Exploring the Mechanisms Behind Parallel Twin Screw Extruders: A Comprehensive Guide
2025-01
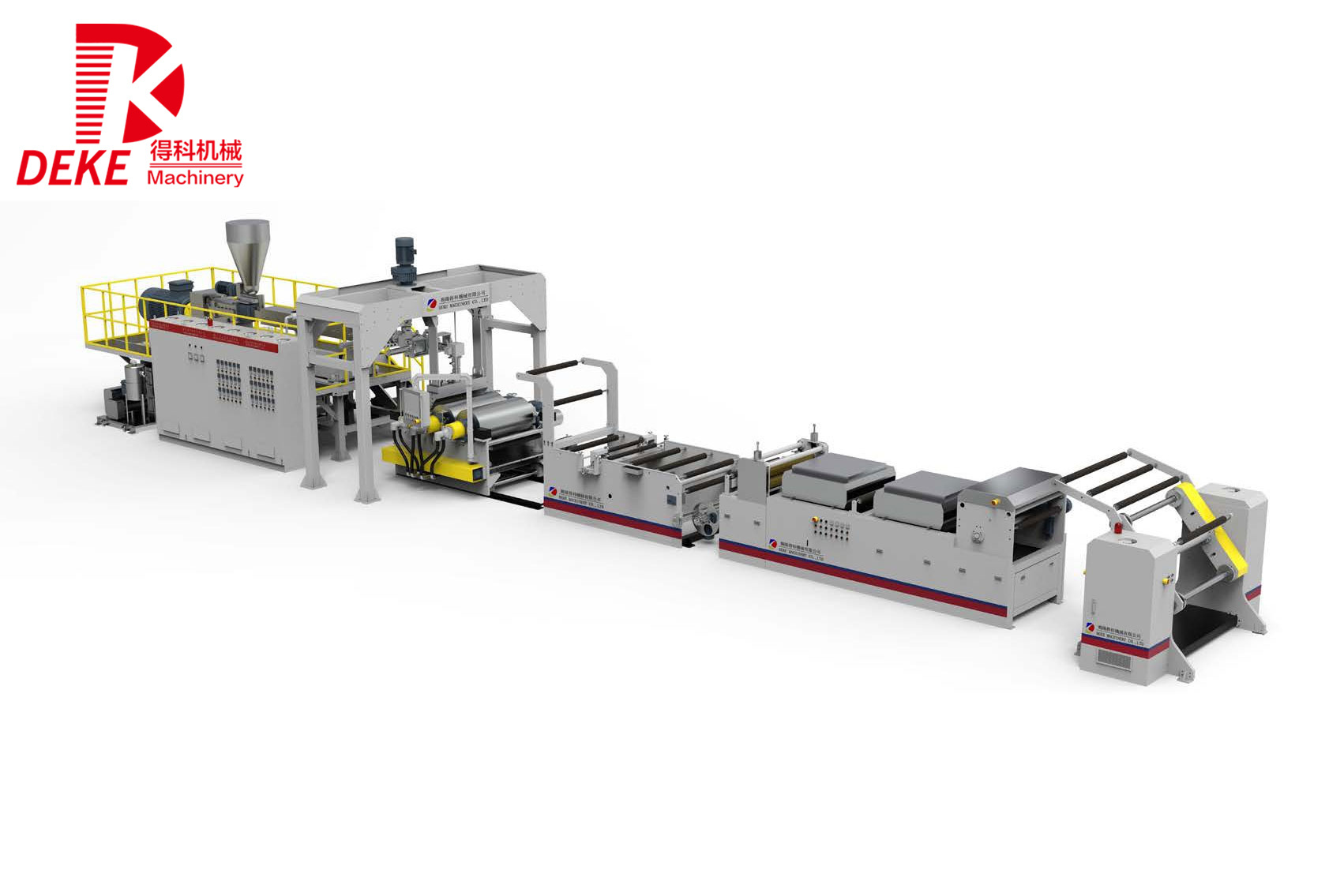
Exploring the Mechanisms Behind Parallel Twin Screw Extruders
Table of Contents
- Introduction to Parallel Twin Screw Extruders
- Understanding the Structure of Parallel Twin Screw Extruders
- Mechanical Principles of Extrusion
- Advantages of Parallel Twin Screw Extruders
- Applications in the Plastic Processing Industry
- Common Challenges and Solutions
- Maintenance and Optimization of Extruders
- Future Trends in Extrusion Technology
- Conclusion
- FAQs
Introduction to Parallel Twin Screw Extruders
Parallel twin screw extruders play a crucial role in the manufacturing and processing of plastics. Their design allows for efficient melting, mixing, and shaping of plastic materials, making them indispensable in various industries. In this article, we will delve into the intricate mechanisms that underlie their functionality, exploring each aspect in detail to provide a comprehensive understanding of these powerful machines.
Understanding the Structure of Parallel Twin Screw Extruders
The structural design of parallel twin screw extruders is fundamental to their performance. Typically, these machines consist of two co-rotating screws mounted parallel to each other within a heated barrel. This unique configuration allows for a variety of material handling capabilities.
