How to Optimize Your Production Line with a PP HIPS Sheet Extruder
2025-04
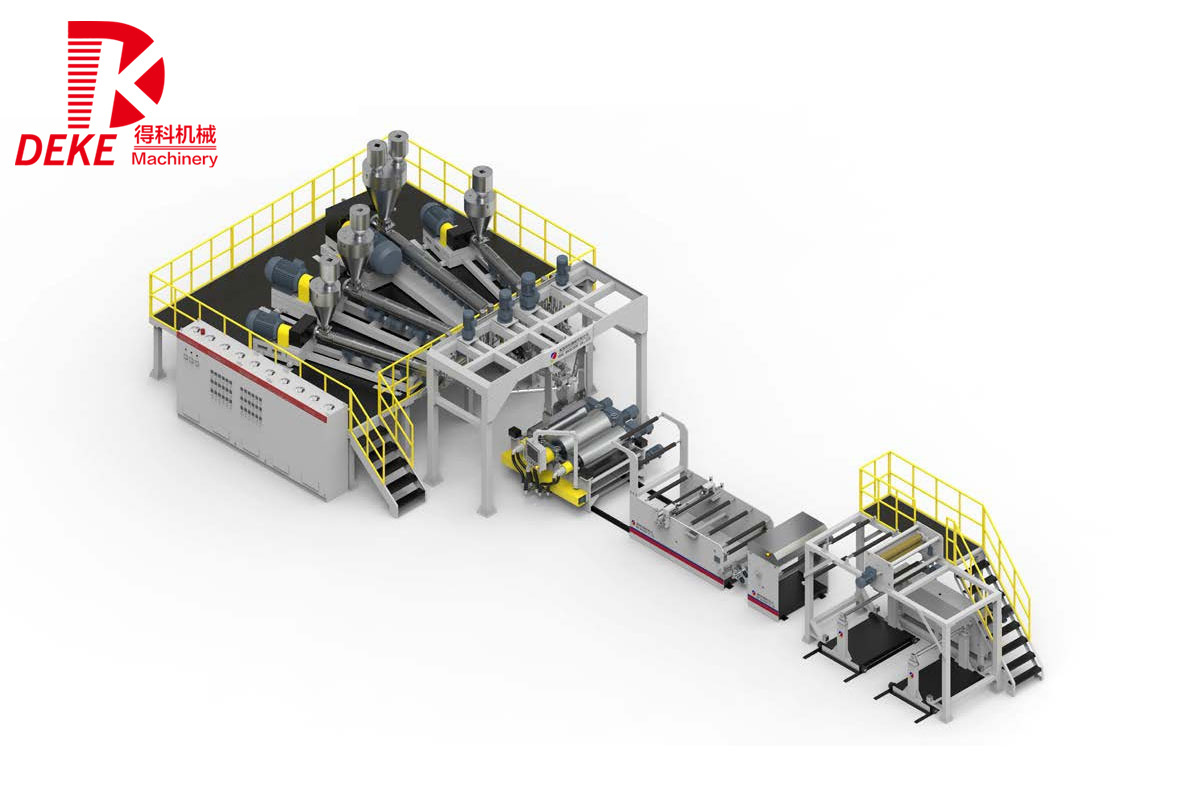
How to Optimize Your Production Line with a PP HIPS Sheet Extruder
Table of Contents
- Understanding PP HIPS Sheet Extruders
- The Importance of Optimization in Manufacturing
- Key Components of PP HIPS Sheet Extruders
- Steps to Optimize Your Production Line
- Monitoring and Maintaining Your Equipment
- Case Studies and Success Stories
- Challenges and Solutions in Extrusion Processes
- Future Trends in Extrusion Technology
- FAQs about PP HIPS Sheet Extruders
Understanding PP HIPS Sheet Extruders
PP (Polypropylene) and HIPS (High Impact Polystyrene) sheet extruders are specialized machines designed for the continuous production of plastic sheets utilized in various industries. These machines convert raw plastic pellets into finished sheets through a series of heating, melting, and shaping processes. The versatility of PP and HIPS materials makes them ideal for applications ranging from packaging to construction, automotive parts, and consumer goods.
The Importance of Optimization in Manufacturing
Optimization is critical in manufacturing, particularly in extrusion processes, where efficiency and quality directly affect profitability. Streamlining operations minimizes waste, reduces downtime, and enhances product quality. The quest for optimization in your production line can lead to significant improvements in overall performance metrics, driving your business forward in a competitive landscape.
Benefits of Optimizing Your Production Line
1. **Increased Efficiency**: By fine-tuning the extrusion process, manufacturers can achieve higher throughput rates.
2. **Cost Reduction**: Efficient use of materials and energy leads to lower operational costs.
3. **Enhanced Product Quality**: Streamlined processes ensure uniformity and reduce defects in production.
4. **Sustainability**: Minimizing waste contributes to more environmentally friendly operations.
Key Components of PP HIPS Sheet Extruders
Understanding the essential components of a PP HIPS sheet extruder is fundamental to optimizing your production line. The main elements include:
1. Hopper
The hopper is where raw plastic pellets are fed into the machine. Proper loading techniques can prevent bridging and ensure a steady flow of material.
