Understanding Micro Twin Screw Extruders: The Future of Plastic Processing
2025-04
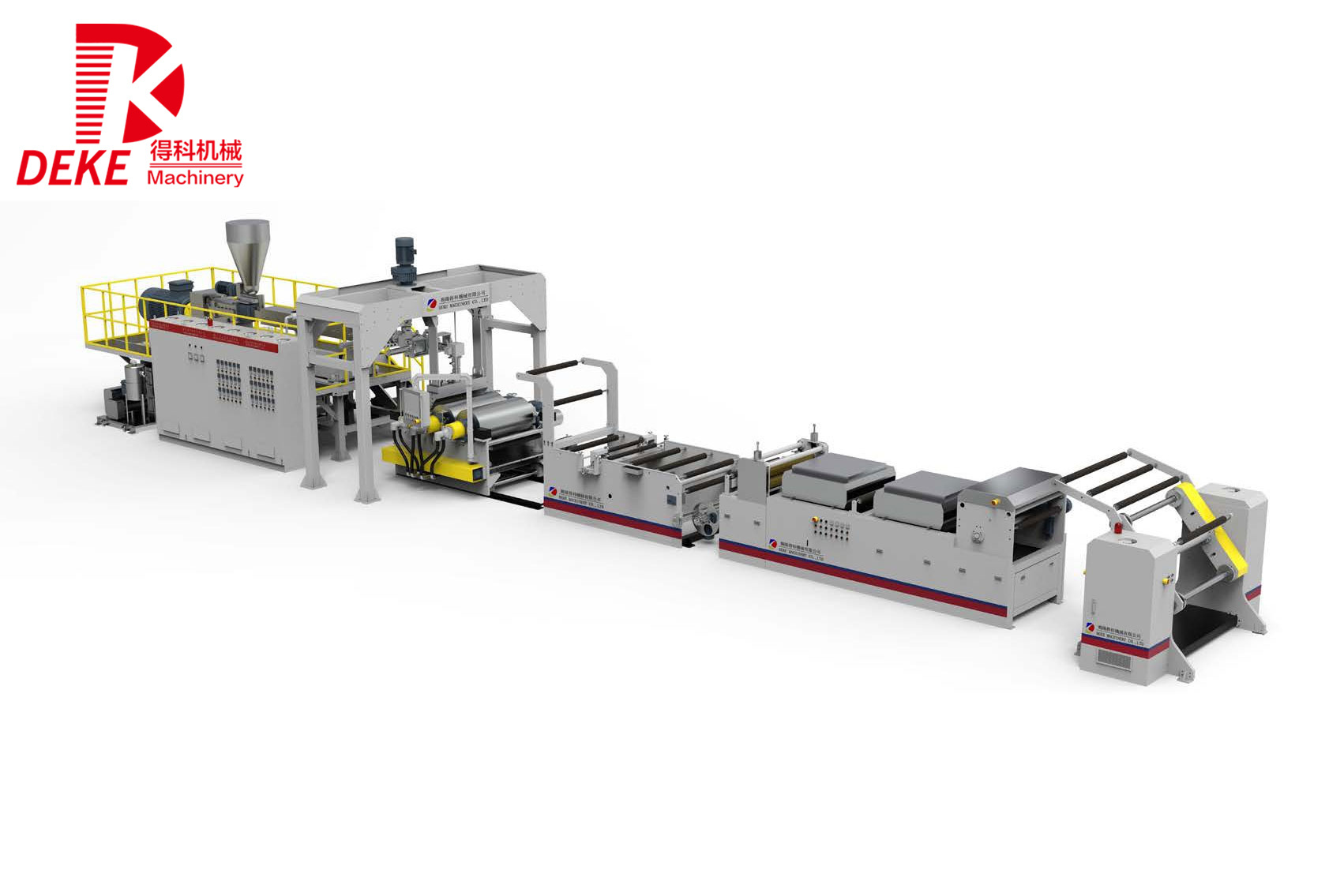
One of the primary advantages of micro twin screw extruders is their ability to process small batch sizes with high precision. This capability is particularly beneficial for industries that require specialized formulations or innovative materials, such as bioplastics or composite materials. The micro scale allows for experimentation and development of new products with minimal resource investment, facilitating rapid prototyping and innovation.
The operation of a micro twin screw extruder involves feeding raw materials into the hopper, where they are then conveyed into the screw channel. As the screws rotate, they transport the materials along the length of the extruder while simultaneously mixing and melting them. The design of the screws can be customized to suit specific processing needs, allowing for a wide range of materials to be processed efficiently. This versatility makes micro twin screw extruders suitable for various applications, from compounding and pelletizing to reactive extrusion and blending.
Moreover, micro twin screw extruders are equipped with advanced control systems that enable precise temperature and torque management. This level of control is essential for achieving consistent product quality, especially in applications where material characteristics such as viscosity and melt flow rate are critical. The integration of sensors and automation further enhances the operational efficiency of these machines, reducing downtime and increasing productivity.
In addition to their technical advantages, micro twin screw extruders are also more environmentally friendly compared to traditional extruding methods. Their efficient design minimizes material waste and energy consumption, aligning with the growing emphasis on sustainability in manufacturing practices. As industries continue to pursue greener alternatives, the adoption of micro twin screw extruders is likely to increase.
In summary, micro twin screw extruders are revolutionizing the plastic processing industry by providing enhanced precision, flexibility, and sustainability. Their ability to cater to specialized applications and produce high-quality materials positions them as a vital tool for manufacturers looking to innovate and stay competitive in a rapidly evolving market. As this technology continues to advance, it will likely play a crucial role in shaping the future of plastic processing.
Next page:
RELATED INFORMATION
Understanding the Benefits and Applications of Parallel Twin Screw Extruders
In the realm of plastic processing machinery, the parallel twin screw extruder stands out as a versatile and effective solution for a variety of applications. This type of extruder is characterized by two screws that run parallel to each other, allowing for efficient melting, mixing, and compounding of materials. The design of the parallel twin screw extruder enables a uniform and consistent outpu
Innovative Applications of Parallel Twin Screw Extruder Technology in Modern Manufacturing
Innovative Applications of Parallel Twin Screw Extruder Technology Introduction to Parallel Twin Screw Extruders The **parallel twin screw extruder** has emerged as a pivotal technology in the realm of manufacturing, particularly within the plastic processing sector. Characterized by two intermeshing screws rotating in the same direction, these extruders are designed to efficiently mix, melt, and