Maximizing Performance with EVOH High Barrier Sheet Extruders
2025-07
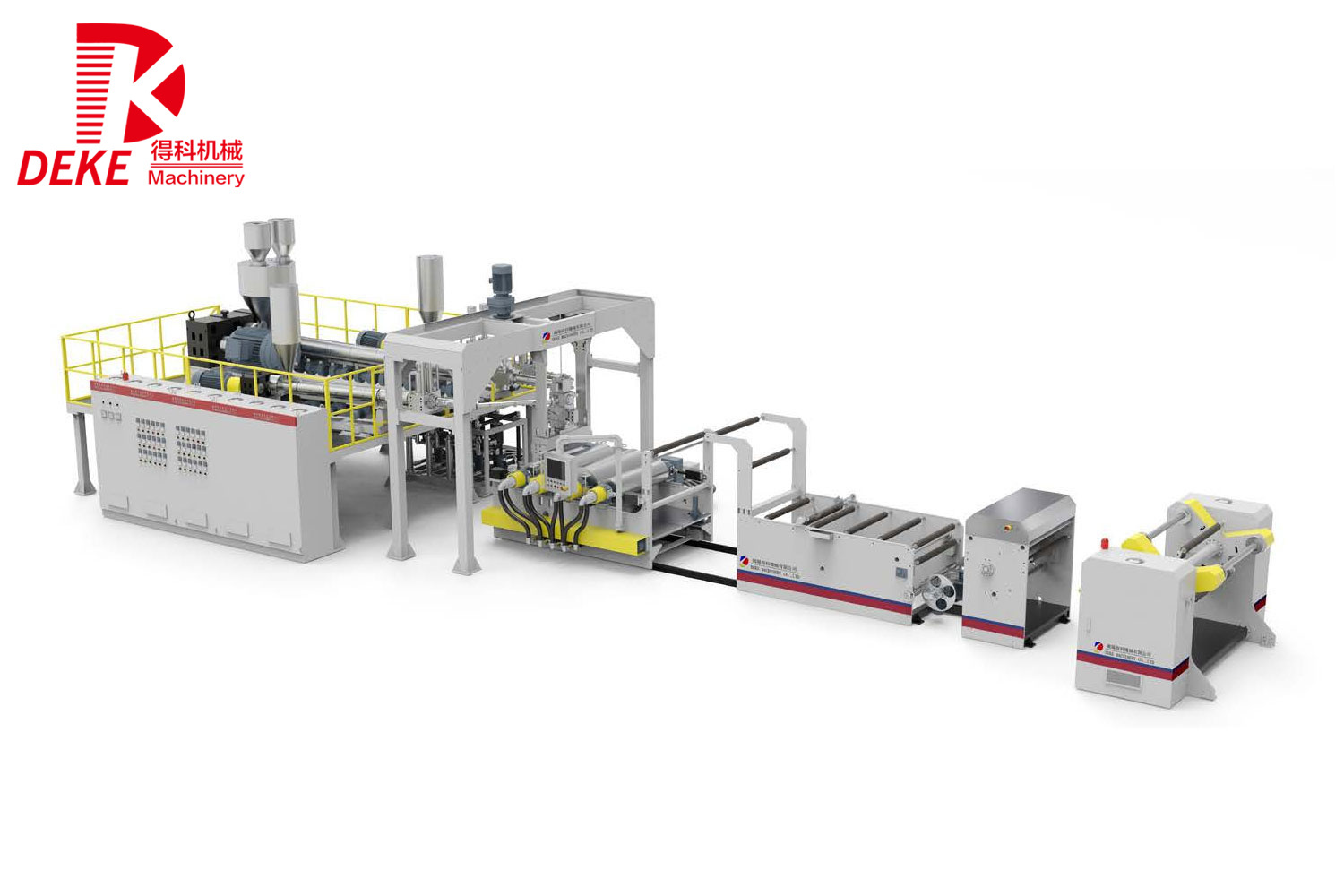
One of the core functionalities of the EVOH high barrier sheet extruder is its ability to produce multi-layer structures. By integrating EVOH into a multi-layer sheet, manufacturers can achieve enhanced barrier properties that protect sensitive products such as food, pharmaceuticals, and electronics from environmental factors. This multi-layer approach not only enhances product shelf life but also contributes to sustainability by reducing material usage without compromising performance.
The process of extruding EVOH requires precise temperature control and screw design. The extruder operates through a combination of melting and mixing processes, where specific temperature zones are maintained to ensure the EVOH is adequately melted while preserving its unique properties. An efficient screw design can significantly enhance the mixing of EVOH with other polymers, leading to a homogeneous melt that results in high-quality sheets.
Moreover, the throughput and energy efficiency of EVOH high barrier sheet extruders play a vital role in manufacturing operations. Advanced models are often equipped with features such as high-efficiency motors, precise temperature control systems, and optimized die designs. These features facilitate faster production speeds and reduce energy consumption, making the manufacturing process not only more cost-effective but also environmentally friendly.
Another important aspect of EVOH high barrier sheet extruders is their adaptability to various applications. They can be tailored to produce sheets of different thicknesses, widths, and barrier properties, catering to diverse industry needs. This versatility allows manufacturers to innovate and develop new products that meet market demands while maintaining quality and performance standards.
Maintenance and operational best practices are crucial for the longevity and efficiency of these extruders. Regular cleaning, monitoring of wear parts, and adherence to operational guidelines can prevent downtime and ensure consistent production quality. Training operators to understand the intricacies of handling EVOH materials can further enhance operational efficiency and product output.
In conclusion, EVOH high barrier sheet extruders are vital in producing high-performance barrier materials that meet the rigorous demands of modern packaging applications. Their advanced technology, coupled with operational efficiencies, positions them as indispensable assets in the plastic processing machinery sector, driving innovation and sustainability in manufacturing. By investing in these advanced extruders, companies can enhance their product offerings and maintain a competitive edge in the market.
RELATED INFORMATION
Understanding PET Sheet Extruder Machines: A Comprehensive Guide
PET sheet extruder machines are specialized equipment used in the plastic processing industry to produce sheets made from polyethylene terephthalate (PET). These machines play a crucial role in various applications, including packaging, automotive parts, and consumer goods. Understanding how these machines work, their components, and their applications can help manufacturers improve efficiency and
Exploring the Efficiency of PET Single Screw Extruders in Manufacturing
Exploring the Efficiency of PET Single Screw Extruders in Manufacturing Table of Contents 1. Introduction to PET Single Screw Extruders 2. The Importance of PET in the Manufacturing Process 3. Design and Mechanism of Single Screw Extruders 4. Efficiency Factors of PET Single Screw Extruders 5. Applications of PET Single Screw Extruders in Manufacturing 6. Maintenance and O