Unveiling the Critical Role of EVOH in High Barrier Sheet Extrusion: Enhancing Performance and Sustainability
2024-12
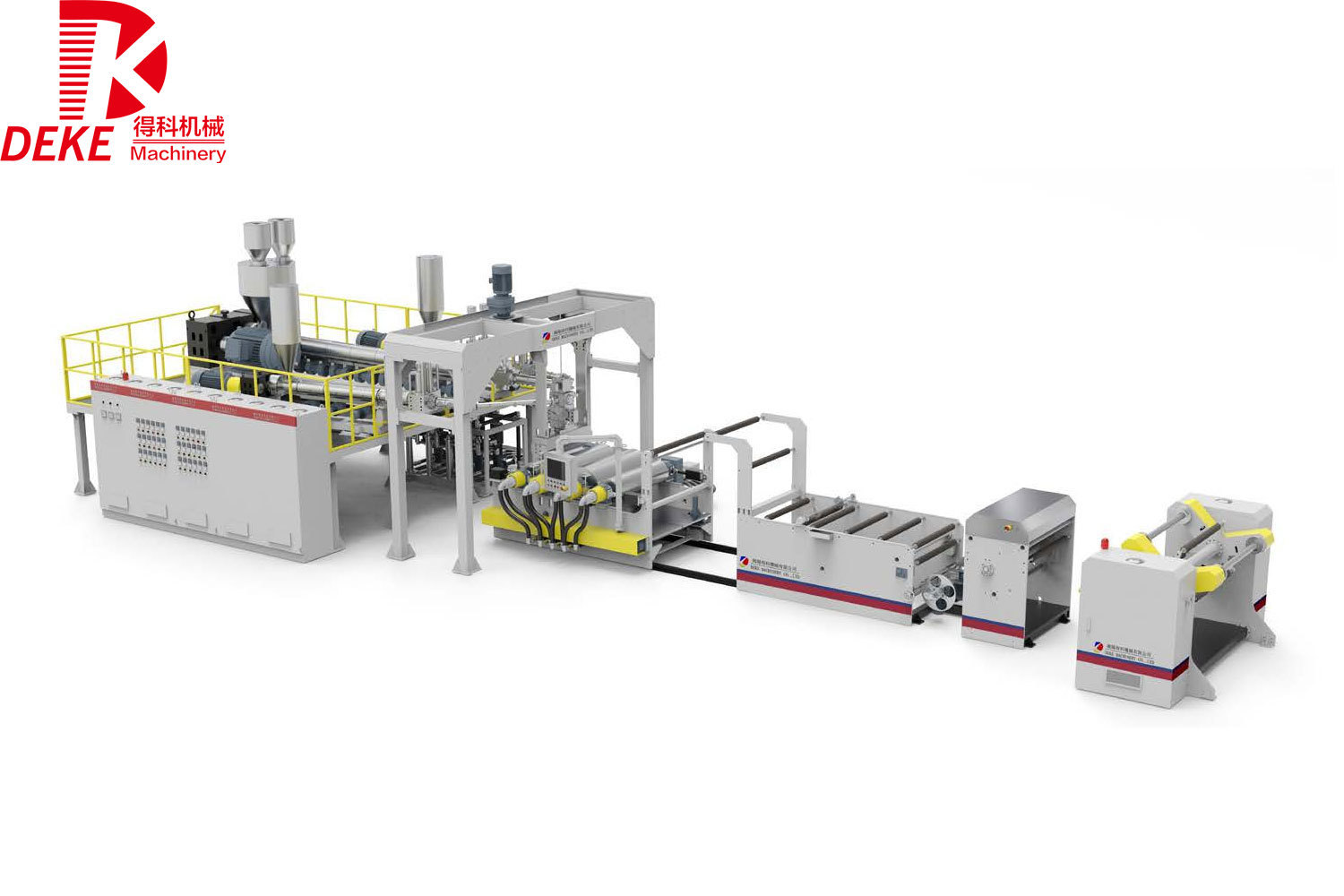
Unveiling the Critical Role of EVOH in High Barrier Sheet Extrusion
Table of Contents
- 1. Introduction to High Barrier Sheet Extrusion
- 2. What is EVOH?
