Innovative Applications of Parallel Twin Screw Extruder Technology in Modern Manufacturing
2025-05
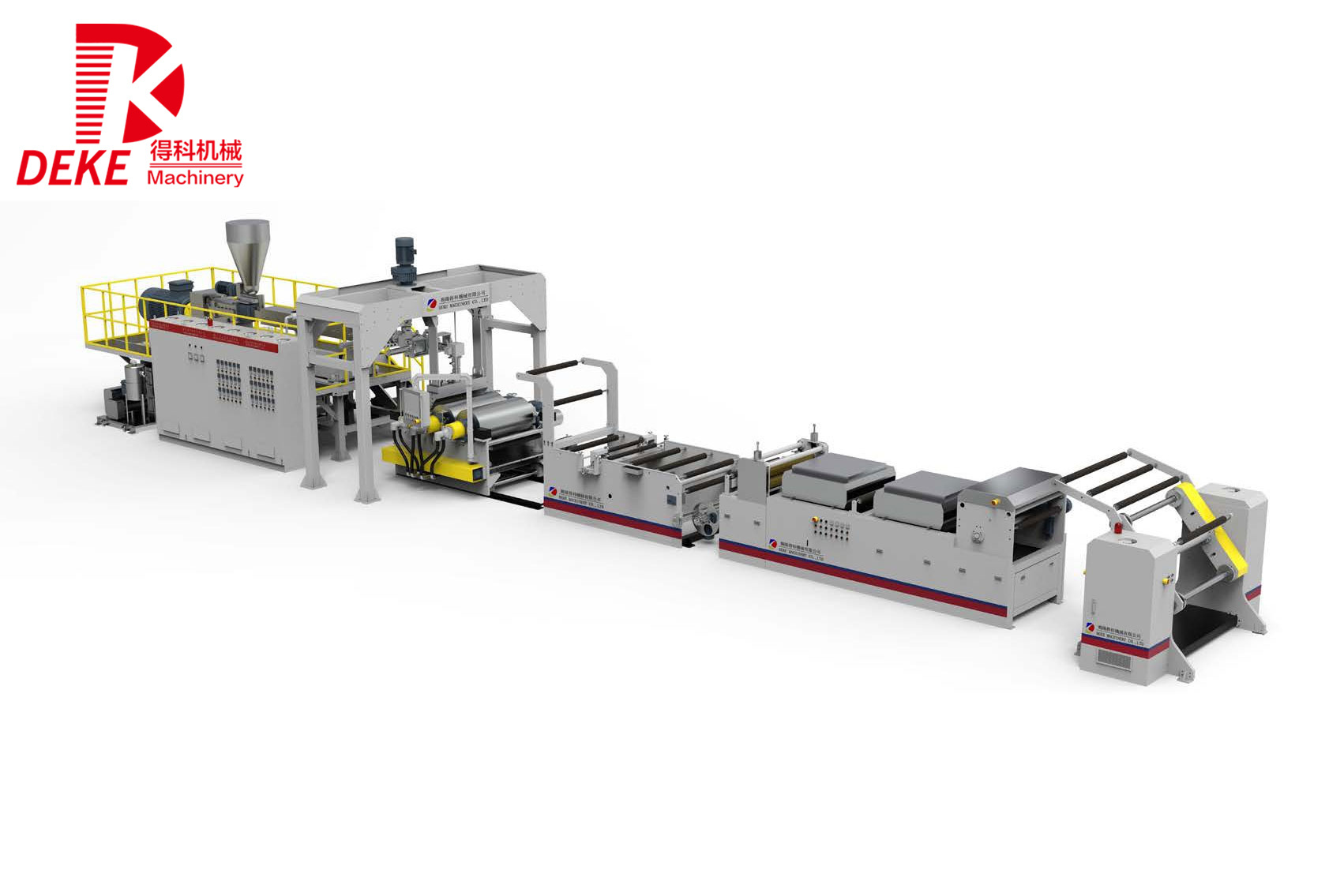
Innovative Applications of Parallel Twin Screw Extruder Technology
Introduction to Parallel Twin Screw Extruders
The **parallel twin screw extruder** has emerged as a pivotal technology in the realm of manufacturing, particularly within the plastic processing sector. Characterized by two intermeshing screws rotating in the same direction, these extruders are designed to efficiently mix, melt, and shape plastic materials. Their versatility and adaptability enable manufacturers to achieve precise control over the extrusion process, making them indispensable in producing high-quality plastic products.
