Understanding the Cost and ROI of Micro Twin Screw Extrusion Systems
2025-04
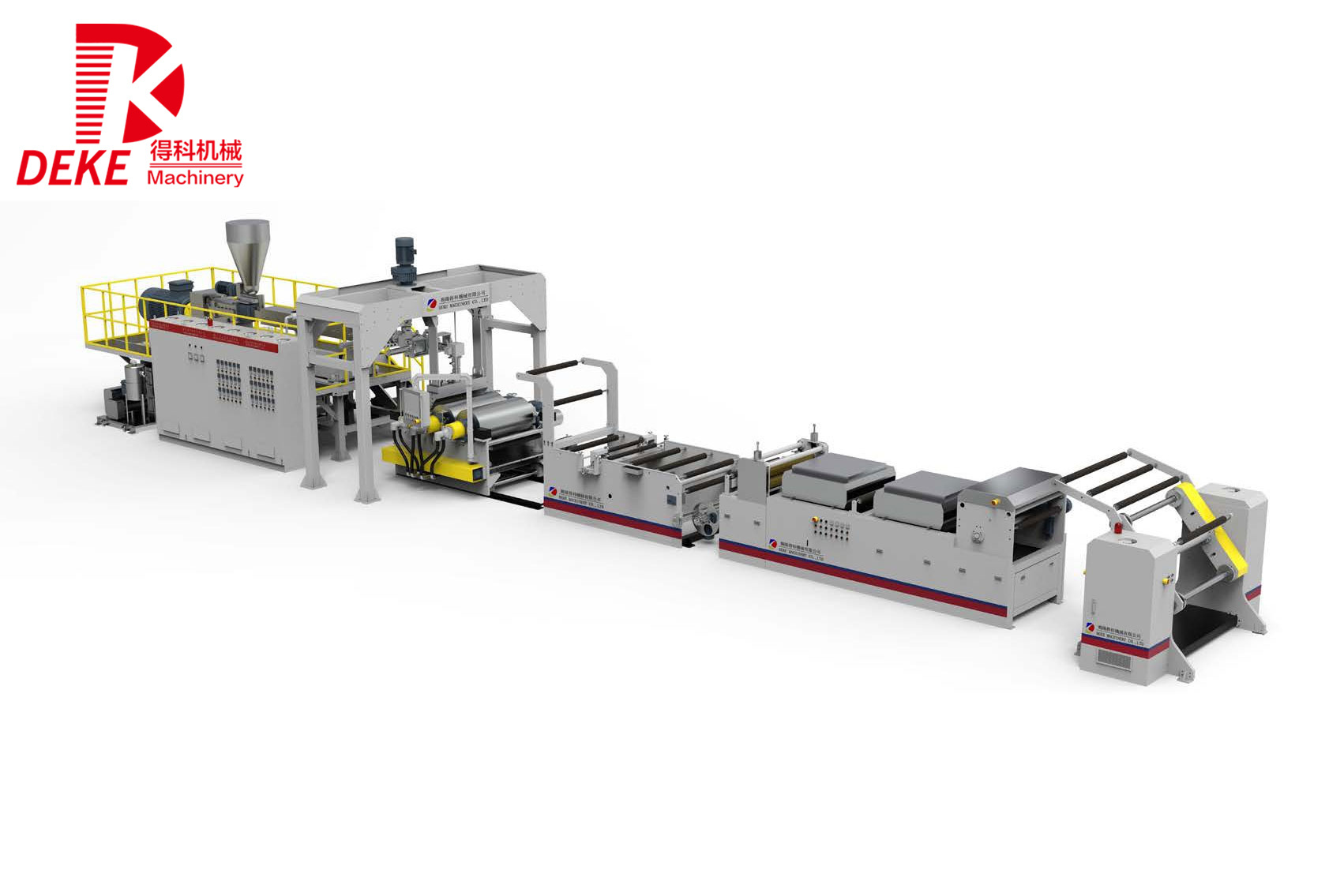
Understanding the Cost and ROI of Micro Twin Screw Extrusion Systems
Table of Contents
- 1. Introduction to Micro Twin Screw Extrusion Systems
- 2. Components and Working Principle
- 3. Cost Analysis of Micro Twin Screw Extrusion Systems
- 4. Factors Influencing Costs
- 5. Return on Investment in Extrusion Technology
- 6. Calculating the ROI of Micro Twin Screw Extruders
- 7. Applications and Industry Impacts
- 8. Future Trends in Extrusion Technology
- 9. Frequently Asked Questions
- 10. Conclusion
1. Introduction to Micro Twin Screw Extrusion Systems
Micro twin screw extrusion systems play a pivotal role in the manufacturing of plastic products, offering unparalleled versatility and efficiency. These systems utilize two intermeshing screws to convey, mix, and melt materials, making them ideal for applications ranging from food production to advanced material science. Understanding the costs and potential ROI of these systems is crucial for manufacturers looking to enhance productivity and innovation.
2. Components and Working Principle
Micro twin screw extruders consist of several key components that contribute to their functionality:
2.1 Screws
The heart of the extruder, the screws are designed to optimize material flow and mixing. Their geometry can be tailored to the specific requirements of the material being processed.
2.2 Barrel
The barrel houses the screws and provides a controlled environment where the material is heated and mixed.
2.3 Drive System
This component provides the necessary torque to turn the screws, enabling the processing of various materials.
2.4 Feeding System
The feeding system ensures a consistent and precise input of raw materials into the extruder.
