How Twin Screw Extruders Revolutionize the Plastic Manufacturing Industry
2025-04
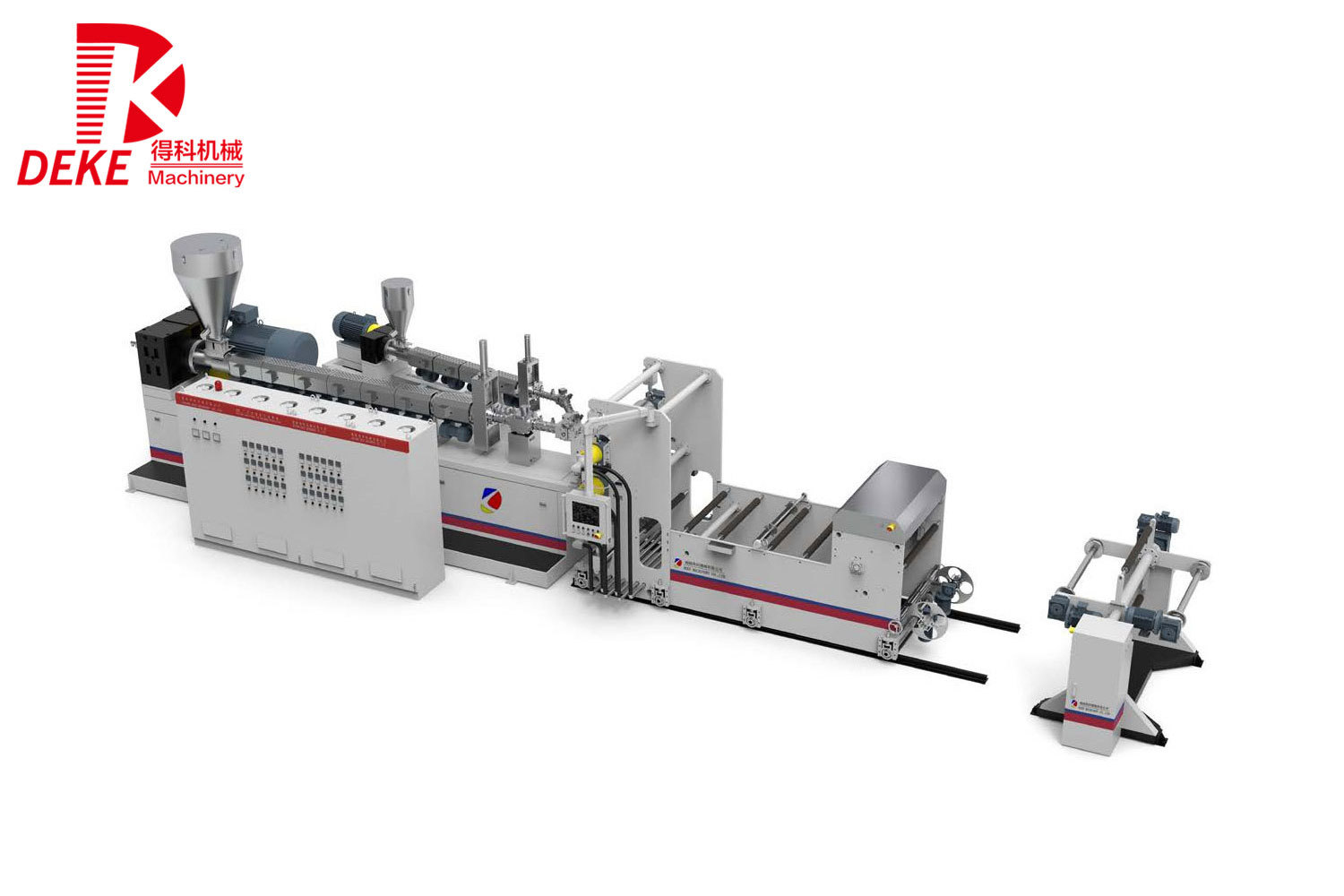
How Twin Screw Extruders Revolutionize the Plastic Manufacturing Industry
Table of Contents
- 1. Introduction to Twin Screw Extruders
- 2. Understanding Twin Screw Extruders
- 3. Advantages of Twin Screw Extruders in Plastic Manufacturing
- 4. Applications of Twin Screw Extruders
- 5. Comparison with Single Screw Extruders
- 6. The Role of Twin Screw Extruders in Plastic Recycling
- 7. Future Trends in Twin Screw Extrusion Technology
- 8. Conclusion
- 9. FAQs
1. Introduction to Twin Screw Extruders
The plastic manufacturing industry has undergone significant transformation, driven by technological advancements that enhance production efficiency and product quality. Among these innovations, **twin screw extruders** have emerged as a pivotal element, reshaping how plastics are processed and produced. These machines offer superior mixing capabilities, consistent output, and remarkable versatility, making them indispensable in various applications.