2. Screw and Barrel
The screw, coupled with the barrel, plays a crucial role in melting and mixing the plastic. Factors such as screw design, length, and temperature profile should be optimized for different materials.
3. Die Head
The die head shapes the molten plastic into sheets. Optimizing the die design can enhance flow rates and ensure uniform thickness.
4. Calendering System
This component further flattens and cools the sheets to achieve the desired thickness and surface quality.
Steps to Optimize Your Production Line
To effectively optimize your production line with a PP HIPS sheet extruder, consider the following steps:
1. Assess Current Processes
Conduct a thorough evaluation of your existing production line to identify bottlenecks and inefficiencies.
2. Adjust Process Parameters
Modify temperature settings, screw speeds, and feed rates based on the specific material being used. Each adjustment should be made while closely monitoring output quality.
3. Implement Automation
Utilizing automation technologies such as sensors and control systems helps in real-time monitoring, allowing for swift adjustments to maintain optimal conditions.
4. Train Your Workforce
Investing in training for your employees on best practices in operating the extrusion machinery can lead to better adherence to optimized processes.
5. Utilize Advanced Technologies
Consider integrating advanced technologies such as predictive maintenance tools and data analytics to analyze production patterns and predict potential failures.
Monitoring and Maintaining Your Equipment
Regular monitoring and maintenance are critical for ensuring that your PP HIPS sheet extruder operates at peak performance. Scheduled maintenance checks can prevent costly breakdowns and extend the lifespan of the machinery.
1. Routine Inspections
Conduct daily inspections to check for wear and tear on components like screws, barrels, and die heads.
2. Lubrication and Cleaning
Regular lubrication of moving parts and thorough cleaning of the extruder will prevent material buildup and mechanical failures.
3. Performance Metrics Tracking
Establish KPIs (Key Performance Indicators) to measure the performance of the extrusion line, such as output rates, energy consumption, and scrap rates.
Case Studies and Success Stories
Several manufacturers have successfully optimized their PP HIPS sheet production lines, leading to remarkable improvements:
1. Company A's Efficiency Boost
After implementing real-time monitoring systems, Company A reduced downtime by 20% and increased production output by 25%.
2. Company B's Cost Savings
Through precise adjustments in the extrusion process, Company B reduced material waste by 15%, resulting in significant cost savings.
Challenges and Solutions in Extrusion Processes
While optimizing production lines, manufacturers may encounter various challenges:
1. Material Variability
Solution: Conduct thorough material testing and adjust process parameters to accommodate different material characteristics.
2. Equipment Failures
Solution: Implement a predictive maintenance program to identify potential issues before they lead to breakdowns.
3. Quality Control Issues
Solution: Utilize advanced quality control technologies, such as vision systems and inline measurements, to monitor output quality instantly.
Future Trends in Extrusion Technology
The extrusion technology landscape is continually evolving. Some emerging trends include:
1. Sustainable Materials
The industry is shifting towards using recycled and bio-based materials to enhance sustainability.
2. Industry 4.0 Integration
Smart factories are becoming a reality, with IoT (Internet of Things) devices being used to enhance the connectivity of machines and processes.
3. Advanced Simulation Software
Software that simulates extrusion processes is becoming increasingly popular, enabling manufacturers to optimize processes before implementation.
FAQs about PP HIPS Sheet Extruders
1. What materials can be processed using a PP HIPS sheet extruder?
PP HIPS sheet extruders are designed to process a variety of materials, including polypropylene, high-impact polystyrene, and other thermoplastics.
2. How often should I perform maintenance on my extruder?
Routine maintenance should be conducted at least once a month, with daily inspections for immediate wear and tear.
3. What are the signs of an underperforming extruder?
Indicators include inconsistent sheet thickness, excessive scrap rates, and frequent equipment failures.
4. Can I retrofit my existing extruder with automation features?
Yes, many older extruders can be retrofitted with modern automation technologies to enhance performance.
5. What is the expected lifespan of a PP HIPS sheet extruder?
With proper maintenance, a PP HIPS sheet extruder can last anywhere from 10 to 20 years, depending on usage and care.
Conclusion
Enhancing your production line with a PP HIPS sheet extruder is a strategic investment that can lead to increased efficiency, reduced costs, and superior product quality. By understanding the intricacies of these machines, implementing optimization strategies, and committing to ongoing maintenance, manufacturers position themselves for success in the dynamic world of plastic processing. The future of extrusion technology promises even greater advancements, making now the perfect time to embrace optimization for your production line.
Previous Page:
RELATED INFORMATION
Understanding the Benefits and Applications of Parallel Twin Screw Extruders
In the realm of plastic processing machinery, the parallel twin screw extruder stands out as a versatile and effective solution for a variety of applications. This type of extruder is characterized by two screws that run parallel to each other, allowing for efficient melting, mixing, and compounding of materials. The design of the parallel twin screw extruder enables a uniform and consistent outpu
Innovative Applications of Parallel Twin Screw Extruder Technology in Modern Manufacturing
Innovative Applications of Parallel Twin Screw Extruder Technology Introduction to Parallel Twin Screw Extruders The **parallel twin screw extruder** has emerged as a pivotal technology in the realm of manufacturing, particularly within the plastic processing sector. Characterized by two intermeshing screws rotating in the same direction, these extruders are designed to efficiently mix, melt, and