3. Cost Analysis of Micro Twin Screw Extrusion Systems
Investing in micro twin screw extrusion systems involves a multifaceted cost analysis. The initial purchase price can vary significantly based on the machine's specifications, brand, and technology used. Generally, the costs can be broken down into several categories:
3.1 Initial Investment
The initial investment for a micro twin screw extruder can range from tens of thousands to several hundred thousand dollars. Factors influencing this cost include screw design, material compatibility, and any additional features such as automation and control systems.
3.2 Operational Costs
Operational costs involve energy consumption, maintenance, and labor. These costs can fluctuate based on the efficiency of the system and the complexity of the materials being processed.
3.3 Maintenance and Downtime
Regular maintenance is essential for keeping the extruder operating at peak efficiency. Unexpected downtime can lead to significant losses, making it crucial to factor in maintenance costs when considering the overall investment.
4. Factors Influencing Costs
Several factors can influence the overall cost of micro twin screw extrusion systems:
4.1 Material Type
The type of materials being processed can have a direct impact on costs. Biodegradable or advanced composite materials may require specialized equipment, increasing the initial investment.
4.2 Production Volume
Higher production volumes may justify the investment in more sophisticated equipment, enabling economies of scale that can reduce per-unit costs.
4.3 Technology and Automation
Investing in advanced technology and automation can enhance productivity but may also increase upfront costs. Manufacturers must weigh the benefits against the investment required.
4.4 Market Demand
The demand for specific products can drive costs up or down. Understanding market trends and consumer preferences is essential for making informed decisions.
5. Return on Investment in Extrusion Technology
Evaluating the ROI of micro twin screw extrusion systems requires a comprehensive understanding of how these systems can impact productivity, quality, and profitability.
5.1 Increased Efficiency
Micro twin screw extruders can significantly boost production efficiency, allowing for faster processing times and reduced waste.
5.2 Enhanced Product Quality
These systems offer precise control over the extrusion process, resulting in higher-quality products with fewer defects.
5.3 Versatility in Applications
The adaptability of micro twin screw extruders enables manufacturers to diversify their product offerings, tapping into new markets and increasing revenue potential.
6. Calculating the ROI of Micro Twin Screw Extruders
To calculate the ROI of micro twin screw extrusion systems, manufacturers can use the following formula:
ROI = (Net Profit from Investment - Cost of Investment) / Cost of Investment x 100
6.1 Estimating Net Profit
Estimating net profit involves calculating the additional revenue generated from increased production and efficiency. Consider factors such as reduced labor costs and decreased material waste.
6.2 Assessing Costs
Include all costs associated with the investment, including initial purchase, operational, and maintenance costs.
7. Applications and Industry Impacts
Micro twin screw extrusion systems are utilized across various industries, each with its unique applications:
7.1 Food Processing
These systems can be employed to create high-quality food products, ensuring consistent texture and flavor.
7.2 Plastics Manufacturing
In plastics manufacturing, micro twin screw extruders facilitate the blending and compounding of different polymer materials, enhancing product performance.
7.3 Pharmaceuticals
The pharmaceutical industry utilizes these systems for the controlled release of active ingredients, ensuring precise dosing.
8. Future Trends in Extrusion Technology
As technology continues to advance, several trends are emerging in the field of micro twin screw extrusion:
8.1 Smart Extrusion Systems
The integration of IoT and AI technologies is leading to the development of smart extrusion systems that optimize performance in real-time.
8.2 Sustainable Materials
With a growing emphasis on sustainability, manufacturers are increasingly exploring biodegradable and recycled materials for extrusion applications.
8.3 Customization and Modularity
The demand for customized solutions is driving the development of modular extrusion systems that can be easily adapted to different production needs.
9. Frequently Asked Questions
9.1 What is the lifespan of a micro twin screw extruder?
The lifespan of a micro twin screw extruder can range from 10 to 20 years, depending on usage and maintenance practices.
9.2 How much energy does a micro twin screw extruder consume?
Energy consumption varies based on the machine's size and operational conditions, typically ranging from 5 to 30 kWh per hour.
9.3 Can micro twin screw extruders process all types of materials?
While versatile, micro twin screw extruders are optimized for specific materials; manufacturers should consult with suppliers for compatibility.
9.4 What are the maintenance requirements for these systems?
Regular maintenance includes cleaning, lubrication, and inspection of components to ensure optimal performance.
9.5 How do I choose the right micro twin screw extruder for my business?
Consider factors like production volume, material types, and desired product specifications when selecting an extruder.
10. Conclusion
Investing in micro twin screw extrusion systems can significantly enhance operational efficiency, product quality, and overall profitability. By understanding the costs involved and calculating the potential ROI, manufacturers can make informed decisions that align with their business goals. The adaptability and technological advancements in extrusion systems present opportunities for growth and innovation in an ever-evolving marketplace. As industries continue to seek more efficient and sustainable production methods, micro twin screw extruders will remain at the forefront, driving the future of manufacturing.
Previous Page:
RELATED INFORMATION
Understanding the Benefits and Applications of Parallel Twin Screw Extruders
In the realm of plastic processing machinery, the parallel twin screw extruder stands out as a versatile and effective solution for a variety of applications. This type of extruder is characterized by two screws that run parallel to each other, allowing for efficient melting, mixing, and compounding of materials. The design of the parallel twin screw extruder enables a uniform and consistent outpu
Innovative Applications of Parallel Twin Screw Extruder Technology in Modern Manufacturing
Innovative Applications of Parallel Twin Screw Extruder Technology Introduction to Parallel Twin Screw Extruders The **parallel twin screw extruder** has emerged as a pivotal technology in the realm of manufacturing, particularly within the plastic processing sector. Characterized by two intermeshing screws rotating in the same direction, these extruders are designed to efficiently mix, melt, and