- 3. Properties of EVOH: Why It Matters
- 4. Applications of EVOH in Packaging
- 5. Advantages of Using EVOH in High Barrier Sheets
- 6. The Sustainability Aspect of EVOH
- 7. EVOH in the Manufacturing Process of Extrusion
- 8. Future Trends in EVOH Technology for Extrusion
- 9. FAQs
- 10. Conclusion
1. Introduction to High Barrier Sheet Extrusion
In the realm of plastic manufacturing, high barrier sheet extrusion is a pivotal process that demands precision and innovation. This method is vital for producing sheets that provide exceptional resistance to gases and moisture, significantly extending the shelf life of various products. In recent years, the incorporation of **Ethylene Vinyl Alcohol (EVOH)** has emerged as a game-changer, revolutionizing how we approach high barrier solutions. As we delve deeper into the significance of EVOH, we'll uncover its unique characteristics and how it enhances the performance of high barrier sheets.
2. What is EVOH?
EVOH, or Ethylene Vinyl Alcohol, is a copolymer that results from the polymerization of ethylene and vinyl alcohol. This material is renowned for its excellent barrier properties, particularly against oxygen, carbon dioxide, and other gases. Because of its unique molecular structure, EVOH offers a superior balance of flexibility and strength, making it ideal for various applications in the packaging industry. The composition of EVOH allows it to be processed at relatively low temperatures while maintaining its integrity and performance.
3. Properties of EVOH: Why It Matters
Understanding the properties of EVOH is essential for recognizing its value in high barrier sheet extrusion. Below are the key attributes that make EVOH a standout material:
3.1 Exceptional Gas Barrier Performance
EVOH exhibits outstanding barrier properties, particularly against oxygen permeation, which is crucial for preserving the freshness of food products. Its effectiveness is not limited to oxygen; it also provides excellent resistance to carbon dioxide and other gases.
3.2 Moisture Resistance
In addition to its gas barrier capabilities, EVOH offers substantial resistance to moisture, making it an ideal choice for products that require protection from humidity and moisture-related degradation.
3.3 Chemical Resistance
EVOH is chemically resistant, which means it maintains its properties even when exposed to various chemicals and solvents. This durability is essential for packaging applications that require long-term stability.
3.4 Versatility and Processability
EVOH can be blended with other polymers to create composite materials that enhance processing capabilities while retaining barrier properties, making it versatile for various manufacturing processes.
4. Applications of EVOH in Packaging
EVOH plays a crucial role in the packaging sector, where its unique properties are harnessed to create high-performance solutions. Some notable applications include:
4.1 Food Packaging
In the food industry, EVOH is widely used in packaging films and containers due to its ability to prolong shelf life by protecting against oxygen and moisture infiltration. This application is critical for perishable items such as meats, cheeses, and ready-to-eat meals.
4.2 Pharmaceutical Packaging
EVOH is increasingly employed in the pharmaceutical sector, where it is vital for ensuring the stability and efficacy of medications. Its ability to prevent moisture and gas exchange is particularly beneficial for sensitive compounds.
4.3 Electronics Packaging
In the electronics industry, EVOH is utilized in packaging materials that safeguard sensitive components from moisture and dust, ensuring product reliability and longevity.
5. Advantages of Using EVOH in High Barrier Sheets
The adoption of EVOH in high barrier sheets offers numerous advantages that resonate with manufacturers and consumers alike. Below are some of the primary benefits:
5.1 Enhanced Protection for Products
EVOH significantly enhances the protective qualities of high barrier sheets, ensuring that products maintain their quality over extended periods. This is especially important in industries where product integrity is paramount.
5.2 Cost-Effectiveness
By improving the shelf life of products, EVOH helps manufacturers reduce waste and minimize costs associated with returns and spoiled goods. This cost-effectiveness contributes to overall profitability.
5.3 Lightweight Solution
EVOH-based high barrier sheets are lighter than traditional materials, which can lead to reduced transportation costs and lower carbon emissions, benefiting both the environment and businesses.
5.4 Consumer Appeal
With increasing consumer awareness regarding sustainability and product quality, using EVOH in packaging can enhance brand reputation and attract environmentally conscious consumers.
6. The Sustainability Aspect of EVOH
Sustainability is a pressing concern across industries, and EVOH contributes positively in this regard. Here’s how:
6.1 Reduced Environmental Impact
EVOH’s ability to extend product shelf life means less food waste, which directly correlates to a reduction in overall environmental impact. Less waste means fewer resources consumed and less strain on landfills.
