Choosing the Right Parallel Twin Screw Extruder for Your Needs
2025-05
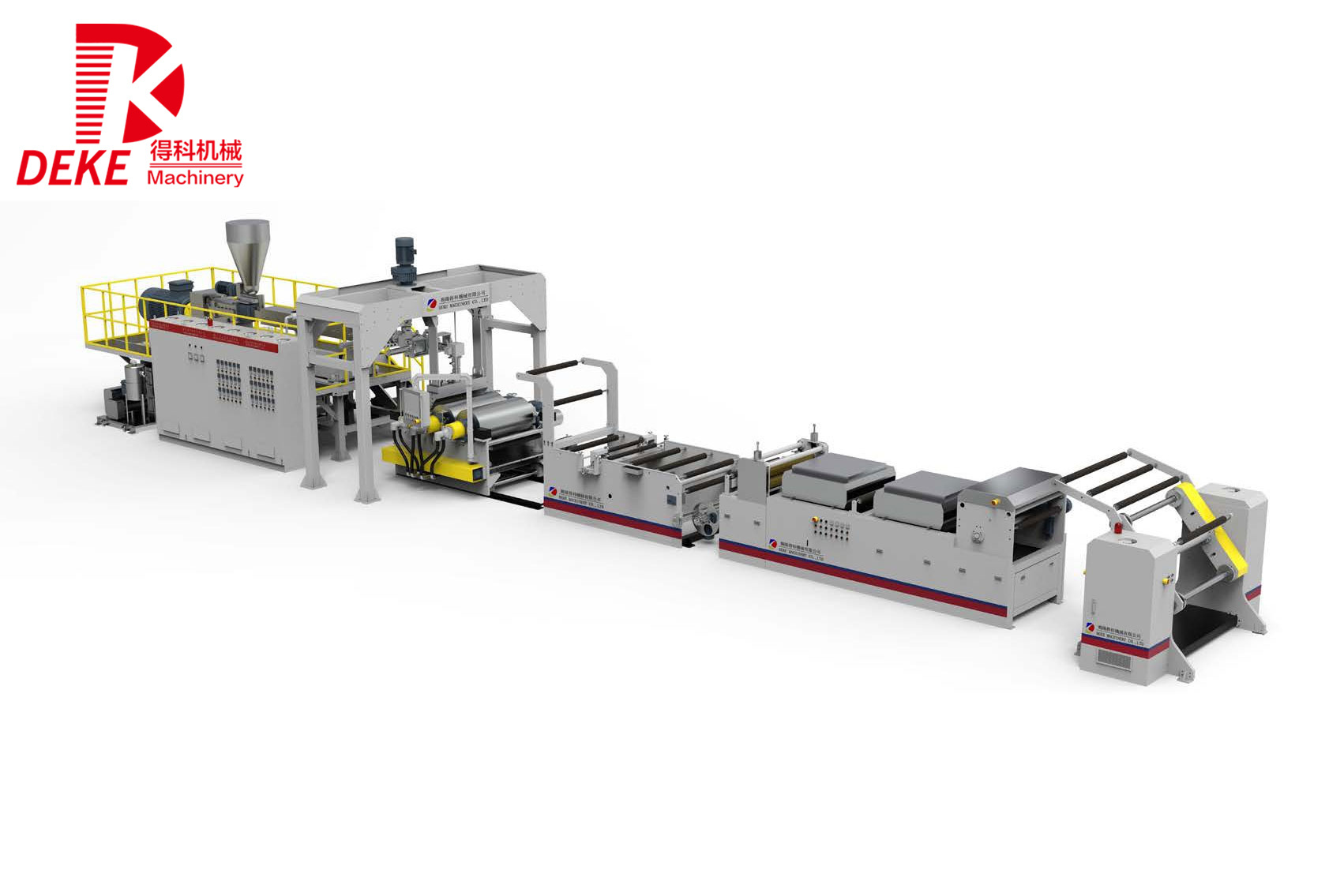
Choosing the Right Parallel Twin Screw Extruder for Your Needs
Table of Contents
- Understanding Parallel Twin Screw Extruders
- Applications and Industries Using Extruders
- Key Components of a Parallel Twin Screw Extruder
- Considerations for Choosing the Right Extruder
- Different Types of Parallel Twin Screw Extruders
- Performance Evaluation of Extruders
- Maintenance and Support for Extruders
- Frequently Asked Questions
Understanding Parallel Twin Screw Extruders
Parallel twin screw extruders are advanced machines widely utilized in the plastics processing industry. They are characterized by two intermeshing screws rotating in parallel, which significantly enhances the mixing and melting of materials. This design allows for effective material handling, making it ideal for a variety of applications, including compounding, pelletizing, and molding.
The **principle of operation** involves the feed material entering the machine through a hopper, where it is subjected to shear and pressure generated by the screws. This process results in a homogenous melt that can be formed into various shapes or pellets, depending on the downstream processes.
Applications and Industries Using Extruders
Parallel twin screw extruders are pivotal in numerous sectors, including:
1. Plastics Manufacturing
In the plastics industry, these extruders are extensively used for processing thermoplastics, thermosets, and elastomers. Their ability to handle a wide range of materials makes them indispensable in producing plastic sheets, films, and profiles.
2. Food Processing
The food industry employs parallel twin screw extruders for tasks such as snack food production and the extrusion of pasta and pet food. Their ability to provide consistent product quality and precise control of processing conditions is crucial in food applications.
3. Pharmaceutical and Chemical Industries
In pharmaceuticals, these extruders are used for granulation and drug delivery systems. Their precise mixing capabilities enable the formulation of consistent and effective drug products.
