Understanding the Benefits and Functionality of Parallel Twin Screw Extruders
2025-01
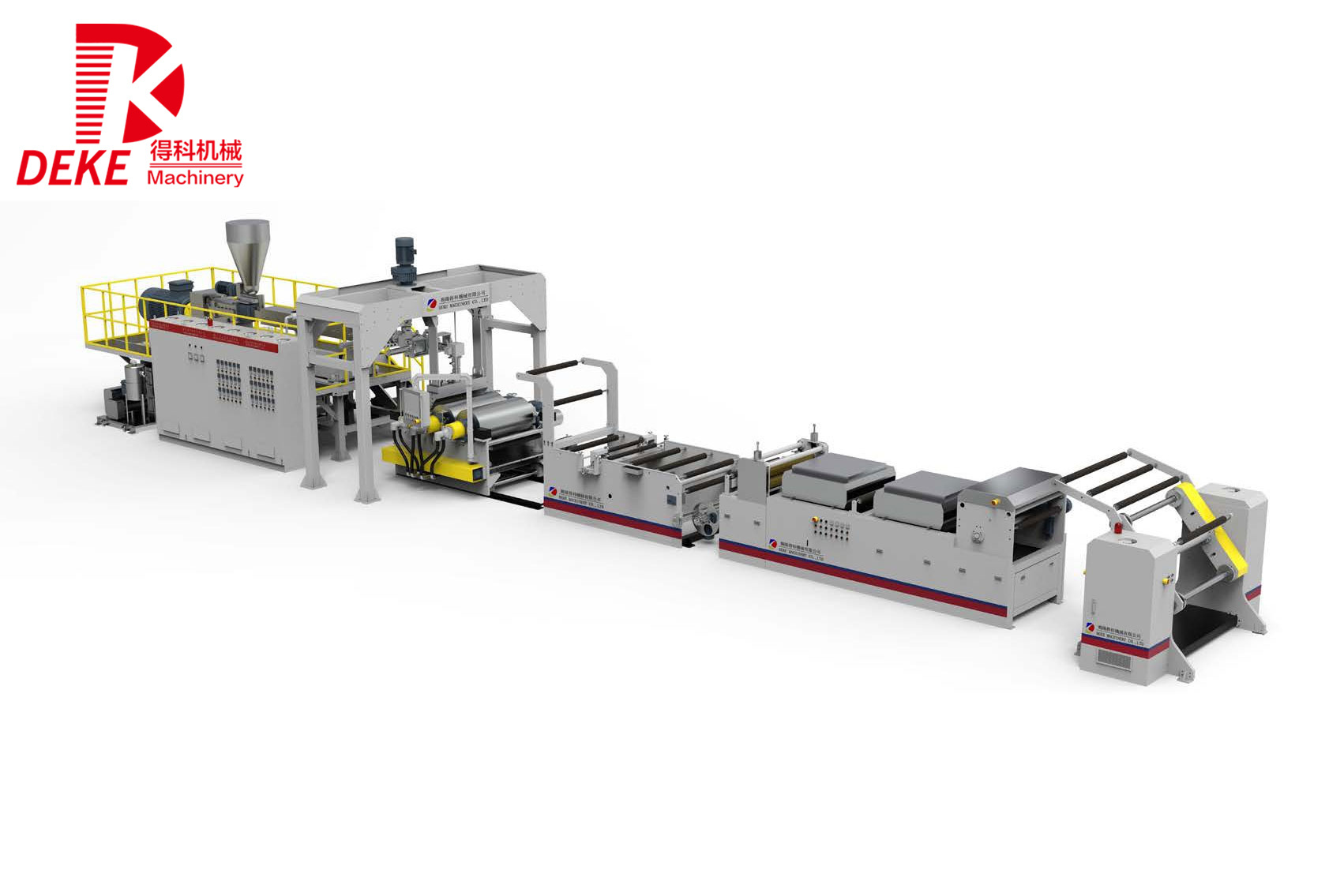
One of the primary advantages of parallel twin screw extruders is their ability to handle materials with varying viscosities. The intermeshing design of the screws enables better material movement and distribution, which is crucial for achieving uniformity in the final product. This feature is particularly beneficial when working with complex formulations that require precise mixing of additives, fillers, and other components.
In addition to their mixing capabilities, parallel twin screw extruders are highly adaptable. They can be equipped with interchangeable elements such as different screw configurations, barrel designs, and temperature control systems. This flexibility allows manufacturers to customize the extruder for specific applications, whether it be producing plastics, rubber, or even food products. Thus, investing in a parallel twin screw extruder can lead to significant improvements in operational efficiency and product versatility.
Moreover, parallel twin screw extruders excel in processing thermoplastics and thermosetting materials. Their design facilitates effective melting and homogenization, which are crucial for producing high-quality end products. The ability to process a wide range of materials also means that manufacturers can diversify their product lines without needing multiple specialized machines.
Another notable benefit of parallel twin screw extruders is their capability for continuous processing. This allows for uninterrupted production runs, which can significantly reduce manufacturing costs and increase throughput. By minimizing downtime associated with batch processing, manufacturers can achieve greater productivity and streamline their operations.
Furthermore, the gentle handling of materials reduces the risk of thermal degradation, making parallel twin screw extruders suitable for sensitive materials that require careful processing. This is particularly important in applications where maintaining the integrity of the material properties is essential.
In conclusion, parallel twin screw extruders represent a vital technology in the realm of plastic processing machinery. Their unique design and versatile applications offer numerous benefits, making them an invaluable asset for manufacturers aiming to enhance their production capabilities. Whether you are looking to improve mixing efficiency, expand your product range, or increase overall productivity, understanding the functionalities of parallel twin screw extruders can provide you with valuable insights into optimizing your manufacturing processes.
Previous Page:
RELATED INFORMATION
Maximizing Output with Twin Screw Roller Head Extruder Settings: A Comprehensive Guide
Maximizing Output with Twin Screw Roller Head Extruder Settings Introduction to Twin Screw Roller Head Extruders In the world of plastic processing machinery, **twin screw roller head extruders** stand out for their versatility and efficiency. These machines are designed to handle various materials, making them indispensable in the manufacturing sector. Understanding how to optimize their settings
Understanding the Benefits and Functionality of Parallel Twin Screw Extruders
Parallel twin screw extruders are specialized machines widely used in the plastic processing industry. As the name suggests, these extruders feature two parallel screws that rotate synchronously within a barrel, providing a unique method of material handling and processing. This design allows for enhanced mixing, compounding, and extrusion of a variety of materials, making them an essential tool f