Why Choosing a Twin Screw Compounder Can Transform Your Plastic Manufacturing
2025-07
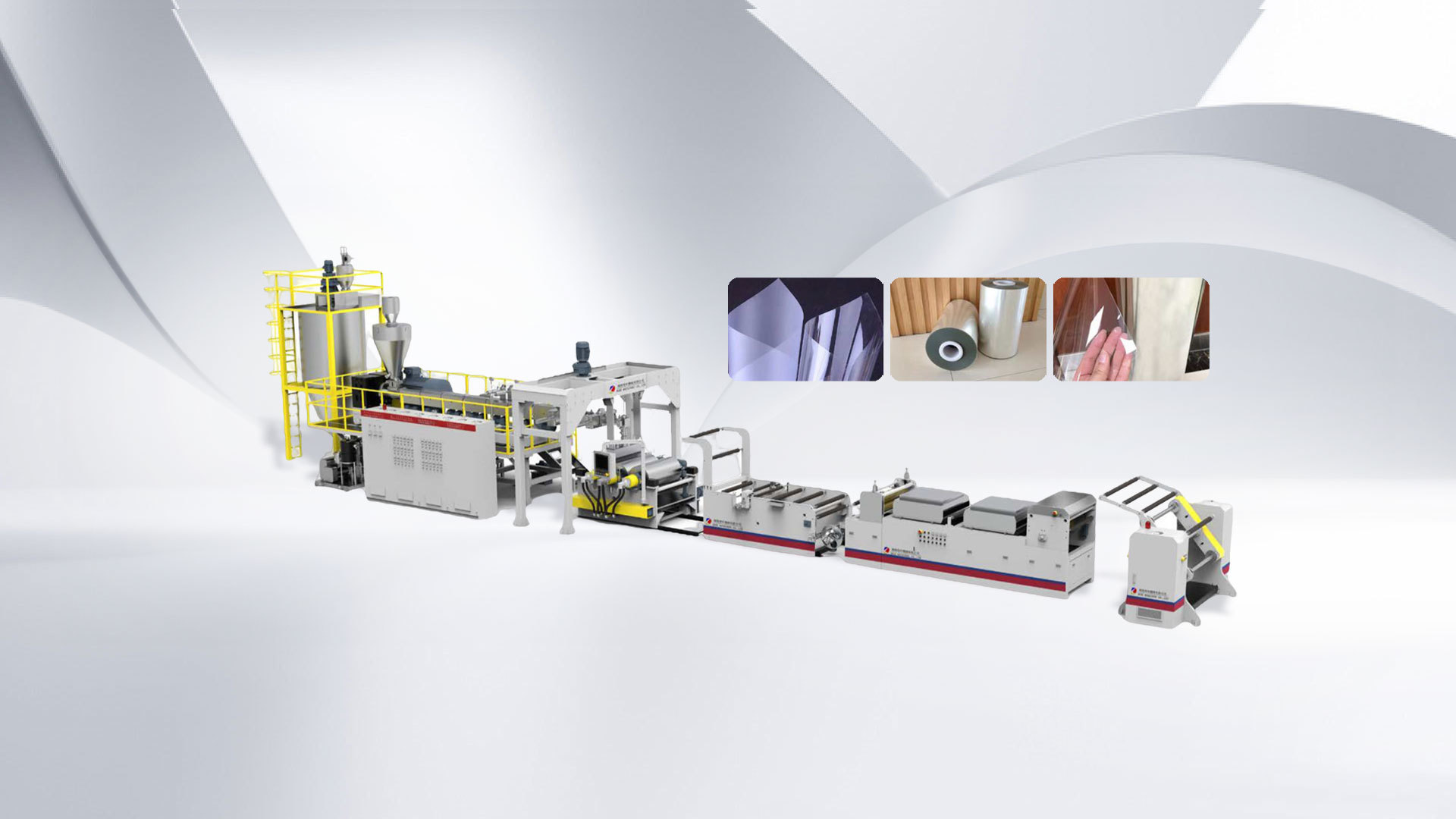
Why Choosing a Twin Screw Compounder Can Transform Your Plastic Manufacturing
Manufacturing in the plastic industry involves intricate processes that require precision, efficiency, and innovation. Among the various technologies available, the twin screw compounder stands out as a transformative solution that can redefine how plastic products are made. This article delves into the numerous advantages of twin screw compounders, their applications, and why investing in this technology can significantly benefit plastic manufacturers.