2. Understanding Twin Screw Extruders
Twin screw extruders are sophisticated machines that utilize two intermeshing screws for the extrusion process. Unlike their single screw counterparts, which rely on a single helical screw, twin screw extruders provide enhanced material handling and processing capabilities. This design allows for better mixing, compounding, and even the incorporation of additives during the extrusion process.
How Twin Screw Extruders Work
The operation of twin screw extruders involves the continuous feeding of raw materials into the extruder, where they are conveyed, melted, and shaped into the desired form. The intermeshing screws create a unique environment for the materials, allowing for efficient heat transfer and improved material properties.
Key Components of Twin Screw Extruders
The main components include the feed section, melting section, mixing section, and die. Each element plays a crucial role in ensuring the effective transformation of raw materials into high-quality plastic products.
3. Advantages of Twin Screw Extruders in Plastic Manufacturing
Twin screw extruders offer a multitude of advantages that make them a preferred choice in the plastic manufacturing sector. Here are some significant benefits:
Enhanced Mixing and Homogeneity
One of the primary advantages of twin screw extruders is their ability to achieve a high level of mixing and homogeneity. The intermeshing screws create a high shear environment, ensuring that all components are evenly distributed throughout the melt.
Improved Product Quality
The precise control over processing conditions allows manufacturers to produce high-quality plastic products with consistent properties and minimal defects. This is crucial for industries where product specifications are stringent.
Versatility in Processing
Twin screw extruders can process a wide variety of materials, including thermoplastics, thermosets, and even bioplastics. Their versatility makes them suitable for diverse applications, from automotive parts to medical devices.
Efficiency and Reduced Waste
The continuous operation of twin screw extruders leads to reduced cycle times and lower waste generation. This efficiency translates into cost savings for manufacturers while promoting sustainable practices.
Effective Additive Incorporation
Additives such as colorants, stabilizers, and fillers can be incorporated seamlessly into the material stream. This capability enhances the functional properties of the final product without compromising quality.
4. Applications of Twin Screw Extruders
The versatility of twin screw extruders allows them to be utilized across a variety of sectors. Some key applications include:
Automotive Industry
In the automotive industry, twin screw extruders are used to produce lightweight components that enhance fuel efficiency. Their capability to process reinforced plastics is particularly valuable for creating durable parts.
Packaging Solutions
In packaging, twin screw extruders play a critical role in producing films and containers that are not only strong but also environmentally friendly. They enable the use of bio-based materials and improved recyclability.
Consumer Goods
From household items to electronics, twin screw extruders are essential for manufacturing a wide range of consumer products. Their ability to create high-performance materials ensures that these goods meet consumer expectations.
Medical Devices
In the medical sector, precision and reliability are paramount. Twin screw extruders are employed to manufacture medical devices and components that require strict compliance with industry standards.
5. Comparison with Single Screw Extruders
While single screw extruders have been the traditional choice for plastic processing, twin screw extruders offer distinct advantages that set them apart.
Processing Capabilities
Twin screw extruders excel in processing complex formulations, enabling manufacturers to create innovative materials. Single screw extruders may struggle with certain blends, leading to variability in quality.
