Unlocking Efficiency: The Role of Twin Screw Extruders in Compounding
2025-04
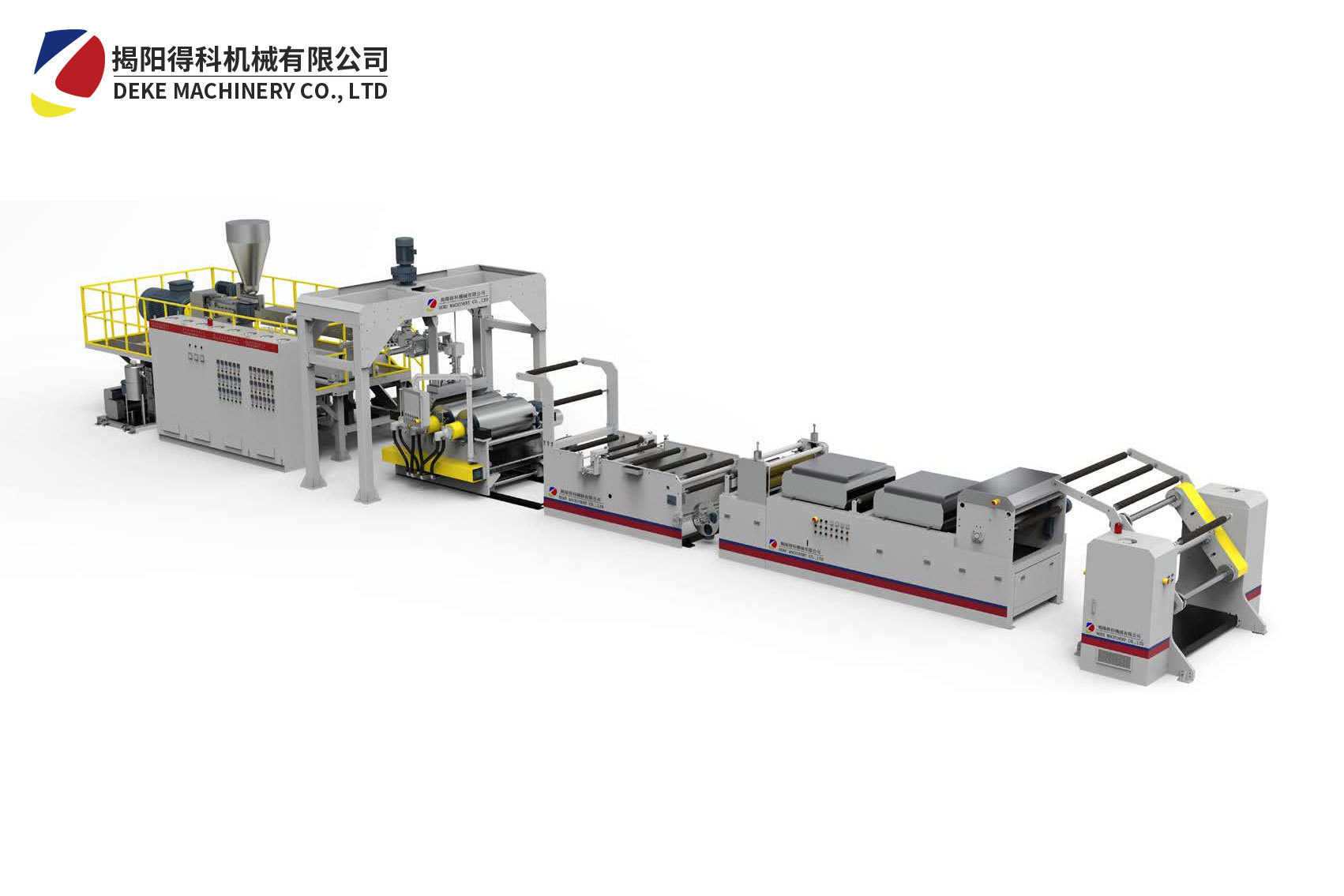
One of the key advantages of a twin screw extruder for compounding is its ability to precisely control the temperature and shear within the extruder barrel. This control is essential for processing heat-sensitive materials and achieving the desired viscosity and consistency of the final product. The twin screw configuration allows for both counter-rotation and co-rotation of the screws, which means that processors can choose the optimal flow dynamics for their specific applications. This flexibility is crucial, as different materials require different processing conditions to achieve the best results.
Moreover, twin screw extruders facilitate the incorporation of a wide range of additives and fillers during the compounding phase. This is particularly beneficial for manufacturers looking to enhance the physical properties of their products, such as improving strength, flexibility, or thermal stability. The extensive mixing action provided by the twin screws ensures uniform distribution of these additives, which is vital for maintaining the quality and performance of the final product.
Another significant factor to consider when discussing twin screw extruders for compounding is their ability to handle a variety of feed materials. Whether dealing with granules, powders, or even liquid additives, these extruders are designed to accommodate diverse input forms, thus increasing their versatility in manufacturing processes. This adaptability can greatly streamline production lines and reduce downtime associated with material changes.
In terms of maintenance and operational efficiency, twin screw extruders are engineered with user-friendly features that facilitate easy cleaning and maintenance, which is essential for maintaining high throughput and minimizing contamination between production runs. The modular design of many twin screw systems allows for quick exchanges of screw elements and barrels, enabling manufacturers to adapt their equipment to meet varying production requirements without extensive downtime.
In summary, a twin screw extruder for compounding is not just a piece of equipment; it is an essential tool that enhances productivity, quality, and flexibility in the plastic manufacturing industry. By leveraging the unique advantages of twin screw technology, manufacturers can optimize their compounding processes, resulting in superior products that meet the evolving demands of the market.
RELATED INFORMATION
Understanding the Benefits and Applications of Parallel Twin Screw Extruders
In the realm of plastic processing machinery, the parallel twin screw extruder stands out as a versatile and effective solution for a variety of applications. This type of extruder is characterized by two screws that run parallel to each other, allowing for efficient melting, mixing, and compounding of materials. The design of the parallel twin screw extruder enables a uniform and consistent outpu
Innovative Applications of Parallel Twin Screw Extruder Technology in Modern Manufacturing
Innovative Applications of Parallel Twin Screw Extruder Technology Introduction to Parallel Twin Screw Extruders The **parallel twin screw extruder** has emerged as a pivotal technology in the realm of manufacturing, particularly within the plastic processing sector. Characterized by two intermeshing screws rotating in the same direction, these extruders are designed to efficiently mix, melt, and