Understanding the Mechanism of Parallel Twin Screw Extruders
To appreciate the innovations surrounding parallel twin screw extruders, it is essential to understand their functional mechanisms. The screws, which run parallel to each other, create a unique conveying and mixing action that facilitates effective material processing. The key components of this technology include:
1. Feeding System
The feeding system plays a critical role in determining the throughput and efficiency of the extruder. Materials such as pellets, powders, or flakes are introduced into the feeder, where they are metered into the screw channel for processing.
2. Heating and Cooling Zones
Parallel twin screw extruders are equipped with multiple heating and cooling zones that allow precise temperature control. This feature is crucial for managing material viscosity and achieving optimal melt flow characteristics.
3. Screw Configuration
The design of the screw geometry, including the pitch, depth, and arrangement, directly influences the mixing and conveying capabilities. Custom screw designs enable manufacturers to tailor the extruder to specific applications, enhancing performance and efficiency.
4. Die Design
The die at the end of the extrusion process shapes the molten material into the desired profile. Advanced die designs can produce complex shapes and ensure uniformity, catering to diverse product requirements.
Innovative Applications of Parallel Twin Screw Extruder Technology
Parallel twin screw extruders are making significant strides in various industries, thanks to their innovative applications. Here are some of the transformative uses of this technology:
1. Compounding of Plastic Materials
Compounding involves mixing various polymers and additives to enhance material properties. Parallel twin screw extruders excel in this area, allowing manufacturers to create high-performance materials with tailored characteristics. This versatility is essential for producing specialized compounds, such as flame-retardant plastics, which are increasingly in demand.
2. Production of Masterbatches
Masterbatch production involves the blending of colorants and additives into a carrier resin. The efficient mixing capabilities of parallel twin screw extruders enable the creation of uniform masterbatches that provide consistent color and performance. This application is vital for industries like packaging, automotive, and consumer goods.
3. Recycling of Plastics
Sustainability is at the forefront of modern manufacturing, and parallel twin screw extruders play a crucial role in plastic recycling. They facilitate the melting and reprocessing of post-consumer plastics, transforming waste into reusable materials. This innovative application contributes to reducing environmental impact while promoting a circular economy.
4. Production of Biodegradable Plastics
With the growing demand for environmentally friendly alternatives, parallel twin screw extruders are being utilized to produce biodegradable plastics. These extruders enable the blending of biodegradable polymers with traditional plastics, resulting in materials that retain performance while minimizing ecological footprints.
5. Food Industry Applications
In the food sector, parallel twin screw extruders are utilized for producing snacks, cereals, and other processed foods. The technology supports efficient cooking, texturizing, and flavor infusion, ensuring high-quality products that meet consumer expectations.
6. Pharmaceutical Applications
The pharmaceutical industry is leveraging parallel twin screw extruder technology for the production of drug formulations. This process allows for precise control of ingredient mixing and temperature, essential for ensuring the efficacy and safety of medications. The capability to produce micro-pellets and sustained-release formulations makes this technology vital in pharmaceutical manufacturing.
7. Polymer Blending
The blending of different polymers to create alloys or new materials is another innovative application of parallel twin screw extruders. By controlling the flow and mixing of various plastics, manufacturers can achieve unique properties such as improved toughness or flexibility.
8. Additive Manufacturing
As additive manufacturing (3D printing) gains traction, parallel twin screw extruders are being adapted to create filament for 3D printers. This allows for the production of high-quality, custom filaments that meet specific printing requirements, further expanding the potential of 3D printing technologies.
Benefits of Parallel Twin Screw Extruder Technology
The adoption of parallel twin screw extruders offers several advantages that contribute to their growing popularity in various industries:
1. Enhanced Mixing and Homogeneity
The intermeshing design of parallel twin screw extruders ensures thorough mixing of materials, resulting in homogeneous products. This is particularly important in applications where consistency and uniformity are critical.