Table of Contents
- Understanding Twin Screw Compounders
- Advantages of Twin Screw Compounders in Plastic Manufacturing
- Applications of Twin Screw Compounders
- Comparison with Single Screw Extruders
- Key Features to Consider When Choosing a Twin Screw Compounder
- Maintenance and Operating Costs
- The Future of Twin Screw Compounding in Plastic Manufacturing
- Frequently Asked Questions
- Conclusion
Understanding Twin Screw Compounders
Twin screw compounders are advanced machines that consist of two intermeshing screws driven by a common motor. This design enables a high degree of mixing, compounding, and pelletizing of plastics and other materials. The screws rotate in the same direction (co-rotating) or in opposite directions (counter-rotating), allowing for a variety of processing techniques, such as melting, mixing, reacting, and devolatilizing.
The versatility of twin screw compounders makes them suitable for a wide range of applications, from polymer blending to additive incorporation. Their ability to process materials with varying viscosities and thermal sensitivities sets them apart from traditional extruders.
Advantages of Twin Screw Compounders in Plastic Manufacturing
The adoption of twin screw compounders in plastic manufacturing brings several benefits that can enhance productivity and product quality:
1. Superior Mixing Capabilities
The unique design of twin screw compounders allows for exceptional mixing of polymers and additives. This capability results in uniform dispersion, which is critical for achieving consistent product quality.
2. Enhanced Thermal Control
The design of twin screw compounders facilitates precise thermal management, reducing the risk of thermal degradation of materials. This feature ensures that sensitive polymers maintain their integrity during processing.
3. Increased Throughput
With their efficient design, twin screw compounders can handle higher throughputs compared to single screw extruders. This efficiency can lead to increased production rates and reduced lead times, giving manufacturers a competitive edge.
4. Flexibility in Processing
Twin screw compounders offer the flexibility to process a wide range of materials, including engineering plastics, thermoplastics, and even biodegradable polymers. This versatility allows manufacturers to adapt quickly to changing market demands.
5. Improved Material Properties
The intensive mixing and shear forces produced by twin screw compounders can enhance the mechanical and thermal properties of the final product. This improvement can lead to better performance in applications requiring high durability.
Applications of Twin Screw Compounders
Twin screw compounders find applications across various sectors in the plastic manufacturing industry, including:
1. Polymer Blending
The ability to blend different polymers effectively makes twin screw compounders ideal for creating custom compounds that meet specific performance criteria.
2. Additive Masterbatch Production
Twin screw compounders are widely used to produce additive masterbatches, which allow for the incorporation of colorants, UV stabilizers, and other performance-enhancing additives into polymer matrices.
3. Recycling and Reprocessing
These machines play a crucial role in recycling processes, allowing for the efficient reprocessing of post-consumer plastics and reducing waste in the environment.
4. Production of Specialty Compounds
From flame-retardant materials to medical-grade plastics, twin screw compounders are essential for developing specialty compounds that require precise formulations and high consistency.
5. Food and Pharmaceutical Applications
The stringent regulations surrounding food and pharmaceutical products necessitate high-quality manufacturing processes. Twin screw compounders meet these requirements by ensuring uniformity and quality in the final products.
Comparison with Single Screw Extruders
While single screw extruders have long been the industry standard, twin screw compounders offer distinct advantages that make them a preferred choice for many manufacturers:
1. Mixing Efficiency
Single screw extruders typically rely on the flow of material to achieve mixing, which can be less effective than the active mixing provided by twin screw systems. This results in inferior dispersion and inconsistency in the final product.
2. Processing Range
Twin screw compounders accommodate a broader range of materials, including those that require careful handling due to viscosity changes during processing. This versatility is crucial for manufacturers looking to innovate.
3. Design Flexibility
With interchangeable screws and barrel configurations, twin screw compounders can be easily customized to address specific manufacturing needs. This adaptability is often challenging to achieve with traditional single screw extruders.
