Why Polycarbonate Sheet Extruders Are Essential for Modern Manufacturing
2025-07
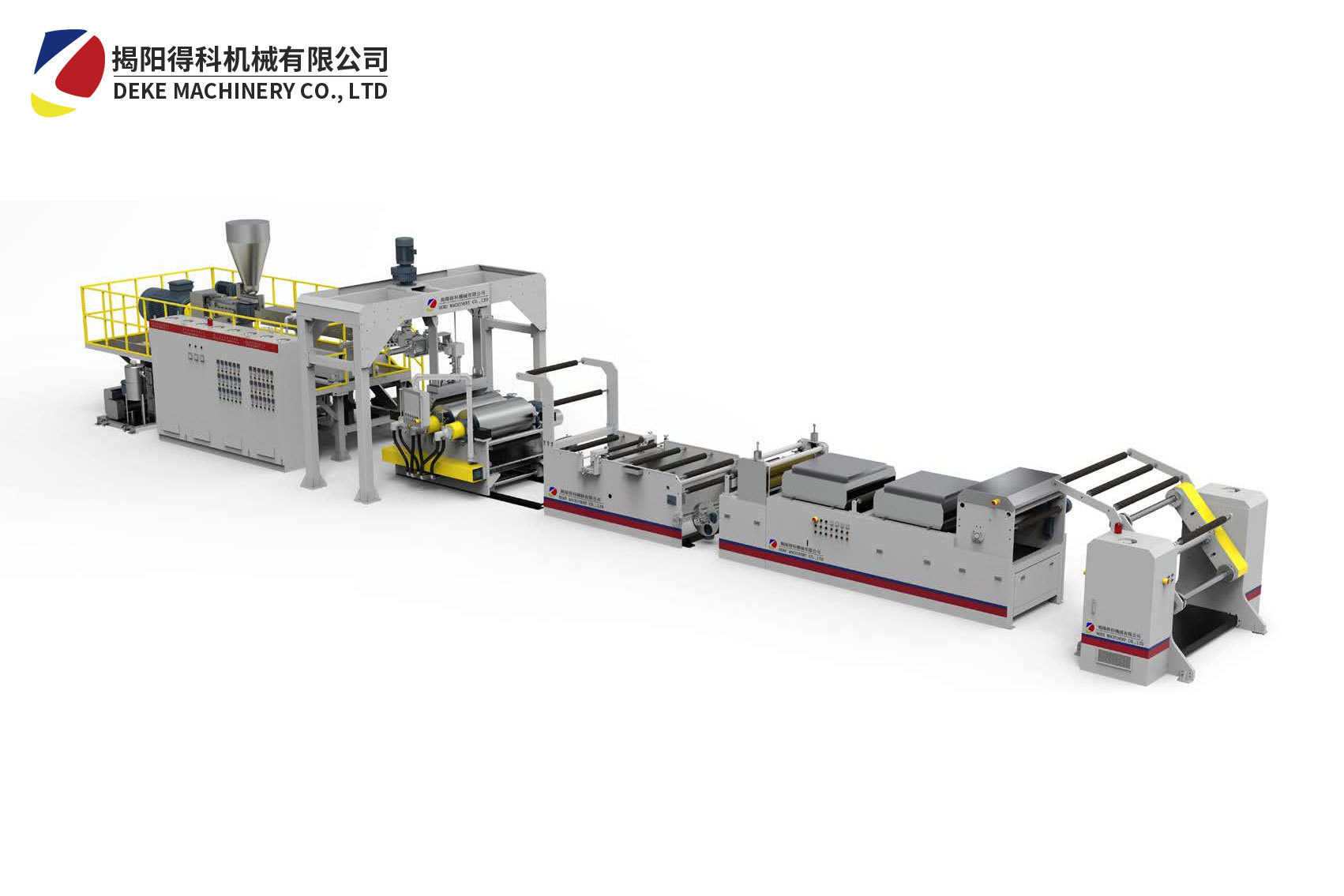
Why Polycarbonate Sheet Extruders Are Essential for Modern Manufacturing
Table of Contents
- 1. Introduction to Polycarbonate Sheet Extruders
- 2. Importance of Polycarbonate in Manufacturing
- 3. How Polycarbonate Sheet Extruders Work
- 4. Advantages of Using Polycarbonate Sheet Extruders
- 5. Diverse Applications of Polycarbonate Sheets
- 6. Polycarbonate vs. Other Plastic Materials
- 7. Maintenance and Optimization of Extruders
- 8. Future Trends in Polycarbonate Extrusion Technology
- 9. FAQs about Polycarbonate Sheet Extruders
- 10. Conclusion: The Indispensable Role of Extruders
1. Introduction to Polycarbonate Sheet Extruders
Polycarbonate sheet extruders are pivotal in the manufacturing landscape, shaping materials essential for various industries. **Polycarbonate**, a thermoplastic polymer known for its exceptional strength and durability, has gained prominence due to its versatile applications, from construction to electronics. The extrusion process allows manufacturers to create sheets of varying thicknesses, widths, and finishes tailored to specific needs. Understanding the intricacies of polycarbonate sheet extruders is key to appreciating their role in modern manufacturing.