The Screws: Design and Function
The screws are the heart of the extruder, designed with specific geometries to enhance material flow and mixing. The pitch, diameter, and length of the screws can vary significantly based on the intended application. Each screw can have various elements such as conveying sections, kneading blocks, and mixing sections, contributing to their versatility.
The Barrel: Heating and Cooling Mechanisms
The barrel provides the necessary environment for the plastic material to melt and be processed. It is equipped with heating zones that regulate temperature along its length. Some extruders also feature cooling zones to control the viscosity of materials during processing.
Mechanical Principles of Extrusion
Understanding the mechanical principles that govern extrusion is vital for optimizing performance.
Shear and Heat Generation
As the screws rotate, they create shear forces that help to melt the plastic granules. This process generates heat through friction, which is critical for achieving the desired melt viscosity.
Material Conveyance
The design of the screws facilitates efficient material conveyance. The co-rotation of the screws pushes the material through the barrel, while the various screw elements ensure thorough mixing and homogenization.
Advantages of Parallel Twin Screw Extruders
Parallel twin screw extruders offer numerous advantages over other types of extrusion machines.
Enhanced Mixing Capabilities
The co-rotating screws provide superior mixing capabilities, allowing for the blending of different materials or additives uniformly. This is particularly advantageous in producing complex materials with specific properties.
Higher Throughput Rates
The design of parallel twin screw extruders enables higher throughput rates, making them ideal for large-scale production. They can process a wide range of materials, from standard thermoplastics to high-performance polymers.
Applications in the Plastic Processing Industry
Parallel twin screw extruders find applications across various sectors, including:
Compounding
Compounding involves mixing polymers with additives to enhance their properties. Parallel twin screw extruders excel in this application due to their exceptional mixing capabilities.
Film and Sheet Production
These extruders are widely used in producing films and sheets, where uniform thickness and material properties are essential.
Injection Molding and Blow Molding
The materials produced using parallel twin screw extruders are often fed into injection and blow molding machines, making them a critical component of the manufacturing process.
Common Challenges and Solutions
While parallel twin screw extruders are highly efficient, they are not without challenges.
Material Degradation
One common issue is material degradation due to excessive heat or shear. To mitigate this, operators must carefully monitor temperature and screw speed.
Wear and Tear of Components
The components of parallel twin screw extruders can experience wear over time. Regular maintenance and timely replacement of worn parts are vital to ensure longevity.
Maintenance and Optimization of Extruders
Regular maintenance is essential for maximizing the performance of parallel twin screw extruders.
Routine Inspections
Conduct routine inspections to identify any potential issues before they become significant problems. This includes checking for wear on screws and barrels.
Calibration and Monitoring
Implementing advanced monitoring systems can provide real-time data on the extruder’s performance, enabling operators to make informed adjustments.
Future Trends in Extrusion Technology
As technology advances, so does the field of extrusion.
Smart Manufacturing
The adoption of smart manufacturing technologies, including IoT and AI, is set to revolutionize the operation of parallel twin screw extruders. These technologies can enhance efficiency and reduce downtime.
Sustainability Practices
The industry is leaning towards more sustainable practices, including the use of recycled materials and energy-efficient processes, making parallel twin screw extruders a focal point in sustainable manufacturing.
Conclusion
Parallel twin screw extruders are indispensable in the plastic processing industry, offering numerous advantages in terms of efficiency, versatility, and product quality. Understanding their mechanisms and the challenges associated with their operation is crucial for optimizing their use in manufacturing. As technology continues to evolve, the future of parallel twin screw extrusion looks promising, paving the way for innovative applications and sustainable practices.
FAQs
1. What materials can be processed using parallel twin screw extruders?
Parallel twin screw extruders can process a wide range of materials, including thermoplastics, elastomers, and composites, making them versatile for various applications.
2. How do I maintain a parallel twin screw extruder?
Regular maintenance involves routine inspections, monitoring screw and barrel wear, calibrating performance settings, and replacing worn components as necessary.
3. What are the advantages of co-rotating screws over counter-rotating screws?
Co-rotating screws provide better mixing and material distribution, leading to improved product quality, whereas counter-rotating screws are better suited for certain applications requiring less shear.
4. Can parallel twin screw extruders be used for recycling plastics?
Yes, parallel twin screw extruders are often used in recycling processes to melt and reform recycled plastics into usable materials.
5. What is the typical throughput rate for parallel twin screw extruders?
Throughput rates can vary based on the specific model and application, but they generally range from hundreds of kilograms to several tons per hour, depending on the material and process requirements.
RELATED INFORMATION
Maximizing Output with Twin Screw Roller Head Extruder Settings: A Comprehensive Guide
Maximizing Output with Twin Screw Roller Head Extruder Settings Introduction to Twin Screw Roller Head Extruders In the world of plastic processing machinery, **twin screw roller head extruders** stand out for their versatility and efficiency. These machines are designed to handle various materials, making them indispensable in the manufacturing sector. Understanding how to optimize their settings
Understanding the Benefits and Functionality of Parallel Twin Screw Extruders
Parallel twin screw extruders are specialized machines widely used in the plastic processing industry. As the name suggests, these extruders feature two parallel screws that rotate synchronously within a barrel, providing a unique method of material handling and processing. This design allows for enhanced mixing, compounding, and extrusion of a variety of materials, making them an essential tool f