Key Features to Consider When Choosing a Twin Screw Compounder
Investing in a twin screw compounder involves careful consideration of various features:
1. Screw Configuration
The design and configuration of the screws significantly impact the mixing and processing capabilities. Selecting the right screw type is critical for achieving desired outcomes.
2. Temperature Control Systems
Effective temperature control systems help prevent thermal degradation and maintain the quality of sensitive materials. Investing in advanced temperature regulation is a vital consideration.
3. Automation and Control
Modern twin screw compounders come equipped with sophisticated automation and control systems that allow for precise monitoring and adjustments during the manufacturing process. This feature enhances overall efficiency and reduces operator error.
4. Maintenance Requirements
Understanding the maintenance needs of the machine is essential for optimizing uptime and ensuring long-term reliability. Regular maintenance routines should be factored into the decision-making process.
5. Manufacturer Support
Choosing a reputable manufacturer who provides comprehensive support, including training and service, is crucial for successful operation.
Maintenance and Operating Costs
While twin screw compounders offer numerous advantages, it’s essential to consider their maintenance and operating costs:
1. Maintenance Costs
Regular maintenance is crucial to ensure optimal performance. This can involve periodic inspections, part replacements, and cleaning, which can add to operational expenses.
2. Energy Efficiency
The energy consumption of twin screw compounders can be higher than that of single screw options. However, the increased efficiency and throughput often justify the additional energy costs.
3. Initial Investment
The upfront investment in a twin screw compounder may be higher than that of traditional extruders. However, the long-term benefits, such as increased production and reduced waste, can lead to significant cost savings.
The Future of Twin Screw Compounding in Plastic Manufacturing
The future of plastic manufacturing is poised for transformation, and twin screw compounding technology will play a pivotal role. As sustainability becomes a priority, the ability to efficiently recycle and reprocess materials will be critical. Moreover, advancements in automation and Industry 4.0 technologies will further enhance the capabilities of twin screw compounders, making them more efficient and smarter.
Innovative materials, such as bio-based plastics and composites, are also set to benefit from the precise mixing and compounding capabilities of twin screw systems. As manufacturers strive to meet evolving consumer demands and regulatory standards, twin screw compounders will position themselves as essential tools for future success.
Frequently Asked Questions
1. What is a twin screw compounder?
A twin screw compounder is a type of extruder that features two intermeshing screws, allowing for efficient mixing and processing of polymers and additives.
2. How does a twin screw compounder differ from a single screw extruder?
Twin screw compounders provide superior mixing capabilities, flexibility in processing a wider range of materials, and greater thermal control compared to single screw extruders.
3. What are the main benefits of using a twin screw compounder?
The benefits include superior mixing, enhanced thermal control, increased throughput, flexibility in processing, and improved material properties.
4. Can twin screw compounders be used for recycling plastics?
Yes, twin screw compounders are widely used in recycling processes to efficiently reprocess post-consumer plastics.
5. What should I consider when choosing a twin screw compounder?
Key considerations include screw configuration, temperature control systems, automation features, maintenance requirements, and manufacturer support.
Conclusion
In summary, the adoption of twin screw compounders represents a significant advancement in plastic manufacturing. With their superior mixing capabilities, enhanced thermal control, and versatility, these machines can transform production processes and lead to high-quality, consistent products. By investing in twin screw technology, manufacturers can streamline operations, meet market demands, and position themselves for future success in an ever-evolving industry. Embracing this technology will not only boost efficiency but also pave the way for innovative products that meet the needs of a sustainable future.
Previous Page:
RELATED INFORMATION
Why Choosing a Twin Screw Compounder Can Transform Your Plastic Manufacturing
Why Choosing a Twin Screw Compounder Can Transform Your Plastic Manufacturing Manufacturing in the plastic industry involves intricate processes that require precision, efficiency, and innovation. Among the various technologies available, the twin screw compounder stands out as a transformative solution that can redefine how plastic products are made. This article delves into the numerous advantag
Understanding the Benefits and Functionality of Twin Screw Extrusion Lines
--- Twin screw extrusion lines are a vital component in the realm of plastic processing machinery, specifically designed to enhance the mixing, compounding, and extrusion of various materials. Unlike single screw extruders, twin screw extruders feature two intermeshing screws that rotate within a barrel, facilitating superior blending and material handling. One of the primary advantages of a twin