6.2 Recyclability
EVOH can be incorporated into recyclable packaging systems, making it an attractive option for companies striving to meet sustainability goals.
6.3 Biodegradable Alternatives
Research is ongoing into developing biodegradable versions of EVOH, which could further enhance its sustainability profile. This development will align with global efforts to reduce plastic waste and promote eco-friendly materials.
7. EVOH in the Manufacturing Process of Extrusion
The integration of EVOH in high barrier sheet extrusion involves several critical steps. Understanding these processes can provide insight into how manufacturers can optimize production.
7.1 Material Selection
Choosing the right grade of EVOH is essential for achieving the desired barrier performance and processing characteristics. Manufacturers must consider factors such as thickness, application, and environmental conditions.
7.2 Blending and Compounding
EVOH is often blended with other polymers to enhance its properties. This step involves precise compounding to ensure uniform distribution of EVOH within the polymer matrix, which is vital for maintaining barrier performance.
7.3 Extrusion Process
During extrusion, the blended material is heated and forced through a die to form sheets. Controlling temperature and pressure is crucial to prevent degradation of EVOH while achieving the desired sheet thickness and quality.
7.4 Post-Processing Techniques
Post-processing techniques, such as lamination and coatings, can further enhance the barrier properties of EVOH sheets and improve overall product performance.
8. Future Trends in EVOH Technology for Extrusion
As technology continues to evolve, so does the role of EVOH in high barrier sheet extrusion. Here are some emerging trends:
8.1 Innovation in Material Science
Ongoing research into new formulations of EVOH aims to enhance its barrier properties further while reducing production costs. This innovation will lead to more competitive materials in the market.
8.2 Integration of Smart Packaging Solutions
The incorporation of EVOH into smart packaging systems that utilize sensors and indicators can provide real-time information about product freshness, ensuring optimal quality for consumers.
8.3 Advances in Recycling Technologies
As recycling technologies advance, the ability to recycle EVOH materials will improve, paving the way for a more sustainable future in packaging.
9. FAQs
9.1 What is the primary use of EVOH in packaging?
EVOH is primarily used for its exceptional barrier properties in food and pharmaceutical packaging, ensuring product freshness and stability.
9.2 How does EVOH compare to other barrier materials?
EVOH offers superior gas and moisture barrier properties compared to many traditional materials, making it a preferred choice for applications that require high protection.
9.3 Is EVOH environmentally friendly?
Yes, EVOH contributes to sustainability by extending product shelf life and can be incorporated into recyclable packaging systems.
9.4 Can EVOH be used in high-temperature applications?
EVOH has limitations in high-temperature applications; it is essential to select appropriate grades and assess their performance under specific conditions.
9.5 What trends are shaping the future of EVOH in packaging?
Future trends include innovations in material science, smart packaging integration, and advancements in recycling technologies, all aiming to enhance EVOH's utility and sustainability.
10. Conclusion
The integration of **EVOH** in high barrier sheet extrusion is not merely an enhancement in material technology; it represents a paradigm shift in how we approach packaging solutions. With its unparalleled gas and moisture barrier properties, EVOH stands at the forefront of innovations that not only safeguard product integrity but also address sustainability concerns. As we move forward, the role of EVOH will continue to evolve, driven by technological advancements and the growing demand for sustainable packaging solutions. Embracing EVOH enables manufacturers to meet the challenges of today while paving the way for a more sustainable and efficient future in plastic processing.
Previous Page:
Next page:
RELATED INFORMATION
Understanding the Benefits and Functionality of Parallel Twin Screw Extruders
Parallel twin screw extruders are specialized machines widely used in the plastic processing industry. As the name suggests, these extruders feature two parallel screws that rotate synchronously within a barrel, providing a unique method of material handling and processing. This design allows for enhanced mixing, compounding, and extrusion of a variety of materials, making them an essential tool f
Exploring the Mechanisms Behind Parallel Twin Screw Extruders: A Comprehensive Guide
Exploring the Mechanisms Behind Parallel Twin Screw Extruders Table of Contents Introduction to Parallel Twin Screw Extruders Understanding the Structure of Parallel Twin Screw Extruders Mechanical Principles of Extrusion Advantages of Parallel Twin Screw Extruders Applications in the Plastic Processing Industry Common Challenges and Solutions Maintenance and Optimizat