Understanding the Role of Twin Screw Extruders in Compounding Processes
2025-04
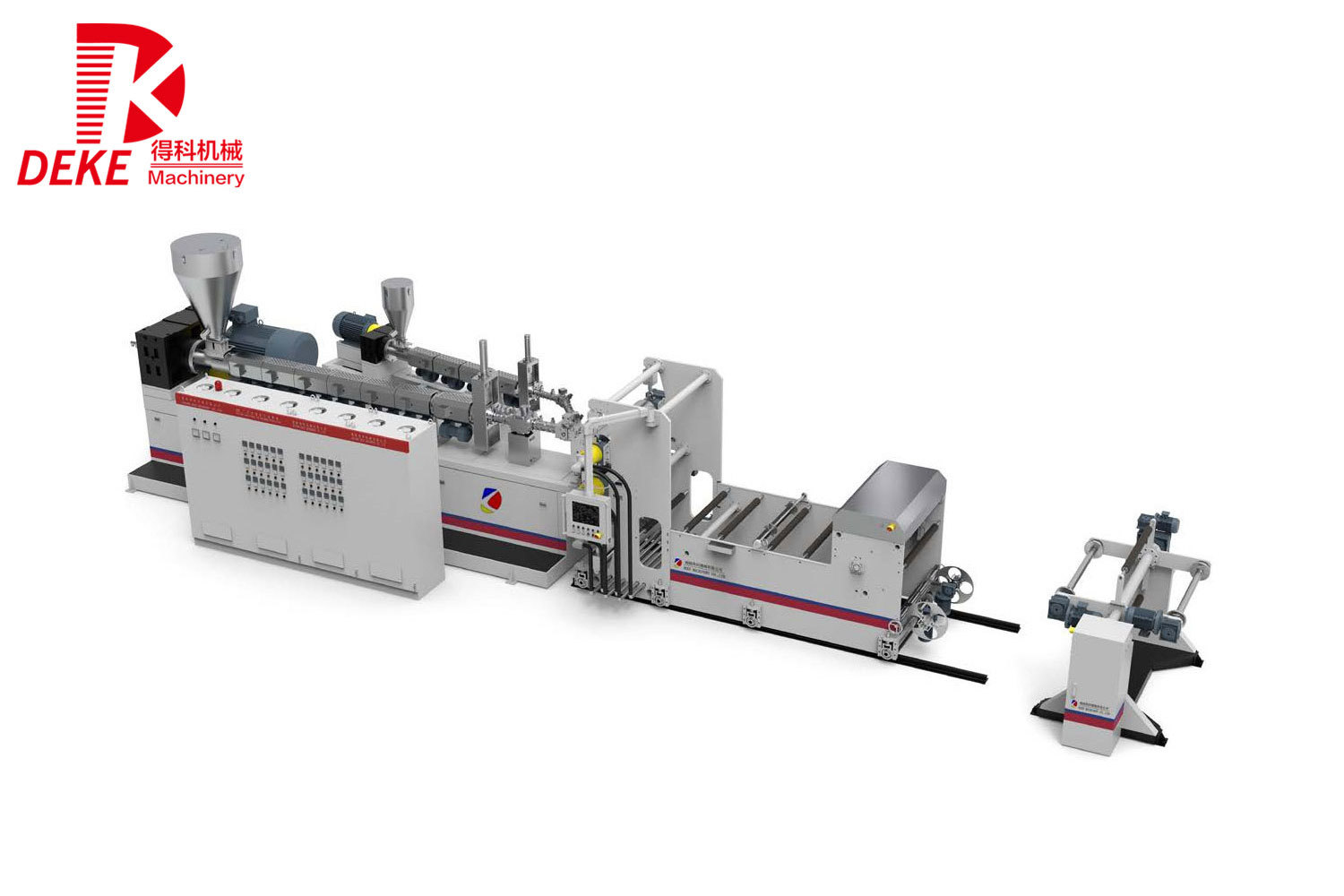
At the core of twin screw extruders is their dual screw configuration, which allows for a high degree of mixing and compounding efficiency. Unlike single screw extruders, twin screw extruders possess two intermeshing screws that facilitate a continuous and homogeneous mixture of materials. This design enables optimal shear and pressure, which are crucial for achieving desired properties in the final product. The intermeshing screws allow for better melting and compounding of polymers, leading to enhanced material properties.
One of the primary advantages of twin screw extruders is their versatility. They can process a wide range of materials, including thermoplastics, thermosets, and elastomers, making them suitable for various applications across different industries. Additionally, twin screw extruders are highly efficient in incorporating additives such as colorants, stabilizers, and fillers into the polymer base. This capability is crucial for manufacturers looking to produce specialty compounds that meet specific performance criteria.
Another significant benefit of twin screw extruders is their ability to operate under controlled temperature and pressure conditions. This feature is vital for maintaining the integrity of sensitive materials that may degrade under excessive heat or pressure. By using temperature control systems and advanced monitoring technologies, operators can ensure that the compounding process remains stable and consistent, resulting in high-quality end products.
The modular design of twin screw extruders also enhances their flexibility. Manufacturers can configure the extruder with various screw elements, such as mixing zones, pumping zones, and venting sections, tailored to specific compounding requirements. This customization allows for the optimization of material flow and processing performance, addressing the diverse needs of different applications.
In summary, twin screw extruders play a critical role in the compounding process, offering advantages such as enhanced mixing capabilities, versatility across different materials, controlled processing conditions, and customizable configurations. As the demand for high-performance plastic compounds continues to rise, the importance of twin screw extruders within the manufacturing sector will only increase, solidifying their position as a key component in modern plastic processing machinery. Understanding these machines’ operational principles and advantages can help manufacturers make informed decisions in their production processes, ultimately leading to improved product quality and operational efficiency.
RELATED INFORMATION
Understanding the Benefits and Applications of Parallel Twin Screw Extruders
In the realm of plastic processing machinery, the parallel twin screw extruder stands out as a versatile and effective solution for a variety of applications. This type of extruder is characterized by two screws that run parallel to each other, allowing for efficient melting, mixing, and compounding of materials. The design of the parallel twin screw extruder enables a uniform and consistent outpu
Innovative Applications of Parallel Twin Screw Extruder Technology in Modern Manufacturing
Innovative Applications of Parallel Twin Screw Extruder Technology Introduction to Parallel Twin Screw Extruders The **parallel twin screw extruder** has emerged as a pivotal technology in the realm of manufacturing, particularly within the plastic processing sector. Characterized by two intermeshing screws rotating in the same direction, these extruders are designed to efficiently mix, melt, and