2. Flexibility and Customization
Manufacturers can easily adapt parallel twin screw extruders to accommodate different materials and formulations. This flexibility allows for the rapid production of diverse products without extensive equipment changes.
3. Energy Efficiency
Parallel twin screw extruders are designed to operate with lower energy consumption compared to traditional extrusion methods. Their efficient heating and cooling systems contribute to reduced operational costs and minimized environmental impact.
4. Reduced Processing Times
The advanced mixing capabilities of parallel twin screw extruders enable faster processing times. This efficiency is crucial for meeting the demands of high-volume production while maintaining product quality.
5. Improved Product Quality
With precise control over processing parameters, parallel twin screw extruders enhance the overall quality of the end products. This improvement minimizes defects and ensures that products meet stringent industry standards.
Future Trends in Parallel Twin Screw Extruder Technology
As technology continues to evolve, the future of parallel twin screw extruders looks promising. Here are some trends to watch for:
1. Integration of Industry 4.0 Technologies
The incorporation of smart technologies, such as IoT and machine learning, into parallel twin screw extruders will enhance monitoring and control capabilities. This integration will enable manufacturers to optimize processes in real-time, leading to increased efficiency and reduced downtime.
2. Advancements in Material Science
Ongoing research in material science will lead to the development of new polymers and composites that can be processed with parallel twin screw extruders. This innovation will expand the range of applications and open new market opportunities.
3. Sustainability Initiatives
As industries strive for sustainability, the demand for eco-friendly materials will continue to grow. Parallel twin screw extruders will play a vital role in producing biodegradable and recyclable plastics, aligning with global sustainability goals.
4. Customization and Automation
The trend towards customization in manufacturing will drive the demand for parallel twin screw extruders capable of handling unique formulations. Automated systems will enhance precision and reduce labor costs, making production more efficient.
Frequently Asked Questions (FAQs)
1. What is a parallel twin screw extruder?
A parallel twin screw extruder is a type of extrusion machine that features two intermeshing screws. This design allows for efficient mixing, melting, and shaping of plastic materials.
2. What industries benefit from parallel twin screw extruder technology?
Various industries benefit, including plastics manufacturing, food processing, pharmaceuticals, and recycling.
3. How does a parallel twin screw extruder improve product quality?
The precise control over temperature and mixing ensures uniformity and consistency in the final product, reducing defects.
4. Can parallel twin screw extruders be used for recycling plastics?
Yes, they are highly effective in recycling post-consumer plastics, transforming waste materials into reusable resources.
5. What are the future trends in parallel twin screw extruder technology?
Future trends include the integration of smart technologies, advancements in material science, a focus on sustainability, and increased automation.
Conclusion
The **innovative applications** of parallel twin screw extruder technology are reshaping the manufacturing landscape, particularly in the plastic processing sector. With their unique capabilities for mixing, compounding, and recycling materials, these extruders are at the forefront of modern manufacturing solutions. As industries continue to embrace sustainability and efficiency, the potential for parallel twin screw extruders will only grow, driving advancements that meet the challenges of tomorrow. By staying informed and adapting to these innovations, manufacturers can ensure they remain competitive in an ever-evolving marketplace.
RELATED INFORMATION
Understanding the Benefits and Applications of Parallel Twin Screw Extruders
In the realm of plastic processing machinery, the parallel twin screw extruder stands out as a versatile and effective solution for a variety of applications. This type of extruder is characterized by two screws that run parallel to each other, allowing for efficient melting, mixing, and compounding of materials. The design of the parallel twin screw extruder enables a uniform and consistent outpu
Innovative Applications of Parallel Twin Screw Extruder Technology in Modern Manufacturing
Innovative Applications of Parallel Twin Screw Extruder Technology Introduction to Parallel Twin Screw Extruders The **parallel twin screw extruder** has emerged as a pivotal technology in the realm of manufacturing, particularly within the plastic processing sector. Characterized by two intermeshing screws rotating in the same direction, these extruders are designed to efficiently mix, melt, and