Understanding PET Sheet Extruder Machines: A Key Component in Plastic Manufacturing
2025-04
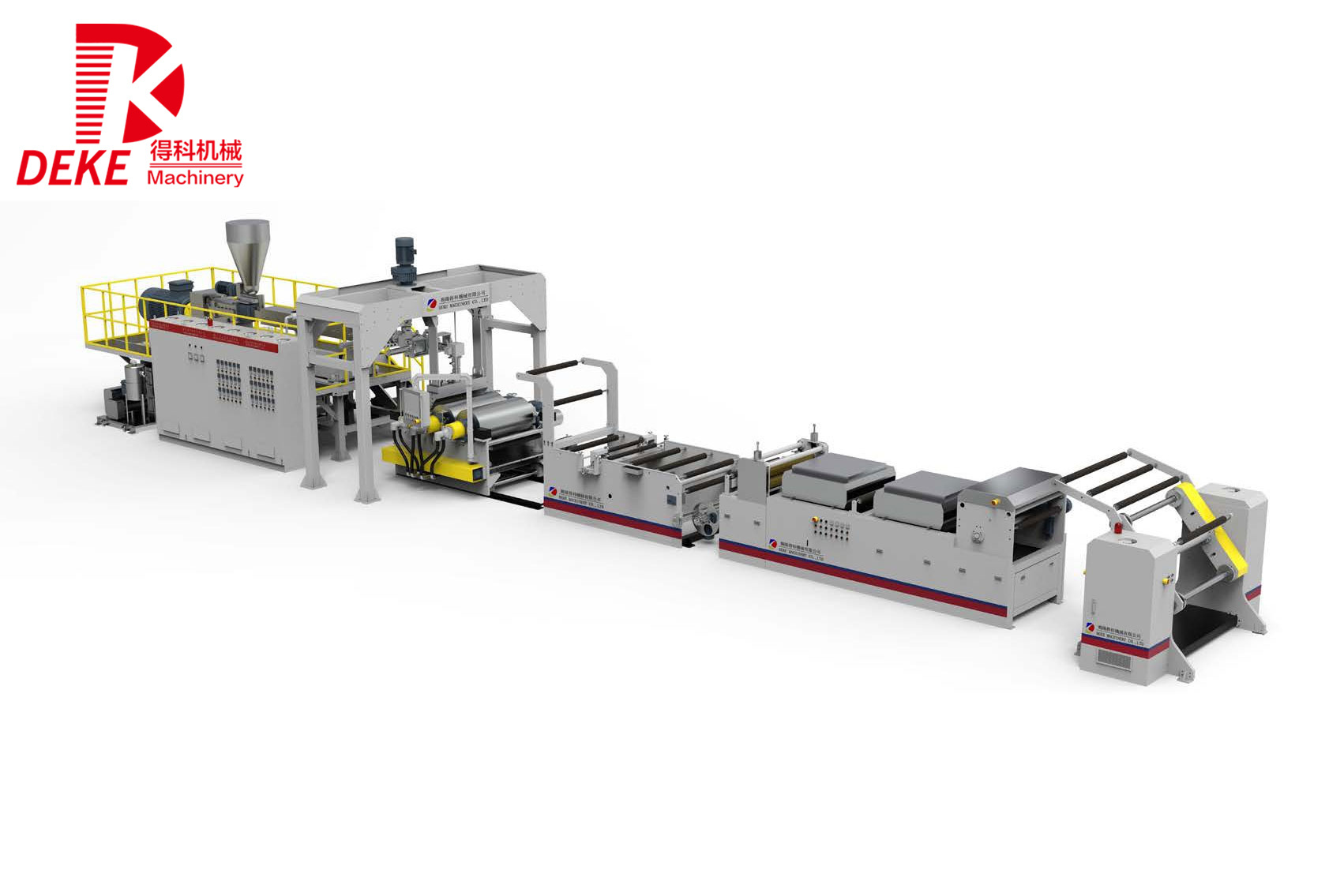
At its core, a PET sheet extruder machine consists of several key components: a hopper, extruder, die, cooling system, and winding unit. The process begins with feeding raw PET pellets into the hopper, where they are subjected to heat and pressure inside the extruder. The extruder melts the pellets and forces the molten material through a die, shaping it into a flat sheet. This sheet then undergoes cooling, solidifying into the desired thickness and properties before being wound up for further processing or distribution.
One of the primary advantages of PET sheet extruder machines is their ability to produce sheets with excellent clarity and dimensional stability. This makes them ideal for applications that require high optical quality, such as packaging for food products and electronic devices. Additionally, PET sheets exhibit good chemical resistance, making them suitable for industries that handle various substances without compromising the integrity of the material.
Another significant benefit of using a PET sheet extruder machine is the environmental aspect. PET is 100% recyclable, and the use of recycled PET pellets can further reduce production costs and environmental impact. Manufacturers that invest in this technology not only meet sustainability goals but also cater to the growing consumer demand for eco-friendly products.
Furthermore, the versatility of PET sheet extruder machines allows for customization. By adjusting the processing parameters, manufacturers can create sheets with varying thicknesses, colors, and finishes, catering to specific customer requirements. This customization capability expands the market reach and offers competitive advantages.
In summary, the PET sheet extruder machine is a vital asset in the plastic manufacturing industry. It enables the efficient production of high-quality PET sheets that are not only versatile and durable but also environmentally friendly. For professionals in the field, understanding the operation and benefits of these machines can lead to informed decisions that enhance productivity and sustainability in their manufacturing processes. As the demand for PET products continues to rise, investing in advanced PET sheet extruder technology will be essential for staying competitive in this dynamic industry.
RELATED INFORMATION
Understanding the Benefits and Applications of Parallel Twin Screw Extruders
In the realm of plastic processing machinery, the parallel twin screw extruder stands out as a versatile and effective solution for a variety of applications. This type of extruder is characterized by two screws that run parallel to each other, allowing for efficient melting, mixing, and compounding of materials. The design of the parallel twin screw extruder enables a uniform and consistent outpu
Innovative Applications of Parallel Twin Screw Extruder Technology in Modern Manufacturing
Innovative Applications of Parallel Twin Screw Extruder Technology Introduction to Parallel Twin Screw Extruders The **parallel twin screw extruder** has emerged as a pivotal technology in the realm of manufacturing, particularly within the plastic processing sector. Characterized by two intermeshing screws rotating in the same direction, these extruders are designed to efficiently mix, melt, and