Unlocking the Benefits of HDPE Sheet Extrusion in Modern Manufacturing
2025-06
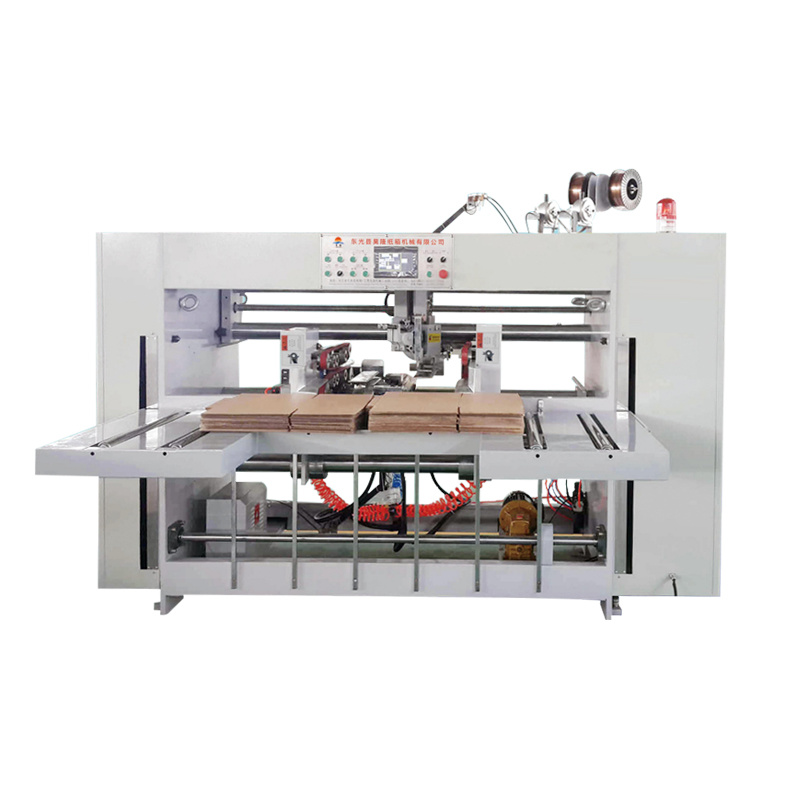
Unlocking the Benefits of HDPE Sheet Extrusion in Modern Manufacturing
Table of Contents
- Introduction to HDPE Sheet Extrusion
- What is HDPE and Its Properties?
- Understanding the HDPE Extrusion Process
- Advantages of HDPE Sheet Extrusion in Manufacturing
- Applications of HDPE Sheets Across Industries
- Sustainability and Environmental Impact of HDPE
- The Future of HDPE Sheet Extrusion
- Conclusion
- Frequently Asked Questions
Introduction to HDPE Sheet Extrusion
In the modern manufacturing landscape, materials play a crucial role in determining product efficiency and sustainability. **High-Density Polyethylene (HDPE)** has emerged as a game-changer in various sectors due to its versatility and robust properties. **HDPE sheet extrusion** is a prominent manufacturing process that allows creating durable sheets tailored for diverse applications. By harnessing the advantages of HDPE sheets, manufacturers can significantly enhance their production capabilities and environmental footprint.
What is HDPE and Its Properties?
HDPE, or High-Density Polyethylene, is a thermoplastic polymer made from petroleum. Characterized by its high strength-to-density ratio, HDPE exhibits outstanding resistance to impact, chemicals, and UV radiation. It is lightweight, making it easy to handle and transport, while its rigidity provides structural integrity in various applications.
The Key Properties of HDPE Include:
- Durability: HDPE sheets are resistant to wear and tear, making them ideal for demanding environments.
- Chemical Resistance: They can withstand exposure to a wide range of chemicals without degrading.
- Moisture Resistance: HDPE does not absorb water, preventing mold and mildew growth.
- Recyclability: HDPE is 100% recyclable, contributing to sustainable manufacturing practices.
Understanding the HDPE Extrusion Process
The HDPE extrusion process involves melting plastic pellets and forcing them through a die to form continuous sheets. This process allows for precise control of thickness, width, and overall quality. The steps involved in the HDPE sheet extrusion process include:
1. Material Preparation
HDPE pellets are fed into a hopper and dried to remove any moisture, ensuring a quality output.
2. Melting
The material is heated to its melting point using a series of heaters in the extruder.
3. Extrusion
The molten HDPE is forced through a die to create sheets of desired dimensions.
4. Cooling
The newly formed sheets are cooled using air or water to solidify them.
5. Cutting and Finishing
Finally, the sheets are cut to specified sizes and undergo any necessary finishing processes, such as sanding or surface treatment.
Advantages of HDPE Sheet Extrusion in Manufacturing
HDPE sheet extrusion offers numerous benefits that enhance manufacturing efficiency and product quality. Below are some of the key advantages:
1. Cost-Effective Production
HDPE extrusion allows for high-volume production, which significantly lowers the cost per unit. The process minimizes material waste, contributing to overall financial efficiency.
