seeking to maintain a competitive edge. By focusing on the implementation of sophisticated control systems, companies can unlock significant opportunities for growth and efficiency in the ever-evolving plastic processing landscape.
RELATED INFORMATION
Understanding PET Sheet Extruder Machines: A Comprehensive Guide
PET sheet extruder machines are specialized equipment used in the plastic processing industry to produce sheets made from polyethylene terephthalate (PET). These machines play a crucial role in various applications, including packaging, automotive parts, and consumer goods. Understanding how these machines work, their components, and their applications can help manufacturers improve efficiency and
Exploring the Efficiency of PET Single Screw Extruders in Manufacturing
Exploring the Efficiency of PET Single Screw Extruders in Manufacturing Table of Contents 1. Introduction to PET Single Screw Extruders 2. The Importance of PET in the Manufacturing Process 3. Design and Mechanism of Single Screw Extruders 4. Efficiency Factors of PET Single Screw Extruders 5. Applications of PET Single Screw Extruders in Manufacturing 6. Maintenance and O