Exploring the Advantages of Twin Screw Extruders in Compounding Applications
2025-04
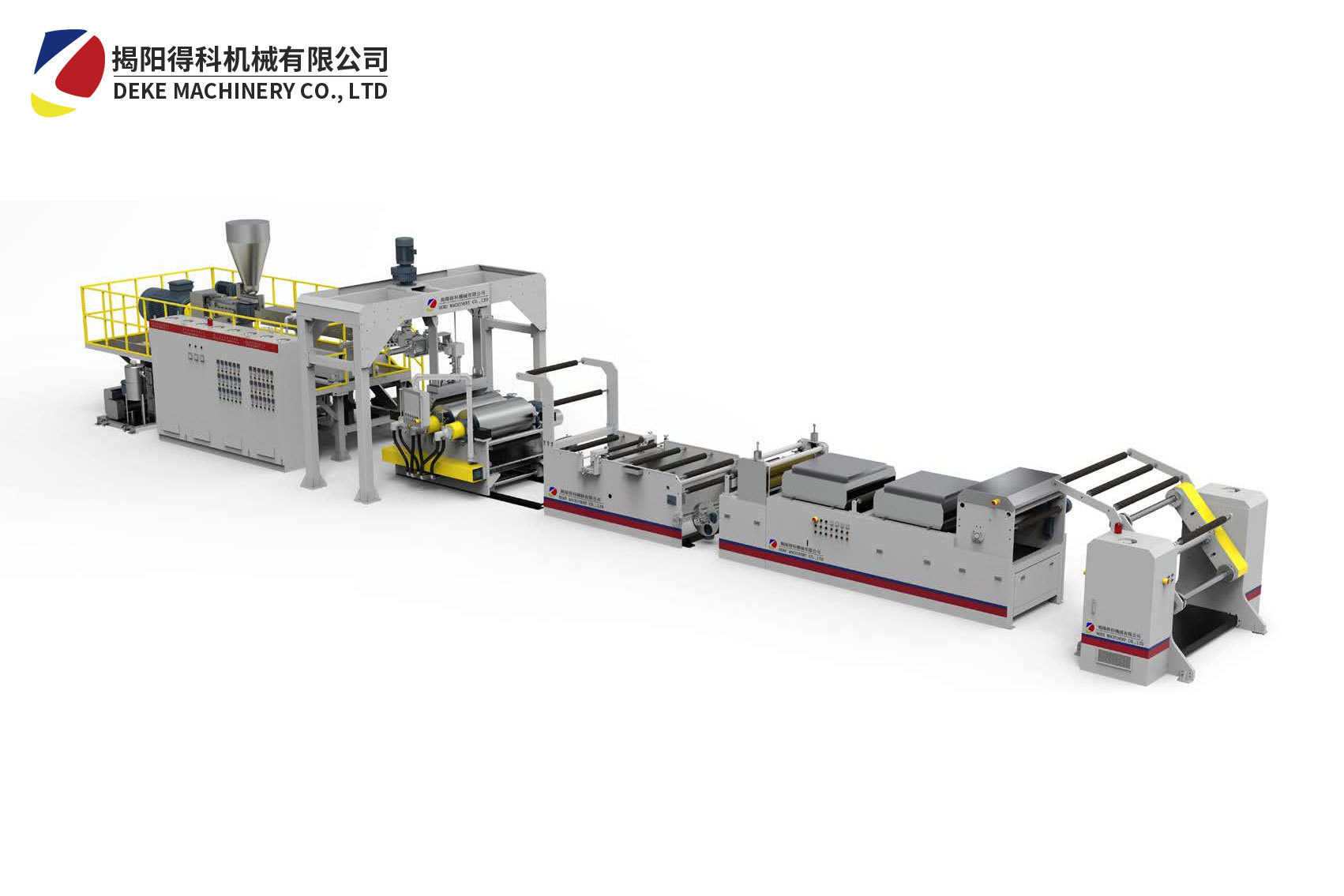
Exploring the Advantages of Twin Screw Extruders in Compounding Applications
Table of Contents
- Introduction to Twin Screw Extruders
- What Are Twin Screw Extruders?
- Key Advantages of Twin Screw Extruders in Compounding
- Superior Mixing Homogeneity
- Process Flexibility and Control
- Effective Thermal Management
- High Efficiency and Throughput
- Applications of Twin Screw Extruders in Compounding
- Case Studies of Successful Applications
- Frequently Asked Questions
- Conclusion
Introduction to Twin Screw Extruders
Twin screw extruders are pivotal in the field of plastic processing, especially in compounding applications. These advanced machines utilize two intermeshing screws that rotate within a barrel, allowing for enhanced mixing, reaction, and extrusion of materials. As industries evolve and the demand for high-quality compounded products increases, understanding the advantages of twin screw extruders becomes essential for manufacturers aiming to optimize their operations.
What Are Twin Screw Extruders?
Twin screw extruders are specialized equipment designed for the processing of thermoplastics and other materials. They consist of two parallel screws that rotate in the same or opposite directions. This unique design facilitates various operations, including mixing, compounding, and pelletizing. The co-rotating configuration offers distinct advantages in terms of material handling, allowing operators to achieve thorough mixing and uniform distribution of additives.