2. Importance of Polycarbonate in Manufacturing
Polycarbonate is renowned for its unique properties, including **high impact resistance**, **optical clarity**, and **thermal stability**. These characteristics make polycarbonate sheets ideal for applications requiring robust materials that can withstand harsh environments. Industries such as automotive, construction, and telecommunications rely heavily on polycarbonate for products ranging from safety goggles to roofing sheets. The increasing demand for lightweight yet strong materials has further solidified polycarbonate's position as a preferred choice in manufacturing.
3. How Polycarbonate Sheet Extruders Work
The operation of a polycarbonate sheet extruder involves several stages:
3.1 Material Feeding
The extrusion process begins with feeding polycarbonate pellets into the barrel of the extruder. The machine's precise feeding system ensures a consistent flow of material, essential for maintaining product quality.
3.2 Melting and Mixing
As the pellets move through the heating zones of the extruder, they are gradually melted. The machine's design incorporates mixing elements that ensure uniform temperature distribution and material consistency, resulting in a homogenous melt.
3.3 Shaping
Once melted, the polycarbonate is forced through a die, shaping it into sheets. The choice of die and its configuration directly affect the sheet's thickness and surface finish.
3.4 Cooling and Cutting
After shaping, the sheets are cooled using various methods, such as water baths or air cooling. Once cooled, they are cut into the desired lengths, ready for shipping or further processing.
4. Advantages of Using Polycarbonate Sheet Extruders
Polycarbonate sheet extruders offer numerous advantages that enhance their utility in manufacturing:
4.1 Customization Options
Extrusion allows for the production of customized sheets tailored to specific applications. Manufacturers can adjust thickness, width, and even color during the extrusion process, accommodating diverse client needs.
4.2 Cost-Effectiveness
While the initial investment in extrusion technology can be significant, the long-term benefits often outweigh costs. Extruders enable mass production, reducing the per-unit cost and allowing businesses to remain competitive.
4.3 Environmental Benefits
Polycarbonate is a recyclable material, and advancements in extrusion technology have made it possible to incorporate recycled polycarbonate into the production process, further minimizing environmental impact.
5. Diverse Applications of Polycarbonate Sheets
Polycarbonate sheets find applications across various sectors:
5.1 Construction Industry
In the construction sector, polycarbonate sheets serve as roofing materials, skylights, and protective barriers. Their high impact resistance and UV stability make them ideal for use in environments exposed to the elements.
5.2 Automotive Sector
The automotive industry utilizes polycarbonate for windows, headlights, and dashboards due to its lightweight nature and strength, contributing to fuel efficiency without compromising safety.
5.3 Electronics and Appliances
In electronics, polycarbonate's optical clarity makes it suitable for screens and housings, while its heat resistance ensures durability in appliances.
5.4 Medical Applications
Polycarbonate sheets are also used in medical devices, including incubators and protective shields, where clarity and resilience are paramount.
6. Polycarbonate vs. Other Plastic Materials
When comparing polycarbonate to other plastic materials, several factors stand out:
6.1 Strength and Durability
While materials like acrylic are lighter, polycarbonate significantly outperforms them in terms of impact resistance and durability, making it the preferred choice for applications requiring robust materials.
