Unlocking the Benefits of PET Twin Screw Extruders in Plastic Processing
2025-04
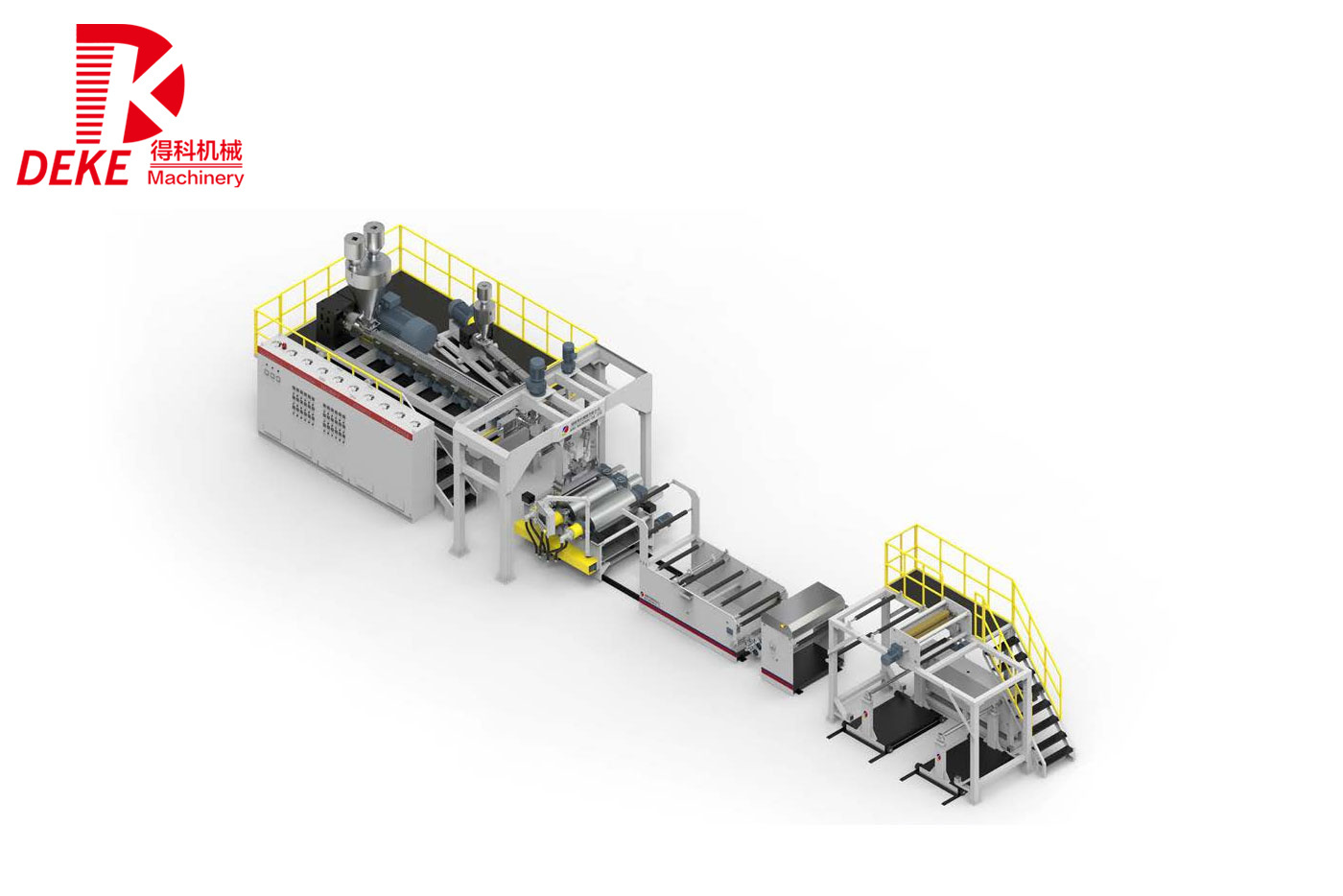
Unlocking the Benefits of PET Twin Screw Extruders in Plastic Processing
Introduction to PET Twin Screw Extruders
In the world of plastic processing, **polyethylene terephthalate (PET)** has emerged as a leading material due to its excellent mechanical properties and versatility. **PET twin screw extruders** play a pivotal role in efficiently processing this thermoplastic material. These advanced machines are designed to provide superior mixing, compounding, and pelletizing capabilities, making them invaluable in various applications, including packaging, automotive components, and consumer goods.
The Importance of Choosing the Right Extruder
Selecting the correct extruder is crucial for optimizing production efficiency. The **PET twin screw extruder** stands out due to its unique design, which allows for better material handling and enhanced thermal control. In this section, we will explore the features that differentiate twin screw extruders from their single screw counterparts.
Design and Mechanism of Twin Screw Extruders
A twin screw extruder consists of two intermeshing screws that rotate in the same or opposite directions, depending on the application. This design promotes:
- **Increased mixing efficiency**: The intermeshing screws create a more homogeneous material blend.
- **Better control of processing conditions**: Precise temperature and pressure management ensures an optimal processing environment for PET.
Applications of PET Twin Screw Extruders
The versatility of PET twin screw extruders allows them to be utilized in various applications, including:
- **Film and sheet production**: For packaging and protective materials.
- **Injection molding**: Creating durable automotive and household components.