2. Customization Options
Manufacturers can easily customize the dimensions, thickness, and colors of HDPE sheets, enabling tailored solutions for specific applications.
3. Enhanced Strength and Durability
The resulting sheets are strong and resistant to impact and environmental factors, making them suitable for use in harsh conditions.
4. Lightweight Yet Sturdy
HDPE sheets are lightweight, which simplifies transportation and installation without compromising on strength.
5. Easy to Fabricate and Install
HDPE sheets can be easily cut, welded, or fabricated into various shapes, providing versatility in design and application.
Applications of HDPE Sheets Across Industries
The versatility of HDPE sheets leads to their widespread use across multiple industries, including:
1. Construction Industry
HDPE sheets serve as reliable materials for insulation, vapor barriers, and protective sheeting in construction projects. Their durability ensures long-lasting performance against the elements.
2. Packaging Solutions
In the packaging industry, HDPE is used for creating durable containers, bottles, and packaging films due to its chemical resistance and lightweight properties.
3. Agriculture
In agriculture, HDPE sheets are utilized for liners, tarps, and containment solutions, aiding in water management and soil protection.
4. Automotive Sector
HDPE sheets find applications in automotive components, particularly in interior parts where lightweight materials are essential.
5. Food Processing
The food industry benefits from HDPE sheets, which are used in manufacturing various food packaging solutions due to their safety and resistance to contaminants.
Sustainability and Environmental Impact of HDPE
With increasing global emphasis on sustainability, HDPE stands out due to its recyclability and low environmental impact. The following aspects highlight the sustainable nature of HDPE:
1. Recyclability
HDPE can be recycled multiple times without significant loss of quality, making it an eco-friendly choice for manufacturers.
2. Reduced Carbon Footprint
The efficient production process of HDPE sheets helps to minimize energy consumption and emissions, contributing to a reduced carbon footprint.
3. Long Lifespan
The durability of HDPE sheets means they do not require frequent replacement, reducing waste and resource consumption over time.
4. Non-Toxic Material
HDPE is classified as a non-toxic material, ensuring safety for both human health and the environment.
The Future of HDPE Sheet Extrusion
As technology advances, the future of HDPE sheet extrusion looks promising. Innovations in extrusion technology are leading to enhanced efficiency, reduced waste, and improved product quality. The integration of automation and real-time monitoring in production processes is expected to further streamline operations.
Moreover, as industries strive for greater sustainability, the demand for HDPE sheets is likely to increase, paving the way for new applications and products. The growing emphasis on eco-friendly materials positions HDPE as a front-runner in the shift toward sustainable manufacturing practices.
Conclusion
In summary, **HDPE sheet extrusion** is a pivotal process in modern manufacturing, offering numerous benefits such as cost-effectiveness, customization, and sustainability. Its wide range of applications across various industries highlights its versatility and importance in contemporary production methods. Embracing HDPE sheet extrusion not only enhances manufacturing efficiency but also contributes to a more sustainable future.
Frequently Asked Questions
1. What are the main benefits of using HDPE sheets?
HDPE sheets offer advantages such as durability, chemical resistance, lightweight properties, and recyclability, making them suitable for various applications.
2. Can HDPE sheets be customized?
Yes, HDPE sheets can be easily customized in terms of thickness, dimensions, and color, allowing for tailored solutions to meet specific needs.
3. How is the HDPE extrusion process carried out?
The process involves melting HDPE pellets, extruding them through a die to form sheets, followed by cooling and cutting to the desired sizes.
4. Are HDPE sheets environmentally friendly?
Yes, HDPE sheets are recyclable, have a low carbon footprint, and are made from non-toxic materials, contributing to sustainable manufacturing practices.
5. What industries commonly use HDPE sheets?
HDPE sheets are widely used in industries such as construction, packaging, agriculture, automotive, and food processing, showcasing their versatility and utility.
RELATED INFORMATION
Understanding PET Sheet Extruder Machines: A Comprehensive Guide
PET sheet extruder machines are specialized equipment used in the plastic processing industry to produce sheets made from polyethylene terephthalate (PET). These machines play a crucial role in various applications, including packaging, automotive parts, and consumer goods. Understanding how these machines work, their components, and their applications can help manufacturers improve efficiency and
Exploring the Efficiency of PET Single Screw Extruders in Manufacturing
Exploring the Efficiency of PET Single Screw Extruders in Manufacturing Table of Contents 1. Introduction to PET Single Screw Extruders 2. The Importance of PET in the Manufacturing Process 3. Design and Mechanism of Single Screw Extruders 4. Efficiency Factors of PET Single Screw Extruders 5. Applications of PET Single Screw Extruders in Manufacturing 6. Maintenance and O