Mixing Efficiency
The mixing efficiency of twin screw extruders far surpasses that of single screw models. This efficiency is vital for producing consistent products, especially when working with additives.
Flexibility in Operations
Twin screw extruders provide greater flexibility in terms of processing parameters. Manufacturers can adjust screw configurations, temperatures, and speeds to optimize performance for specific applications.
6. The Role of Twin Screw Extruders in Plastic Recycling
As the push for sustainability intensifies, twin screw extruders are playing an increasingly vital role in plastic recycling. Their advanced design allows for the effective processing of recycled materials, ensuring that they can be reintroduced into the manufacturing cycle.
Processing Recycled Plastics
Twin screw extruders can handle contaminated and mixed plastic feedstocks, making them ideal for recycling operations. Their ability to effectively melt and homogenize these materials facilitates the production of high-quality recycled products.
Challenges and Solutions in Recycling
Recycling often presents challenges, such as material degradation and contamination. Twin screw extruders mitigate these issues through controlled processing conditions, enabling the production of materials that meet stringent quality standards.
7. Future Trends in Twin Screw Extrusion Technology
The future of twin screw extrusion is promising, with ongoing innovations poised to further enhance their capabilities.
Integration of Smart Technology
The incorporation of smart technology and Industry 4.0 principles will enable real-time monitoring and data analysis, optimizing processing conditions for improved efficiency and product quality.
Development of Sustainable Materials
As the industry moves towards sustainability, twin screw extruders will be crucial in developing and processing bio-based and biodegradable materials, aligning production with environmental goals.
Customization and Specialization
The demand for specialized materials will likely drive innovations in twin screw extruder design, enabling manufacturers to customize screw configurations and processing parameters for specific applications.
8. Conclusion
Twin screw extruders have undeniably revolutionized the plastic manufacturing industry by enhancing processing capabilities, product quality, and operational efficiency. As technology continues to advance, these machines will play an even more critical role in the evolution of plastic production, positioning manufacturers to meet both current and future challenges in a rapidly changing market. By embracing the advantages offered by twin screw extruders, companies can not only improve their bottom line but also contribute to a more sustainable and innovative plastic manufacturing landscape.
9. FAQs
What is a twin screw extruder?
A twin screw extruder is a machine that uses two intermeshing screws for the extrusion process, allowing for better mixing, compounding, and processing of materials compared to single screw extruders.
What are the main advantages of using twin screw extruders?
The main advantages include enhanced mixing and homogeneity, improved product quality, versatility in processing a wide range of materials, efficiency, and effective incorporation of additives.
In what industries are twin screw extruders commonly used?
Twin screw extruders are commonly used in the automotive, packaging, consumer goods, and medical device industries due to their versatility and high processing capabilities.
How do twin screw extruders facilitate plastic recycling?
Twin screw extruders can effectively process contaminated and mixed plastic feedstocks, producing high-quality recycled materials that can be reintroduced into the manufacturing cycle.
What future trends can we expect in twin screw extrusion technology?
Future trends may include the integration of smart technology, the development of sustainable materials, and customization of extruder designs to meet specialized processing needs.
RELATED INFORMATION
Understanding the Benefits and Applications of Parallel Twin Screw Extruders
In the realm of plastic processing machinery, the parallel twin screw extruder stands out as a versatile and effective solution for a variety of applications. This type of extruder is characterized by two screws that run parallel to each other, allowing for efficient melting, mixing, and compounding of materials. The design of the parallel twin screw extruder enables a uniform and consistent outpu
Innovative Applications of Parallel Twin Screw Extruder Technology in Modern Manufacturing
Innovative Applications of Parallel Twin Screw Extruder Technology Introduction to Parallel Twin Screw Extruders The **parallel twin screw extruder** has emerged as a pivotal technology in the realm of manufacturing, particularly within the plastic processing sector. Characterized by two intermeshing screws rotating in the same direction, these extruders are designed to efficiently mix, melt, and