6.2 Temperature Resistance
Polycarbonate can withstand higher temperatures than many other plastics, offering an advantage in environments where thermal stability is critical.
6.3 Cost Considerations
Though polycarbonate may be more expensive to produce than some alternatives, its longevity and performance often justify the investment, proving to be cost-effective over time.
7. Maintenance and Optimization of Extruders
Proper maintenance of polycarbonate sheet extruders is vital for ensuring operational efficiency and product quality.
7.1 Regular Cleaning
Establishing a routine cleaning schedule helps prevent material build-up, which can lead to inconsistent product quality and machine performance issues.
7.2 Monitoring Temperature Settings
Maintaining appropriate temperature settings during the extrusion process ensures a uniform melt and reduces the risk of defects in the final product.
7.3 Inspection of Mechanical Components
Regular inspections of mechanical components, such as screws and barrels, can identify potential wear and tear, allowing for timely replacements and minimizing downtime.
8. Future Trends in Polycarbonate Extrusion Technology
As technology evolves, several trends are emerging in the field of polycarbonate sheet extrusion:
8.1 Automation and Smart Manufacturing
The integration of automation and IoT technology is set to revolutionize the manufacturing landscape, enhancing efficiency and product quality through real-time monitoring and data analysis.
8.2 Advanced Material Formulation
Research into new formulations of polycarbonate is underway, aiming to enhance attributes such as UV resistance and fire retardancy, thereby broadening its application range.
8.3 Sustainable Practices
A growing emphasis on sustainability is driving the development of eco-friendly extrusion processes and materials, reflecting the industry's shift towards greener manufacturing practices.
9. FAQs about Polycarbonate Sheet Extruders
1. What types of products can be made using polycarbonate sheet extruders?
Polycarbonate sheet extruders can create a wide range of products, including roofing sheets, safety goggles, signage, and electronic housings.
2. How does the extrusion process impact the quality of polycarbonate sheets?
The extrusion process allows for precise control over material flow and temperature, ensuring uniformity and high-quality output.
3. Are polycarbonate sheets suitable for outdoor use?
Yes, polycarbonate sheets are highly UV resistant and can withstand various weather conditions, making them suitable for outdoor applications.
4. What maintenance is required for polycarbonate sheet extruders?
Regular cleaning, temperature monitoring, and mechanical inspections are essential for maintaining optimal performance and product quality.
5. How does polycarbonate compare to glass?
Polycarbonate is significantly lighter, shatter-resistant, and has better insulation properties compared to glass, making it a preferred choice in many applications.
10. Conclusion: The Indispensable Role of Extruders
In conclusion, polycarbonate sheet extruders play a critical role in modern manufacturing, offering unique advantages that cater to diverse industrial needs. The exceptional properties of polycarbonate, combined with the efficiency of extrusion technology, position these machines as indispensable tools in the production of lightweight, durable, and high-performance materials. As industries continue to evolve and demand innovative solutions, the importance of polycarbonate sheet extruders will undoubtedly grow, paving the way for a more resilient and sustainable manufacturing future.
RELATED INFORMATION
Understanding the Benefits and Functionality of Twin Screw Extrusion Lines
--- Twin screw extrusion lines are a vital component in the realm of plastic processing machinery, specifically designed to enhance the mixing, compounding, and extrusion of various materials. Unlike single screw extruders, twin screw extruders feature two intermeshing screws that rotate within a barrel, facilitating superior blending and material handling. One of the primary advantages of a twin
Why Polycarbonate Sheet Extruders Are Essential for Modern Manufacturing
Why Polycarbonate Sheet Extruders Are Essential for Modern Manufacturing Table of Contents 1. Introduction to Polycarbonate Sheet Extruders 2. Importance of Polycarbonate in Manufacturing 3. How Polycarbonate Sheet Extruders Work 4. Advantages of Using Polycarbonate Sheet Extruders 5. Diverse Applications of Polycarbonate Sheets 6. Polycarbonate vs. Other Plastic Materials 7. Ma