Unlocking the Potential of PP HIPS Sheet Extruders in Modern Manufacturing
2025-04
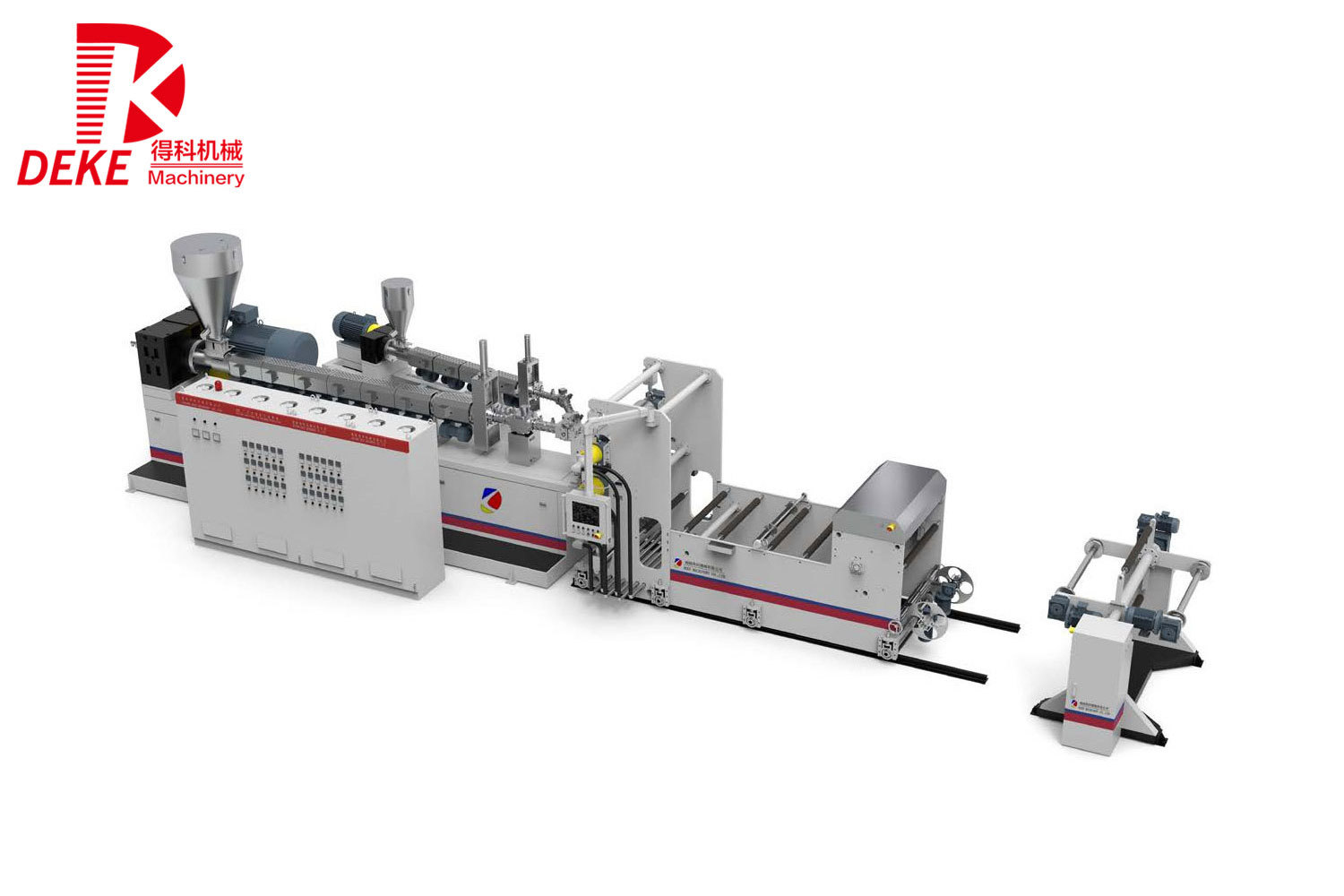
The core function of a PP HIPS sheet extruder is to melt and reshape thermoplastic materials into continuous sheets. This process involves a series of steps that include feeding raw plastic pellets into a hopper, where they are then conveyed into a heated barrel. Within the barrel, the pellets undergo a melting process through the application of heat and mechanical shear forces generated by rotating screws. The resulting molten plastic is then forced through a flat die, producing a sheet of desired thickness.
One of the key benefits of using a PP HIPS sheet extruder is its efficiency. Modern machines are designed to maximize output while minimizing energy consumption. By optimizing the temperature control and screw design, manufacturers can achieve a smooth and consistent flow of material, which is crucial for producing high-quality sheets. Additionally, advancements in automation and control technologies enable operators to monitor and adjust the extrusion process in real-time, further enhancing production efficiency.
Versatility is another significant advantage of PP HIPS sheet extruders. These machines can handle a wide range of materials and formulations, allowing manufacturers to experiment with different blends to achieve specific properties. For instance, adding certain additives can enhance the impact resistance or UV stability of the sheets produced. This adaptability means that manufacturers can cater to various industries and customer preferences without needing to invest in multiple specialized machines.
The applications of PP HIPS sheets are extensive. In the packaging industry, these sheets are commonly used for creating containers, trays, and clamshells that require durability and aesthetic appeal. In signage, they provide a robust solution for outdoor and indoor displays, resisting fading and wear. Automotive manufacturers appreciate the lightweight yet strong characteristics of PP HIPS sheets for interior parts, contributing to overall vehicle efficiency.
In conclusion, the PP HIPS sheet extruder is an indispensable tool in the manufacturing landscape, offering efficiency, versatility, and a wide range of applications. By investing in this technology, manufacturers can enhance their production capabilities, meet diverse market demands, and maintain a competitive edge in the plastic processing industry. Understanding the intricacies of the PP HIPS sheet extrusion process can empower industry professionals to make informed decisions that drive growth and innovation.
RELATED INFORMATION
Understanding the Benefits and Applications of Parallel Twin Screw Extruders
In the realm of plastic processing machinery, the parallel twin screw extruder stands out as a versatile and effective solution for a variety of applications. This type of extruder is characterized by two screws that run parallel to each other, allowing for efficient melting, mixing, and compounding of materials. The design of the parallel twin screw extruder enables a uniform and consistent outpu
Innovative Applications of Parallel Twin Screw Extruder Technology in Modern Manufacturing
Innovative Applications of Parallel Twin Screw Extruder Technology Introduction to Parallel Twin Screw Extruders The **parallel twin screw extruder** has emerged as a pivotal technology in the realm of manufacturing, particularly within the plastic processing sector. Characterized by two intermeshing screws rotating in the same direction, these extruders are designed to efficiently mix, melt, and