- **Filament production**: For 3D printing and other innovative technologies.
Key Benefits of Using PET Twin Screw Extruders
Adopting PET twin screw extruders in your plastic processing operations can yield numerous benefits, leading to increased productivity and cost savings.
1. Enhanced Processing Efficiency
The **high shear forces** generated by twin screw extruders facilitate faster melting and mixing of PET. This results in reduced cycle times and increased output, allowing manufacturers to meet demanding production schedules.
2. Superior Material Quality
When processing PET, maintaining material quality is a top priority. Twin screw extruders minimize thermal degradation and ensure uniformity in the final product. This is particularly important for applications requiring high clarity and strength.
3. Flexibility in Formulation
One of the standout features of twin screw extruders is their ability to handle various additives and fillers. Whether incorporating colorants, nucleating agents, or reinforcing materials, these extruders provide the flexibility needed to customize PET formulations.
4. Energy Efficiency
Modern PET twin screw extruders are designed with energy efficiency in mind. Innovative technologies help minimize energy consumption while maximizing output, leading to a lower carbon footprint and reduced operational costs.
5. Environmentally Friendly Processing
As sustainability becomes increasingly important, the use of twin screw extruders in PET processing aligns with eco-friendly practices. The ability to use recycled PET, combined with the efficient processing capabilities, contributes to a more sustainable manufacturing approach.
Challenges in PET Processing and How Twin Screw Extruders Address Them
While PET offers numerous advantages, processing this material can present challenges. Twin screw extruders effectively tackle several of these issues.
Dealing with Viscosity Variations
The viscosity of PET can vary significantly based on molecular weight and processing conditions. Twin screw extruders allow for precise control over temperature and shear rates, facilitating the handling of different viscosity levels without compromising quality.
Minimizing Degradation and Contamination
Thermal degradation is a concern when processing PET. Twin screw extruders feature advanced temperature control systems that minimize overheating. Additionally, the enclosed design reduces the risk of contamination, ensuring purity in the final product.
The Future of PET Twin Screw Extruders
As technology continues to evolve, the future of PET twin screw extruders looks promising. Innovations in design and automation are on the horizon, aimed at further improving efficiency and reducing operational costs.
Trends in Automation and Control
The integration of smart technologies into twin screw extruders promises enhanced control over the processing environment. Real-time monitoring and data analytics will enable manufacturers to make informed adjustments, leading to improved product quality and consistency.
Growing Demand for Sustainable Solutions
As industries increasingly prioritize sustainability, the demand for PET twin screw extruders capable of processing recycled materials will grow. Manufacturers that invest in these technologies will be well-positioned to meet market expectations.
Choosing the Right PET Twin Screw Extruder for Your Needs
Selecting the appropriate twin screw extruder is essential for optimizing your production process. Consider the following factors:
1. Production Scale
Determine the scale of your operations. Manufacturers should choose an extruder that meets their production capacity while providing the necessary performance characteristics.
2. Application Requirements
Different applications may require specific configurations of twin screw extruders. Assess your processing needs to ensure compatibility with the desired end products.
3. Budget Considerations
Investing in a PET twin screw extruder represents a significant capital expenditure. Evaluate your budget and consider potential long-term savings through increased efficiency and reduced waste.
FAQs About PET Twin Screw Extruders
1. What materials can be processed with PET twin screw extruders?
PET twin screw extruders are highly versatile and can process various thermoplastics, including recycled materials and a range of additives for customization.
2. How does temperature control affect PET processing?
Effective temperature control prevents thermal degradation and ensures optimal melting and mixing of PET, leading to high-quality end products.
3. Can PET twin screw extruders handle colorants and additives?
Yes, twin screw extruders are designed to accommodate various colorants, fillers, and additives, allowing for customized formulations.
4. What is the typical output of a PET twin screw extruder?
Output varies based on the specific model and production requirements, but many PET twin screw extruders are capable of producing several hundred kilograms per hour.
5. Are there maintenance requirements for PET twin screw extruders?
Regular maintenance is essential for optimal performance. This includes cleaning, lubrication, and inspection of components to prevent wear and tear.
Conclusion
In conclusion, **PET twin screw extruders** represent a transformative force in the plastic processing industry. Their ability to enhance efficiency, improve material quality, and provide flexibility in formulation makes them an essential investment for manufacturers looking to optimize their operations. As the demand for sustainable solutions continues to grow, investing in advanced twin screw extruders will position your business for future success. Embracing these technologies not only enhances productivity but also contributes to a more sustainable manufacturing landscape.
RELATED INFORMATION
Understanding the Benefits and Applications of Parallel Twin Screw Extruders
In the realm of plastic processing machinery, the parallel twin screw extruder stands out as a versatile and effective solution for a variety of applications. This type of extruder is characterized by two screws that run parallel to each other, allowing for efficient melting, mixing, and compounding of materials. The design of the parallel twin screw extruder enables a uniform and consistent outpu
Innovative Applications of Parallel Twin Screw Extruder Technology in Modern Manufacturing
Innovative Applications of Parallel Twin Screw Extruder Technology Introduction to Parallel Twin Screw Extruders The **parallel twin screw extruder** has emerged as a pivotal technology in the realm of manufacturing, particularly within the plastic processing sector. Characterized by two intermeshing screws rotating in the same direction, these extruders are designed to efficiently mix, melt, and