Key Components of a Parallel Twin Screw Extruder
Understanding the essential components of a parallel twin screw extruder can help in selecting the right machine for your needs.
1. Screw Design
The screw design significantly influences the extruder's performance. Different configurations (such as mixing elements, conveying elements, and kneading blocks) can be employed to optimize the process for specific materials.
2. Barrel Design
The barrel's construction, often made of hardened steel, affects heat transfer and material flow. The option for adjustable heating zones can provide better temperature control during processing.
3. Drive System
The drive system must provide sufficient torque and speed to handle various materials efficiently. Gearbox configurations and motor choices can impact the overall performance of the extruder.
4. Control Systems
Modern extruders come equipped with advanced control systems that enable precise monitoring and adjustment of parameters, including temperature, pressure, and feed rate. This level of control ensures consistent product quality.
Considerations for Choosing the Right Extruder
Selecting the right parallel twin screw extruder requires careful consideration of several factors:
1. Material Characteristics
Different materials exhibit unique processing behaviors. Understanding the thermal and rheological properties of the materials you plan to extrude will guide your choice of screw design and processing conditions.
2. Production Volume
Consider your production capacity needs. High-volume applications may necessitate larger extruders with higher throughput capabilities, while smaller operations might benefit from more compact machines.
3. Desired Product Specifications
Define the end product specifications, such as dimensions, surface finish, and mechanical properties. This information will help you identify the features necessary in an extruder to meet these specifications.
4. Budget Constraints
Establishing a budget is crucial. While advanced features may enhance performance, they also come at a higher cost. Balancing your budget with the required specifications is key to making a sound decision.
Different Types of Parallel Twin Screw Extruders
Parallel twin screw extruders come in various designs to suit different applications:
1. Co-rotating Extruders
In co-rotating extruders, both screws rotate in the same direction. This configuration enhances mixing and is suitable for applications requiring extensive material blending and high shear.
2. Counter-rotating Extruders
Counter-rotating extruders feature screws that rotate in opposite directions. This design can provide excellent material conveyance and is often used for processes that require lower shear forces.
3. Intermeshing vs. Non-Intermeshing
Intermeshing extruders have screws that mesh together, providing superior mixing. Non-intermeshing designs can be more effective in processes where material degradation must be minimized.
Performance Evaluation of Extruders
Evaluating the performance of a parallel twin screw extruder involves examining several critical metrics:
1. Throughput
Throughput measures the amount of material processed over time. Higher throughput indicates a more efficient extruder, essential for meeting production demands.
2. Energy Efficiency
Energy consumption is a vital consideration, as it directly impacts operational costs. An energy-efficient extruder can significantly reduce overall production expenses.
3. Product Quality
Assessing the quality of the extrudate is crucial. Consistency in size, shape, and material properties reflects the effectiveness of the extruder and its suitability for your application.
Maintenance and Support for Extruders
Regular maintenance is essential to ensure the longevity and performance of your extruder:
1. Routine Maintenance Practices
Establish a maintenance schedule that includes regular inspections, cleaning, and part replacements. This practice can prevent costly breakdowns and keep the extruder operating at peak performance.
2. Manufacturer Support
Selecting a manufacturer that offers robust customer support and service options can make a significant difference. Access to technical support and spare parts ensures you can address any issues promptly.
Frequently Asked Questions
1. What materials can be processed with a parallel twin screw extruder?
Parallel twin screw extruders can process a wide range of thermoplastics, thermosets, and even some elastomers, depending on their design and configuration.
2. How do I determine the right screw design for my application?
The right screw design depends on the material characteristics and the desired product outcome. Consulting with a manufacturer or expert can provide valuable insights.
3. What is the typical lifespan of a parallel twin screw extruder?
With proper maintenance, a well-built parallel twin screw extruder can last for many years, often exceeding a decade or more in industrial applications.
4. Are there customizable options available for parallel twin screw extruders?
Yes, many manufacturers offer customizable features, including screw design, barrel length, and heating zones, to fit specific processing needs.
5. How does a parallel twin screw extruder compare to a single screw extruder?
Parallel twin screw extruders typically offer better mixing and temperature control, making them more suitable for complex processing applications compared to single screw extruders.
Conclusion
Selecting the right parallel twin screw extruder for your needs involves a thorough understanding of your material characteristics, production requirements, and desired product specifications. By considering key factors such as screw design, barrel construction, and operational efficiency, you can make an informed choice that maximizes productivity and product quality. From food processing to plastics manufacturing, these machines play a critical role in modern production, making the right selection crucial for success. Regular maintenance and support are also vital for sustaining performance over time. With the right parallel twin screw extruder, you can achieve optimal results for your specific manufacturing needs.
Previous Page:
RELATED INFORMATION
Choosing the Right Parallel Twin Screw Extruder for Your Needs
Choosing the Right Parallel Twin Screw Extruder for Your Needs Table of Contents Understanding Parallel Twin Screw Extruders Applications and Industries Using Extruders Key Components of a Parallel Twin Screw Extruder Considerations for Choosing the Right Extruder Different Types of Parallel Twin Screw Extruders Performance Evaluation of Extruders Maintenance and Suppo
Understanding the Benefits and Applications of Parallel Twin Screw Extruders
In the realm of plastic processing machinery, the parallel twin screw extruder stands out as a versatile and effective solution for a variety of applications. This type of extruder is characterized by two screws that run parallel to each other, allowing for efficient melting, mixing, and compounding of materials. The design of the parallel twin screw extruder enables a uniform and consistent outpu