Key Advantages of Twin Screw Extruders in Compounding
Understanding the advantages of twin screw extruders is crucial for manufacturers looking to enhance their compounding processes. Here are the most significant benefits:
Superior Mixing Homogeneity
One of the standout features of twin screw extruders is their ability to achieve **superior mixing homogeneity**. The intermeshing screws ensure that materials are uniformly mixed, regardless of their viscosity. This uniformity leads to consistent product quality, which is vital in applications demanding high precision and reliability.
Process Flexibility and Control
Twin screw extruders offer remarkable **process flexibility**. Manufacturers can easily adjust the operational parameters, such as temperature, pressure, and screw speed, to suit various materials and formulations. This adaptability allows for the seamless incorporation of different additives, resulting in customized products that meet specific performance criteria.
Effective Thermal Management
Thermal management is critical in compounding processes, especially when dealing with heat-sensitive materials. Twin screw extruders provide **effective thermal control** through advanced heating and cooling systems integrated into the barrel. This feature helps maintain optimal processing temperatures, minimizing the risk of thermal degradation and ensuring the quality of the final product.
High Efficiency and Throughput
When it comes to production efficiency, twin screw extruders excel. They are designed to achieve **high throughput rates**, making them ideal for large-scale production. The efficient material transport and mixing capabilities reduce processing times, enabling manufacturers to meet increasing market demands without compromising quality.
Applications of Twin Screw Extruders in Compounding
The versatility of twin screw extruders opens them to various applications across multiple industries. Here are some primary applications where these machines shine:
Plastics and Polymers
In the plastics industry, twin screw extruders are widely used for compounding various polymers. They are essential for blending different types of plastics, adding fillers, or modifying the properties of materials to enhance performance. Their ability to achieve consistent mixing and maintain product integrity makes them a preferred choice among manufacturers.
Masterbatch Production
Twin screw extruders are also crucial in producing masterbatches, which are concentrated mixtures of pigments and additives. The precise control offered by twin screw technology allows for the creation of high-quality masterbatches that can be easily incorporated into final products, improving coloration and performance characteristics.
Biodegradable Materials
As sustainability becomes a priority, twin screw extruders are increasingly utilized in processing biodegradable materials. These machines facilitate the incorporation of renewable resources into formulations, allowing manufacturers to produce environmentally friendly products without sacrificing performance.
Case Studies of Successful Applications
Examining real-world applications of twin screw extruders can provide valuable insights into their advantages. Here are a few noteworthy case studies:
1. **Automotive Industry**: A leading automotive manufacturer implemented twin screw extruders for compounding reinforced plastics, resulting in lighter and more fuel-efficient vehicles.
2. **Food Packaging**: A company specializing in food packaging used twin screw technology to develop biodegradable materials for their products, significantly reducing their environmental footprint.
3. **Biomedical Devices**: In the biomedical sector, twin screw extruders were employed to compound polymers for producing devices with specific mechanical properties, improving patient outcomes.
Frequently Asked Questions
1. What is the main difference between a single screw and a twin screw extruder?
The primary difference lies in the design and mixing capabilities. Twin screw extruders offer better mixing and more control over the processing conditions compared to single screw extruders.
2. Can twin screw extruders handle high-viscosity materials?
Yes, twin screw extruders are well-suited for high-viscosity materials, thanks to their unique design that allows for effective material transport and mixing.
3. How do twin screw extruders improve product quality?
They enhance product quality by achieving superior mixing homogeneity, allowing for consistent dispersion of additives and uniform material properties.
4. What are the maintenance requirements for twin screw extruders?
Regular maintenance includes cleaning, checking for wear on screws and barrels, and monitoring the temperature control systems to ensure optimal performance.
5. Are twin screw extruders suitable for small-scale production?
While they are primarily used for large-scale production, twin screw extruders can be adapted for small-scale applications, making them versatile for various manufacturing needs.
Conclusion
Twin screw extruders represent a significant advancement in compounding applications, offering unparalleled benefits that enhance manufacturing processes across various industries. Their superior mixing capabilities, process flexibility, effective thermal management, and high efficiency make them the go-to choice for manufacturers seeking to optimize their operations. By exploring the advantages of twin screw extruders, businesses can position themselves for success in an increasingly competitive marketplace, delivering high-quality products that meet evolving consumer demands. As technology continues to advance, the role of twin screw extruders in shaping the future of compounding applications will undoubtedly grow, making them an investment worth considering for any manufacturer.
RELATED INFORMATION
Understanding the Benefits and Applications of Parallel Twin Screw Extruders
In the realm of plastic processing machinery, the parallel twin screw extruder stands out as a versatile and effective solution for a variety of applications. This type of extruder is characterized by two screws that run parallel to each other, allowing for efficient melting, mixing, and compounding of materials. The design of the parallel twin screw extruder enables a uniform and consistent outpu
Innovative Applications of Parallel Twin Screw Extruder Technology in Modern Manufacturing
Innovative Applications of Parallel Twin Screw Extruder Technology Introduction to Parallel Twin Screw Extruders The **parallel twin screw extruder** has emerged as a pivotal technology in the realm of manufacturing, particularly within the plastic processing sector. Characterized by two intermeshing screws rotating in the same direction, these extruders are designed to efficiently mix, melt, and