Understanding the Functionality and Benefits of PP HIPS Sheet Extruders in Plastic Processing
2025-04
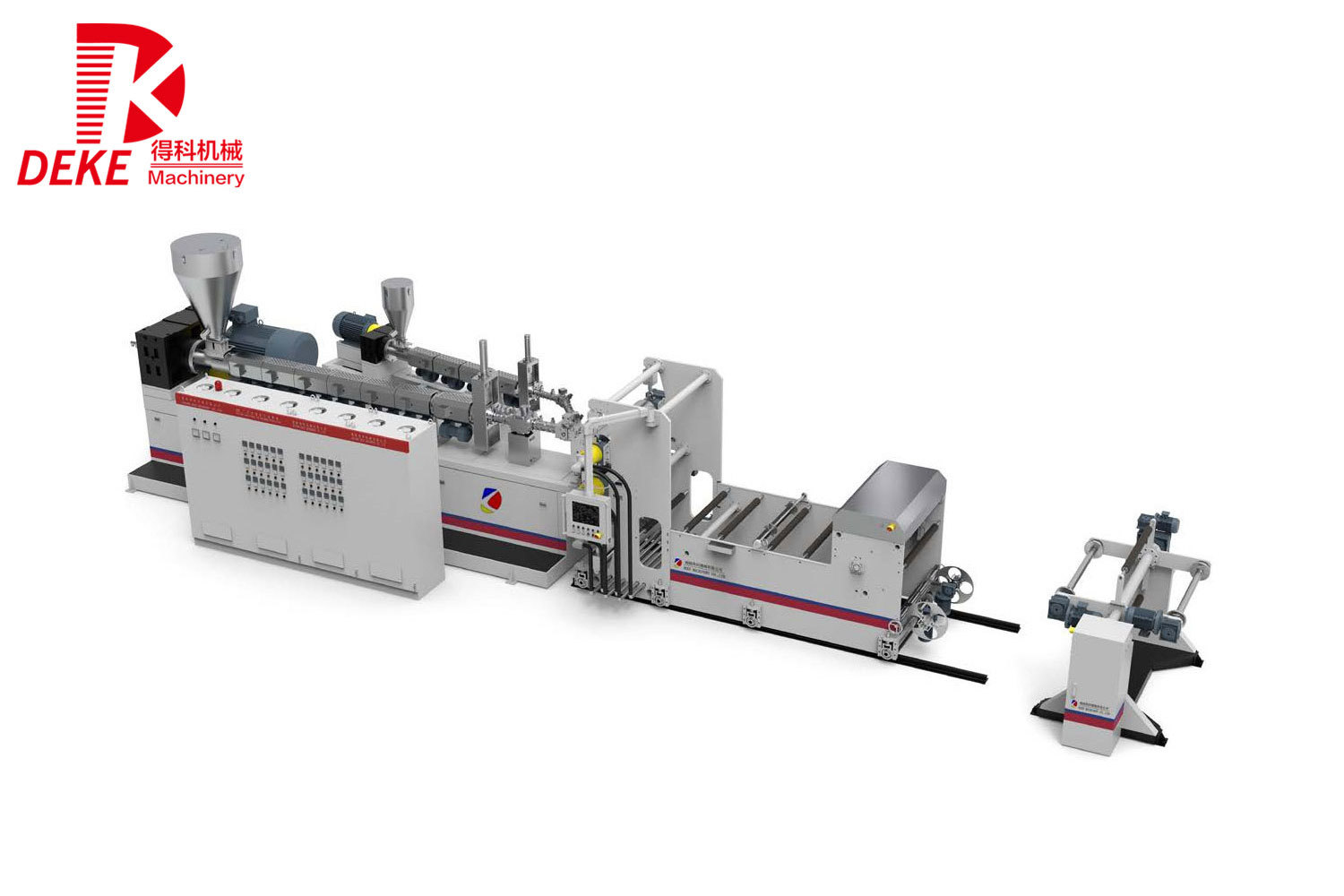
One of the primary benefits of using a PP HIPS sheet extruder lies in its versatility. This machinery can easily adapt to different production requirements, allowing manufacturers to create sheets of varying thicknesses and dimensions. This flexibility is essential for meeting the diverse needs of industries such as packaging, construction, and automotive, where specific sheet characteristics are often necessary.
The operational principle of a PP HIPS sheet extruder involves several key components, including the feed zone, melting zone, and die. Raw plastic pellets are fed into the extruder, where they are gradually heated and melted. The melting process transforms the solid pellets into a viscous liquid state, which is then forced through a die to form a continuous sheet. The ability to maintain precise temperature control throughout this process is crucial, as it ensures the integrity and quality of the final product.
Another significant advantage of a PP HIPS sheet extruder is its energy efficiency. Modern extruders are designed to optimize energy consumption while maximizing output. This is achieved through advancements in technology, such as better thermal insulation and improved screw designs that enhance material flow and reduce friction. As a result, manufacturers can not only decrease operational costs but also contribute to more sustainable production practices.
When considering the implementation of a PP HIPS sheet extruder, it is essential to take into account several factors. Proper maintenance and regular inspections are vital to ensure optimal performance and longevity of the machine. Manufacturers should also invest in training for their operators to ensure they understand the intricacies of the equipment and can troubleshoot any issues that may arise during production.
In conclusion, the PP HIPS sheet extruder plays a critical role in the plastic processing industry, offering versatility, energy efficiency, and high-quality output. By understanding its functionality and benefits, manufacturers can make informed decisions that enhance their production capabilities and help them meet the ever-evolving demands of the market. Whether for packaging, construction, or other applications, the PP HIPS sheet extruder remains a valuable asset in the realm of plastic manufacturing.
RELATED INFORMATION
Understanding the Benefits and Applications of Parallel Twin Screw Extruders
In the realm of plastic processing machinery, the parallel twin screw extruder stands out as a versatile and effective solution for a variety of applications. This type of extruder is characterized by two screws that run parallel to each other, allowing for efficient melting, mixing, and compounding of materials. The design of the parallel twin screw extruder enables a uniform and consistent outpu
Innovative Applications of Parallel Twin Screw Extruder Technology in Modern Manufacturing
Innovative Applications of Parallel Twin Screw Extruder Technology Introduction to Parallel Twin Screw Extruders The **parallel twin screw extruder** has emerged as a pivotal technology in the realm of manufacturing, particularly within the plastic processing sector. Characterized by two intermeshing screws rotating in the same direction, these extruders are designed to efficiently mix, melt, and